Carbon Nanotubes vs Carbon Nanotube Fibers
In the early 2000s, carbon nanotubes (CNTs) generated immense excitement in the scientific, technological, and industrial communities due to their extraordinary properties. Carbon as a solid, CNTs were remarkably strong—approximately 100 times stronger than steel at a fraction of the weight—yet flexible, making them an ideal material for engineering. Additionally, their electrical conductivity surpassed that of copper, suggesting potential breakthroughs in electronics and "smart" devices. Their thermal conductivity also exceeded that of diamond. Combining all these properties into a single material, CNTs were hailed as a "wonder material."
By the mid-to-late 2000s, however, the CNT community began grappling with a sobering reality: translating the jaw-dropping properties of nanoscale CNTs into macroscale structures proved far more difficult than anticipated. The initial enthusiasm—built on the promise of superstrong, ultralight, and highly conductive materials—started to give way to disillusionment as researchers and engineers hit wall after wall in their attempts to use the wonder material for practical applications.
Over the course of this period, confusion about the differences between raw “nanoscale” CNTs and the useful “macroscale” structures that can be produced from them developed. This confusion persists today and too often obscures the genuine (and transformational) progress that has been made in the industry.
In this post we will clarify what is the difference between CNTs and their derived structures, why the difference matters, and why the advances in macroscale fiber structures are a game changer.
The Core Distinction: CNTs vs. Derived Structures
To understand the true potential of carbon nanotubes today, it's important to differentiate between raw carbon nanotubes and carbon nanotube fibers, and to recognize the contrast between the overstated expectations of the early 2000s and the transformative and practical possibilities that exist now.
Carbon Nanotubes (CNTs)
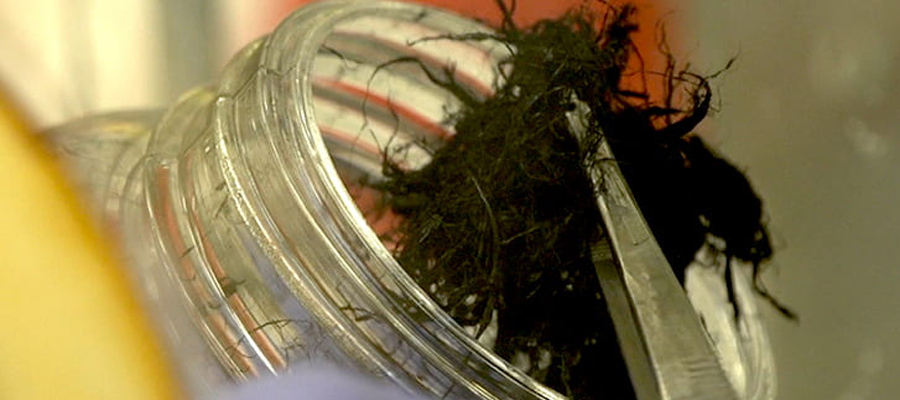
These are the fundamental building blocks—nanoscale, tubular structures of carbon atoms arranged in a hexagonal lattice. They are grown via methods like chemical vapor deposition (CVD) or arc discharge—taking the form of pure, standalone nanostructures.
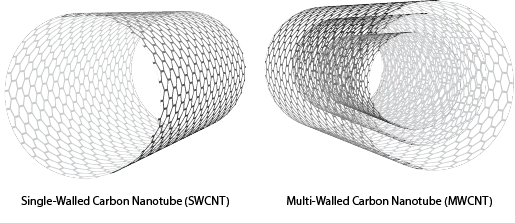
CNTs are individual molecules that look like rolled-up graphene sheets (i.e. “tubes”), typically 1-100 nanometers in diameter and 1,000-1,000,000 nanometers in length. These microscopic cylinders come in single-walled (SWCNT) or multi-walled (MWCNT) varieties, depending on how many layers are stacked within each other.
The Source of the 2000s Hype: Amazing Properties Exhibited at the Nanoscale
Carbon nanotubes (CNTs) are renowned for their remarkable properties, including superior strength-to-weight ratio compared to steel, exceptional electrical conductivity surpassing copper, and highly efficient heat dissipation—all in a very lightweight material. Since their discovery in 1991, scientists have envisioned their potential applications in a wide range of fields, from the development of ultra-strong composite materials to advancements in next-generation electronics. Below, are carbon nanotube properties at the nanoscale:
- Tensile strength: > 110 GPa (Steel 5.2 GPa, Carbon Fiber 6.4 GPa )
- Electrical conductivity: ~ 100 MS/m (Cu 59 MS/m, Ag 63 MS/m)
- Thermal conductivity: ~ 3000 W/m-K (Diamond 2000 W/m-K)
- Low density: ~ 1.4 kg/m3 (Steel 8 kg/m3, Aluminum 2.7 kg/m3)
But there’s a catch. Carbon nanotubes in their raw form have limited value. CNTs are tiny and they’re a pain to work with. For context, 100,000 CNTs are the width of a human hair. And they are highly disorganized; oriented every which way such that it’s hard to build anything with them at a usable scale.
