Galvorn Carbon Nanomaterial
A revolution in materials performance
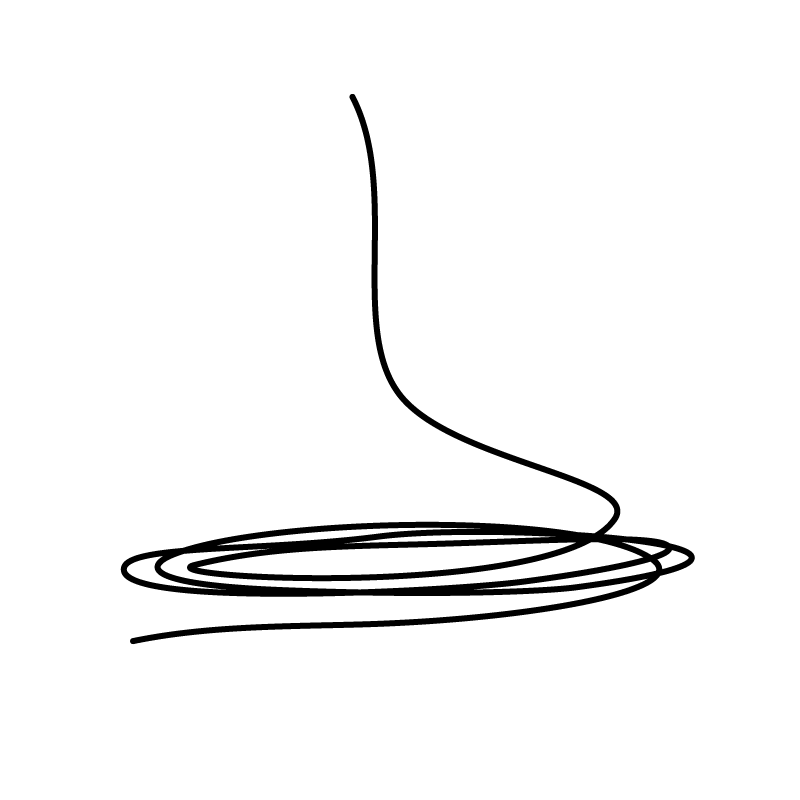
EXECUTIVE SUMMARY
We live in a material world.
From the protective garments we wear, to the electronics, cars, buildings, and bridges we construct and use in our day to day lives, materials play an existential role in our world. Yet for all our advancements in the discovery of new materials—plastics, fiberglass, carbon fiber, and more—our reliance on metals has thus far stood the test of time. Steel, aluminum, and copper alone make up 2% of the global economy.
In recent years, the environmental impact of materials has increasingly come under scrutiny. Be it the mile-wide holes in the ground or toxic chemicals leaking into them due to mining, the inefficiencies of the process (4-5 tons of dirt must be mined to produce a single gold bar), or the “forever chemicals” found in your hiking boots and waterproof gear—consumers and legislators are reflecting this newfound knowledge in their purchasing choices and policy demands.
It befalls product designers and developers to find materials that not only satisfy their high-performance applications, but also minimize the environmental impact of what they create.
Thus, it befalls product designers and developers to find materials that not only satisfy their high-performance applications, but also minimize—dare we hope, improve—the overall environmental impact of the things they create. It is not an easy task.
This white paper outlines the technical and environmental benefits that Galvorn carbon nanomaterials offer when high-performance meets carbon-negative impact at scale.
Carbon nanotubes: from hope to hype—to something real
Since their discovery in the 1990s, carbon nanotubes (CNTs) have become one of the most famous parts of the growing field of nanotechnology—for good reason. The idea that captured our imaginations? Harnessing CNTs’ unparalleled properties to create a new generation of materials that address some of our most vexing challenges.
Over the years, market hope turned to hype, which turned to disillusionment as the inherent difficulty of working with CNTs limited the number of applications in which they were successfully leveraged to make a tangible impact.
Nevertheless, research into CNTs continued to make steady progress. It has led to better production methods and a better understanding of their properties and how they might be exploited at the macroscale.
DexMat has achieved the ability to unlock the high-performance properties, exhibited at the nanoscale, for macroscale structures.
