Frequently Asked Questions About Galvorn
Below we address questions commonly asked about Galvorn carbon nanomaterial.
Yes. Galvorn is pure carbon. Carbon can come in many physical forms, for example, Graphene, charcoal… and carbon nanotubes!
A carbon nanotube (CNT) is a tube made of carbon. When graphene sheets form into cylindrical tubes this is what we call a carbon nanotube. CNTs measure in the nanometer range, think "nanoscale."
High quality CNTs have a single-walled (or very few-walled) structure. Multi-walled CNTs have more defects and lower performance properties.
Galvorn is a carbon nanomaterial. The CNTs that form it are densely packed and highly aligned, which is is how it is able to achieve superior properties.
Galvorn is produced using a wet fiber spinning process. As a point of reference, Kevlar uses this same type of process. Carbon nanotubes are dissolved into a liquid solution and then extruded through a spinneret to form fibers.
DexMat’s proprietary process ensures that the carbon nanotubes are highly aligned and thus exhibit the high-performance properties we see today. Learn more about how we make Galvorn.
No. By volume Galvorn’s conductivity today is about 1/6th that of copper and 1/3rd that of aluminum.
Conductivity by volume:
- Galvorn: 10 MS/m
- Copper: 58 MS/m
- Aluminum: 33 MS/m
However, in the real world material properties are never considered in isolation. There are many conductive applications for which copper's other properties render it inadequate. For example, power transmission lines use aluminum instead of copper because copper is too heavy and brittle. Even aluminum is deeply flawed for that application, which is why it must be supported by a steel core.
It is also why DexMat won a DOE grant to develop stronger, lighter power transmission lines using Galvorn to replace the heavy steel core. Eventually, we hope to replace the aluminum as well.
Galvorn actually exceeds copper's conductivity for high frequency applications, such as radio antennas and wireless chargers. Again, the application context is paramount.
Galvorn’s true power is that it has a combination of historically valued properties: super strong, lightweight, conductive, flexible, flame resistant, and more.
Highly unlikely. Galvorn’s conductivity has been doubling approximately every three years. Research thus far can attribute the improvements to better feedstock material and processing.
Galvorn has only reached ~10% of its theoretical maximum conductivity. That theoretical limit is the performance properties exhibited at the nanoscale.
Let’s put that into historical context. Carbon nanotubes were only discovered relatively recently in 1991. Carbon nanotube fibers were first spun in 2013 (by members of our very own team no less!).
Compare that to copper, which has been around since 8000 B.C. And aluminum, which was first discovered in the 1820s. The conductivity of copper and aluminum have each reached their peak centuries and decades ago, respectively. As we continue to improve our processing, we expect to see improvements in properties, as has been the case for the last 10+ years.
Think of materials not just in their standalone properties, but instead consider, “What does it take to get the job done?” And, critically, what is the emissions tradeoff? Below you can see the conductivity of materials on a per mass basis. Galvorn is comparable to copper and about half that of aluminum.
Specific conductivity:
- Galvorn: 6150 Sm2/kg
- Copper: 6300 Sm2/kg
- Aluminum: 12,200 Sm2/kg
Consider the emissions to conduct the same amount of electricity with the same resistance. Galvorn can get the job done with far less negative impact on our environment. Although Galvorn has a lower specific conductivity than copper or aluminum, their displacement leads to lower emissions. This is true even if you need more Galvorn to conduct the same amount of electricity.
Above: Estimated 2035 emissions. Galvorn's emissions today are higher because of its smaller scale (typical of materials production). At full scale, process efficiencies improve and significantly reduce the energy required to produce it. Contact us to learn more about our techno-economic analysis.
Yes, in some cases it may. But reimagining how a product is designed to achieve the same or better application goal is common for new materials.
Also, as we're learning from customers, there are many conductive applications for which copper is actually over-engineered. Applications like data transmission cables, which consume massive amounts of material in data centers, vehicles, and consumer electronics, require much less conductivity than copper.
And as previously mentioned, there are many conductive applications for which copper's other properties render it inadequate. The application context is paramount.
Galvorn production has low energy intensity with a clean energy byproduct, hydrogen. Today Galvorn’s feedstock is produced from methane (CH4). The hydrocarbon is split into carbon nanotubes (CNTs), a form of carbon, and hydrogen (H2). DexMat applies its proprietary process to turn these unstructured CNTs into the high-performance carbon nanomaterial, Galvorn.
Galvorn is fundamentally less energy and CO2 intensive to produce. Using it instead of dirty incumbent materials is how Galvorn can have the biggest impact.
If we set aside metals and other GHG-intensive materials displacement, however, the production of Galvorn can be "carbon negative" under certain circumstances. Galvorn has a carbon negative footprint (versus impact) when we use carbon negative feedstock.
We assess carbon feedstocks using Argonne National Lab’s GREET model. GREET ascribes -2.3 kg CO2 emissions per kg renewable natural gas (RNG) when produced from landfill gas. GREET has a publication describing their assessment of renewable natural gas (RNG) here.
Using a carbon negative feedstock is the only manner in which we claim a negative CO2 footprint (though we always claim a negative CO2 impact, due to metals displacement).
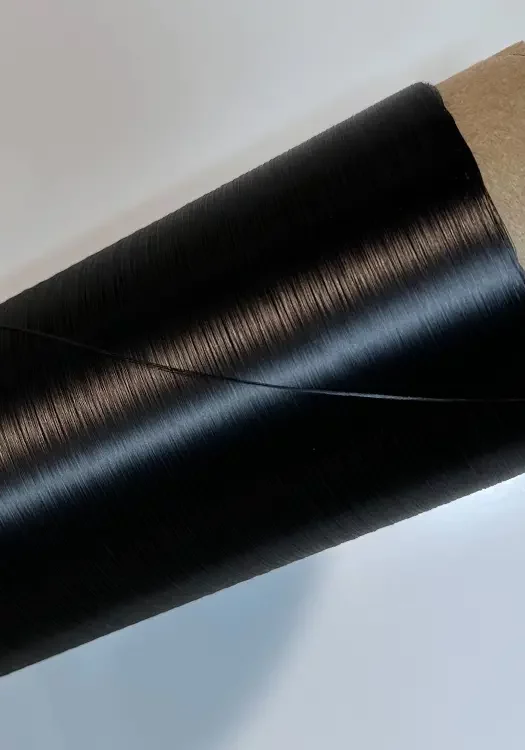