Enter 2010s Disillusionment: CNTs Properties Are Just Out of Reach at the Macroscale
It turns out that forming CNTs into structures that can be used in the real world is extremely difficult. It’s akin to getting really excited about copper ore, but having no way to process that copper into useful wire.
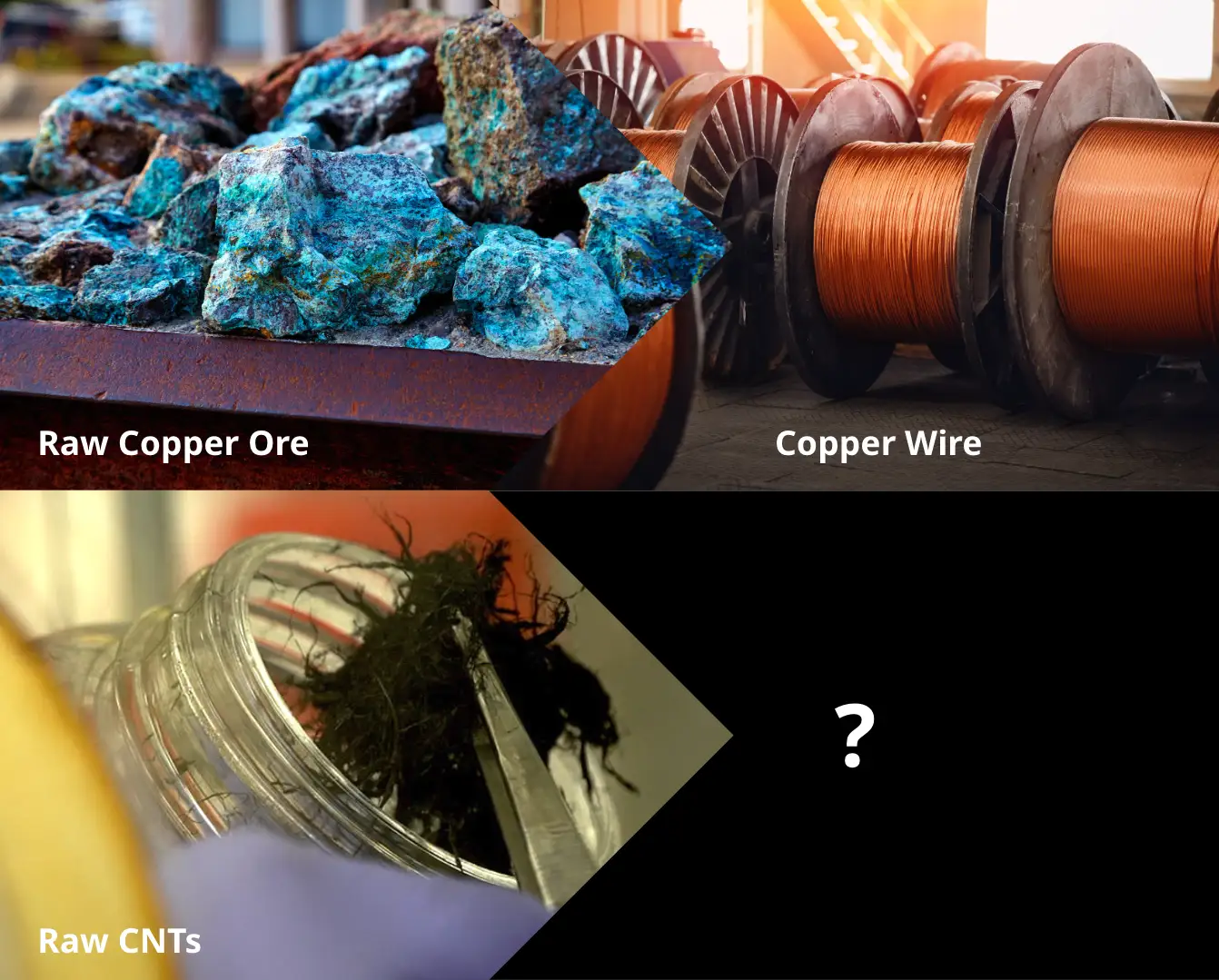
The hype of the early 2000s was about these fantastical properties at the nanoscale. But disillusionment followed when it became clear that forming CNTs into macroscale, useful structures is actually quite difficult.