Today, the production of high-performance carbon nanomaterials is real, and they can be used to advance existing products and—perhaps more importantly—enable new ones.
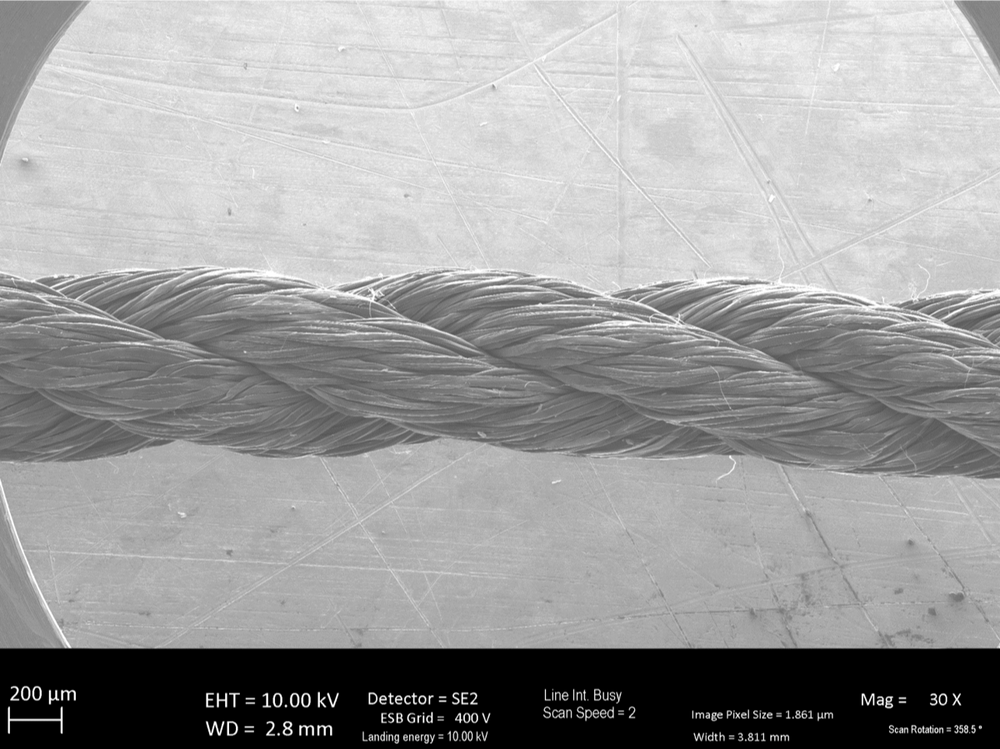
Above: Microscopic view of Galvorn carbon nanotube yarn.
Our team at DexMat achieved a breakthrough in CNT material science—the ability to unlock the high-performance properties, exhibited at the nanoscale, for macroscale structures. DexMat, Inc. was founded in 2019 to commercialize Galvorn, a carbon nanomaterial that combines superior strength, light weight, conductivity, flexibility, and more, outperforming GHG-intense alternatives. It is available for commercial use today in the form of fibers, yarns, films, fabrics, and composites.
What are carbon nanotubes and why are they important?
Carbon nanotubes (CNTs) have been one of the most well-known and widely-researched materials in the field of nanotechnology. Their outstanding molecular properties offer transformative opportunities for advanced materials.
Carbon nanotubes are tubes made of carbon with diameters that are measured in nanometers (“nanoscale”). They come in multiple forms, each suitable for different applications.
- Single-walled carbon nanotubes (SWCNTs) have diameters around 0.5–2.0 nanometers, about 100,000 times smaller than the width of a human hair.
- Multi-walled carbon nanotubes (MWCNTs) consist of single-wall carbon nanotubes nested together to form a tube-in-tube structure. Double- and triple-walled carbon nanotubes are variants of MWCNT.
High performance at nanoscale
An individual CNT has exceptionally high strength, electrical conductivity, and thermal conductivity, and its hollow cylindrical structure allows it to form sturdy and stable materials while maintaining a low density—all fantastic properties for high-performance materials.
Key to unlocking nanoscale properties at the macroscale is achieving control over the arrangement and interconnections between CNT molecules.