Companies have resorted to mixing CNTs into dispersions. However, CNTs remain disorganized in these dispersions so they only imbue the materials with a tiny fraction of their molecular properties.
Companies have resorted to mixing CNTs into dispersions (cement, polymers, resin for composites, metals, etc.) to at least get some of the benefits of the amazing properties. However, CNTs remain disorganized in these dispersions so they only imbue the materials with a tiny fraction of their molecular properties.
Consider electrical conductivity. CNTs’ intrinsic conductivity (~ 100 MS/m) can transform insulating matrices into conductive materials. A polymer like polystyrene, with conductivity <10-20 MS/m, can reach 0.000001-0.00001 MS/m with 1-2 wt% CNTs added to it. But that 0.00001 MS/m is 10,000,000 times less conductive than the CNTs’ potential.
The same is true for tensile strength. CNTs have a molecular tensile strength of ~100 GPa, so even small additions (0.1-5 wt%) via mixing can enhance the strength of the matrix. For example, polymer-CNT composites (e.g., CNT-polyethylene) can see strength increases of 20-50%, reaching 50-100 MPa, compared to 20-40 MPa for the neat polymer. But 100 MPa is 1,000x weaker than the CNTs’ potential.
Despite these drawbacks, demand for even these marginal improvements in materials performance is exploding. A recent report from the Advanced Carbon Council found that the CNT market is growing rapidly at a compound annual growth rate (CAGR) of 17% from 2024 to 2034. The market size is expected to reach multiple billions of dollars by the end of this period. The growing adoption of CNTs in lithium-ion batteries for electric vehicles, supercapacitors for renewable energy storage, and flexible electronics are cited as the major contributors to this growth.
Carbon Nanotube *Fibers* (CNTF)
Truly unlocking the potential of CNTs requires a different approach from dispersion. Instead, transform them into fibers. These solid carbon flexible fibers can be subsequently constructed into things—useful things. They are macroscale materials made from CNTs, which can then be assembled into larger, practical forms, such as wire/yarn, textiles, and structural composites. Kevlar and Dyneema are excellent demonstrations of the versatility of fibers.
Processing CNTs into fibers aligns and packs the CNTs, achieving properties that are orders of magnitude better than what you can achieve with CNTs mixed with other materials. For example, see below:
Mixed CNT Composites | CNT Fiber | |
Conductivity (MS/m) | 0.000001-0.00001 | 10 |
Strength (GPa) | 0.05-0.1 | 1-10 |
Ultimately, transforming CNTs into fibers (valuable carbon!) requires a suite of intellectual property (IP). Doing so scalably with exceptional properties, and from multiple CNT feedstock sources, is an IP moat that can only be realized when your origin story begins with Nobel laureates and continues with some of the best minds in the industry.
The Wet-Spinning Breakthrough
It was Nobel laureate Richard Smalley, PhD, who had the idea to use wet-spinning technology to align the carbon nanotubes into fibers and maintain the properties. Wet spinning fibers is a well-established technology, producing viscose fibers at 100 kt plant scale. If you don’t know what viscose fibers are, you’ve almost surely worn them: tencel, lyocell, micro-modal, modal, rayon, and bamboo rayon are all viscose.