Carbon nanotube propertiesat the nanoscale:
- Tensile strength: > 110 GPa (Steel 5.2 GPa, Carbon Fiber 6.4 GPa )
- Electrical conductivity: ~ 100 MS/m (Cu 59 MS/m, Ag 63 MS/m)
- Thermal conductivity: ~ 3000 W/m-K (Diamond 2000 W/m-K)
- Low density: ~ 1.4 kg/m3 (Steel 8 kg/m3, Aluminum 2.7 kg/m3)
One of the keys to unlocking nanoscale properties at the macroscale is achieving control over the arrangement and interconnections between CNT molecules, including the density of packing and degree of alignment and order.
Commercially available CNTs
Today, CNTs are commercially available in a few different forms. Most CNTs that are available for purchase come in a disordered and entangled state that arose from random growth of the molecules during synthesis.
These often take the form of powders, or—in the case of very long CNT molecules—mats of material made up of entangled, non-aligned CNT molecules.
CNTs can also take the form of a vertically aligned array, in which CNT molecules were grown from a solid substrate and develop a rough vertical alignment due to their common direction of growth.
Commercial CNTs may be single-walled carbon nanotubes (SWCNTs), multi-walled carbon nanotubes (MWCNTs)—or a combination of both. CNTs can have a wide variety of molecular diameters and lengths, and typically a range of both values are present in any commercially available sample.
Not all CNTs are created equal
Different sources of CNTs also vary in purity (the amount of non-nanotube material included in the sample) and in molecular quality (the frequency of defects in their molecular structure). Purified samples, very high molecular quality samples, or even samples that have been sorted to contain only certain selected CNT types can each be obtained for a higher price. Sorted CNTs may sometimes be sold in the form of a liquid solution, since fluid and chemical processing steps are used in the process of sorting CNT types from one another. Given this variance in CNT type and quality, CNTs from a given commercial source may or may not be suitable for a given application.
Early commercial applications do not harness the true power of CNTs
The earliest commercial applications of CNTs focused on mixing particles of entangled, disorganized CNTs into other materials to increase the strength and flexibility of common commercial goods and coatings.
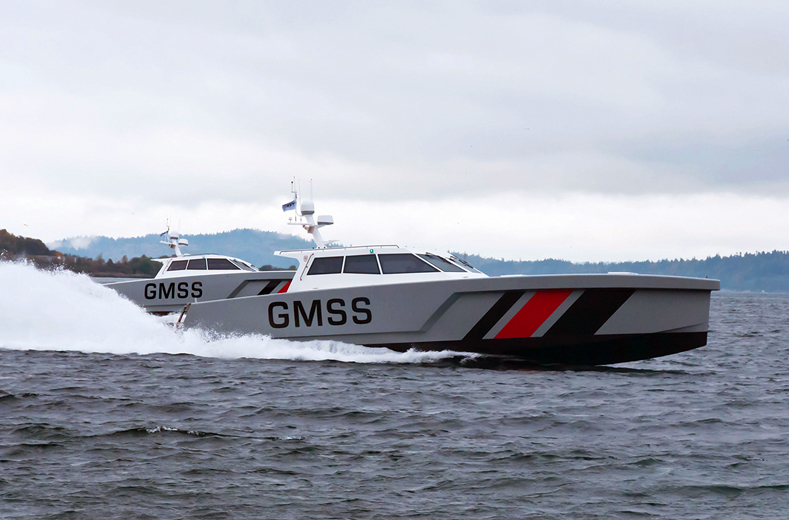
Source: NASA | Carbon Nanotube Resin Shores Up Boats, Bikes
CNTs have been used in this way to help strengthen composite materials like boat hulls or bicycle frames; some more recent incarnations of this type of product use CNT composites in additive manufacturing. Other applications for disorganized CNTs mixed into other materials include enhancement of the conductivity of thin film electronics and the formation of anti-corrosion coatings. These applications are often not very sensitive to the quality of the CNT material used, so they can be achieved through the use of less expensive CNT products with low quality or purity. However, they do not harness CNTs’ excellent mechanical or electrical properties.
Methods and techniques for making carbon nanotubes useful
Synthesizing CNTs into an aligned array can give them a more useful structure. CNT molecules tend to have strong adhesion to one another through van der Waals forces because of their relatively large and smooth surface areas. It is challenging to rearrange the molecules through processing since it is difficult to break apart the clumps and bundles present in the raw material.
On the other hand, these strong adhesive forces mean that once CNT molecules have been rearranged into a new solid structure, that structure will tend to be stable without the need for molecular cross-linking. An additional advantage of CNTs’ stable structure is that they can be recycled by disassembling and reassembling the CNTs again and again into new structures, rendering them a potentially perpetually recyclable material.
Examples of processed CNT structures include:
- Buckypaper, wherein raw CNTs have been compressed together into a thin sheet
- Yarns formed from drawing and twisting entangled mats or arrays of long CNTs
- Thin films formed by dispersing CNTs in solvents and surfactants and subsequently depositing them on a filter or solid surface.
- Single filament fibers, as well as yarns, braided yarns, and fabrics constructed from those fibers
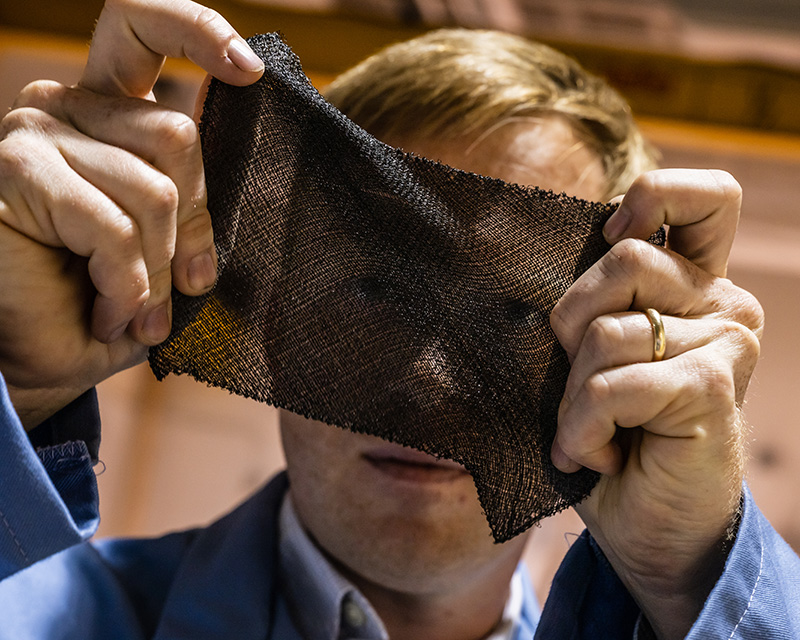
Above: Galvorn carbon nanotube fabric, constructed from single filament fibers twisted into yarn.
Different molecular structures suit different applications
Once CNTs have been processed into different structures they can be used for a wider variety of applications appropriate to their new forms. For example, a long chain of well-packed and well-aligned CNT molecules can serve very well as a high-strength fiber. This type of structure makes the best use of the combined mechanical strength of the molecules and the slip resistance of their long surfaces of contact, which increases the tensile strength of the fiber. Maximizing alignment and density of packing on a molecular level also enhances electrical and thermal contact between the constituent molecules, creating CNT materials with high thermal and electrical conductivity.
Galvorn unlocks nanoscale properties at macroscale
Galvorn carbon nanomaterials conduct electricity like metals, have the softness and flexibility of cotton, while being lightweight and corrosion resistant like polymers—and it is even flame-resistant. With a carbon-negative impact at scale, it offers the best of all worlds.
Galvorn carbon nanomaterials conduct electricity like metals, have the softness and flexibility of cotton, while being lightweight and corrosion resistant like polymers—and it is even flame-resistant. With a carbon-negative impact at scale, it offers the best of all worlds.