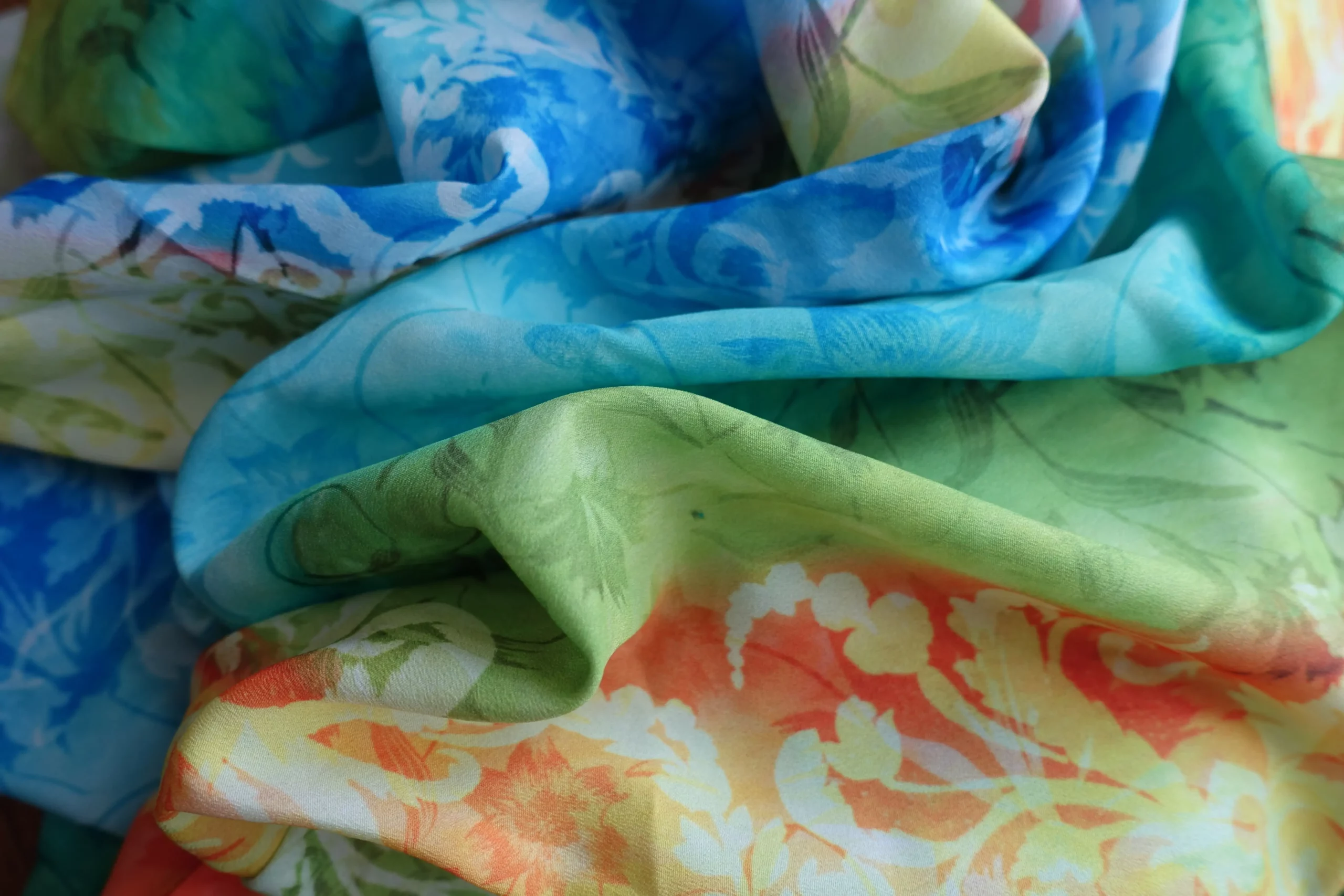
In 2001 at Rice University, Smalley began trying to use this liquid processing technology to spin carbon nanotubes into fibers that retained the tubes’ electrical and mechanical properties over kilometer lengths. DexMat Co-Founder and Chief Science Advisor, Matteo Pasquali, PhD, was part of the project from the beginning and took over after Smalley’s passing in 2005.