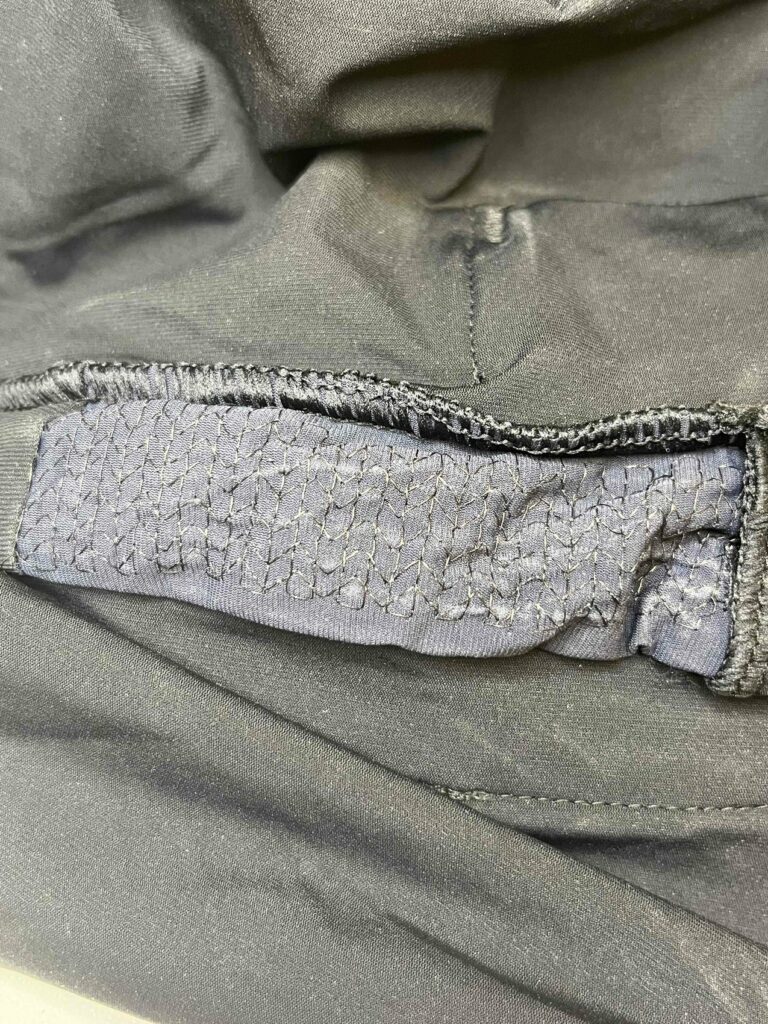
Above: Galvorn yarn, acting as electrodes, is embroidered into pieces of elastic fabric, which were then sewn into the interior lining of EKG vests and connected to a set of wires that carry signal to a recording device. Learn more.
Galvorn materials are composed of high-quality carbon nanotubes
Processing highly pure, high-quality CNTs as the raw material ensures the properties present at nanoscale continue to be present in the larger structured, useful form. We have found that this is one of the keys to achieving excellent material performance in Galvorn fibers and films.
To produce Galvorn we use solvents to mix CNT molecules into a solution, aligning the nanotubes and increasing their packing density. This allows us to use fluid processing techniques similar to those used by the polymer fiber industry (think Kevlar® or Dyneema®). This approach not only optimizes performance at the macroscale, but increases the techno-economic scalability of production.
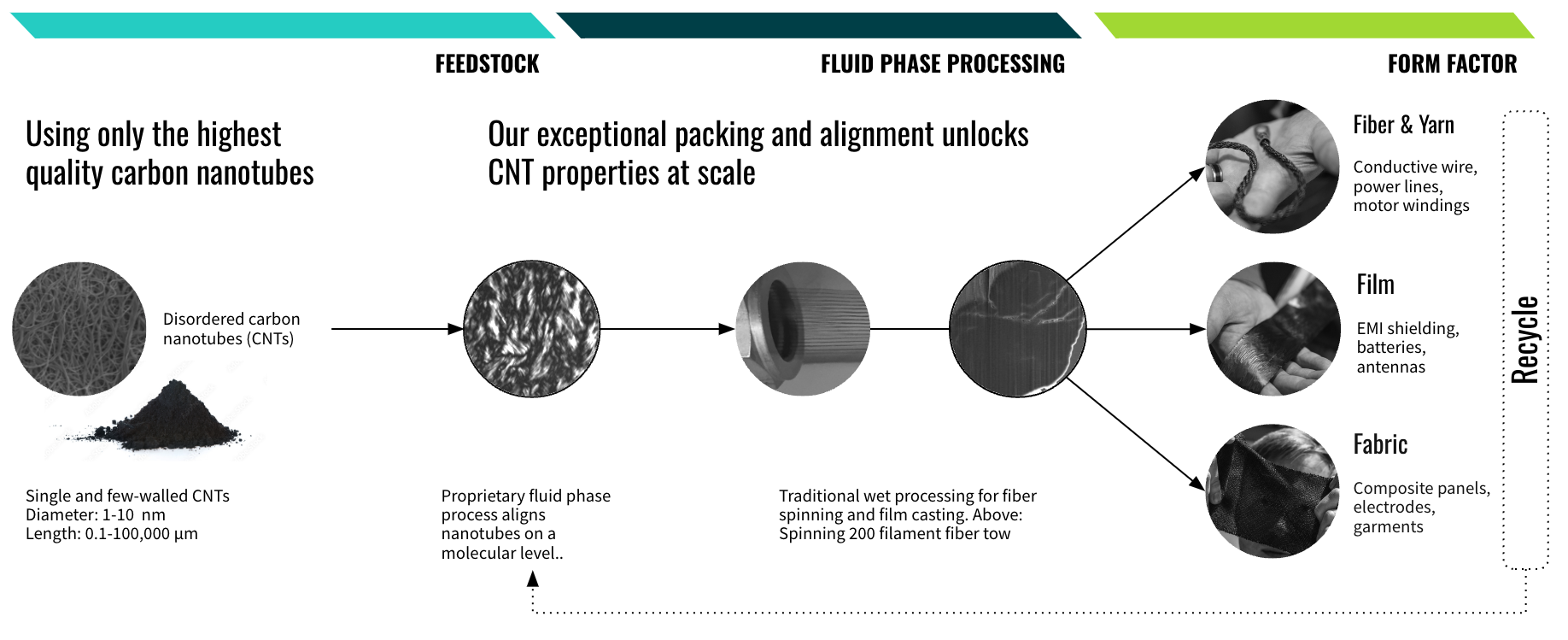
Galvorn has a carbon-negative impact at scale
Galvorn defies conventional climate wisdom because the more of this carbon nanomaterial we produce and use, the less climate impact industries have. Here’s how:
Today Galvorn can be made from hydrocarbons, capturing the carbon and co-producing hydrogen
By using methane (CH4) as a Galvorn feedstock in the near term, we’re preventing methane from directly entering the atmosphere (where it is a potent greenhouse gas–28x more potent than CO2!) and diverting it from combustion (where it would exhaust more carbon dioxide into the atmosphere).
Renewably powered manufacturing process on the horizon
Our production process uses electricity; when powered by renewable energy, it has a zero-emissions energy footprint.
In the future, Galvorn could be made from renewable natural gas and captured COâ‚‚
As a carbon-based material, Galvorn locks carbon into long-term storage, where it cannot contribute to global warming. By using renewable natural gas as a feedstock–and, in the longer term, using captured carbon dioxide (CO2) as technologies such as carbon dioxide removal (CDR) and direct air capture (DAC) mature and scale—Galvorn production has an even higher carbon negative impact.
Galvorn displaces dirty incumbent materials
By displacing steel, aluminum, copper, and other materials with a heavy climate footprint, we are pushing gigatons of carbon emissions out of global industry–and avoiding the need for environmentally destructive mining and intense chemical processing upon which today’s metals rely.
Clean hydrogen byproduct
Because the feedstock of Galvorn is developed through methane (CH4) pyrolysis—separating the carbon (C) from hydrogen (H4)—the primary byproduct of Galvorn production is clean hydrogen, itself a climate-friendly fuel and intermediate feedstock of green ammonia and other fuels.
Galvorn is available today for commercial applications
In addition to starting with a high-quality source of raw CNT materials, we optimize the potential of CNTs by aligning them into fibers and films. Then, using these formats, we can further construct them into yarns, fabrics, and composites.
Galvorn’s properties include high strength, electrical and thermal conductivity, and low density to create new opportunities in high-performance applications.
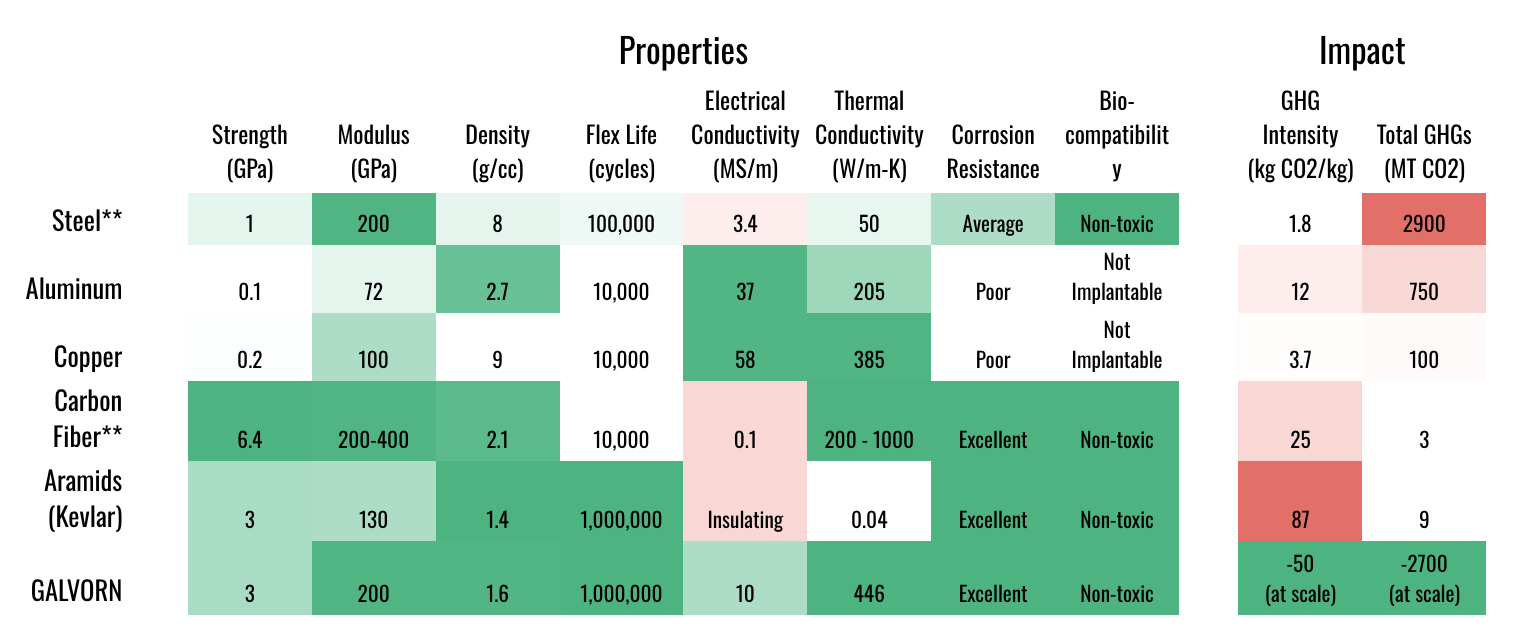
Note:** Properties noted here are for high-end forms of steel / carbon fiber.
Galvorn is a revolution in materials performance, enabling new opportunities in high-performance applications.
The commercial applications for Galvorn fibers, yarns, and films are boundless and include everything from cut-resistant gear to e-textiles to conductive composites and beyond. Below are a few highlights:
From our blog
Wires & Electronics
The Complete Guide to Galvorn Carbon Nanotube Wire and Cable
How Galvorn carbon nanomaterial can be used in data transfer applications
Wearables & E-Textiles
How Galvorn carbon nanomaterial can be used in electronic textiles
Aerospace
The Future of Aerospace Cables
Read our blog to learn more about commercial applications with Galvorn, as well as how it compares to dirty incumbent materials.
Combined with a production process that has a carbon-negative impact at scale, Galvorn represents a bold new opportunity for product designers and developers to usher the next generation of advanced high-performance materials for a low-carbon world.