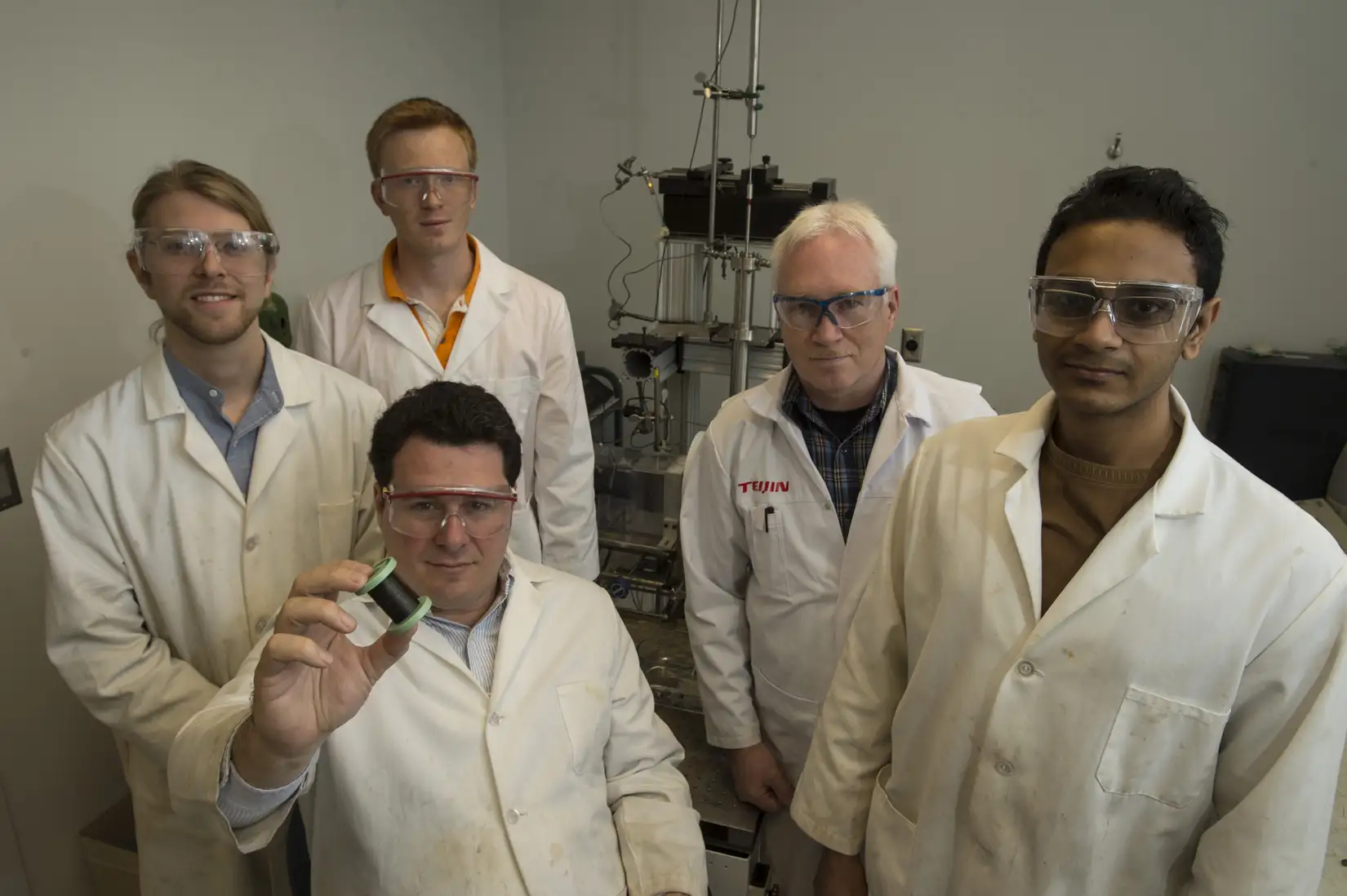
By 2013, the team achieved the first demonstration of high conductivity and strength in carbon nanotube fibers. Professor Pasquali led the team, which then included Dmitri Tsentalovich, PhD, now DexMat Co-Founder and CTO, as well as Colin Young, PhD, now DexMat Senior Research Scientist.
In 2016, also out of the Pasquali Lab, Dmitri Tsentalovich, PhD, wrote the seminal paper that defined the relationship between carbon nanotube characteristics and the fibers and properties that can be formed from them.
Carbon nanotube fibers allow us to harness extraordinary properties in a form that’s usable in real-world products, amplifying their impact across industries.
Finally, the gap between the extraordinary nanoscale properties of individual CNTs and practical, macroscale applications had been bridged. Spinning them into fibers allows us to harness these attributes in a form that’s usable in real-world products, amplifying their impact across industries.
Spinning fibers also enable the “macroscale” structures to be made of pure carbon, maintaining a key advantage with CNTs: recycling. The advanced materials community has long been challenged by the issue of carbon fiber recycling. Current carbon fibers can only be downcycled at their end of life by breaking them into smaller pieces, rendering them unsuitable for reuse in high-performance, lightweight composites. However, CNTs (the emerging second-generation carbon fibers), offer a more sustainable solution. The study found that carbon fibers made out of carbon nanotubes can be fully recycled from mixed streams (i.e., in realistic conditions for end-of-life recycling).
The Galvorn Advantage
At DexMat, we make carbon nanotube fibers, called Galvorn. Our proprietary processes allow us to make fibers with superior properties, and do so at scale—eventually making them at a hundred-kiloton scale. Critically, our trade secrets and IP give us a significant performance, scalability, and economic advantage.
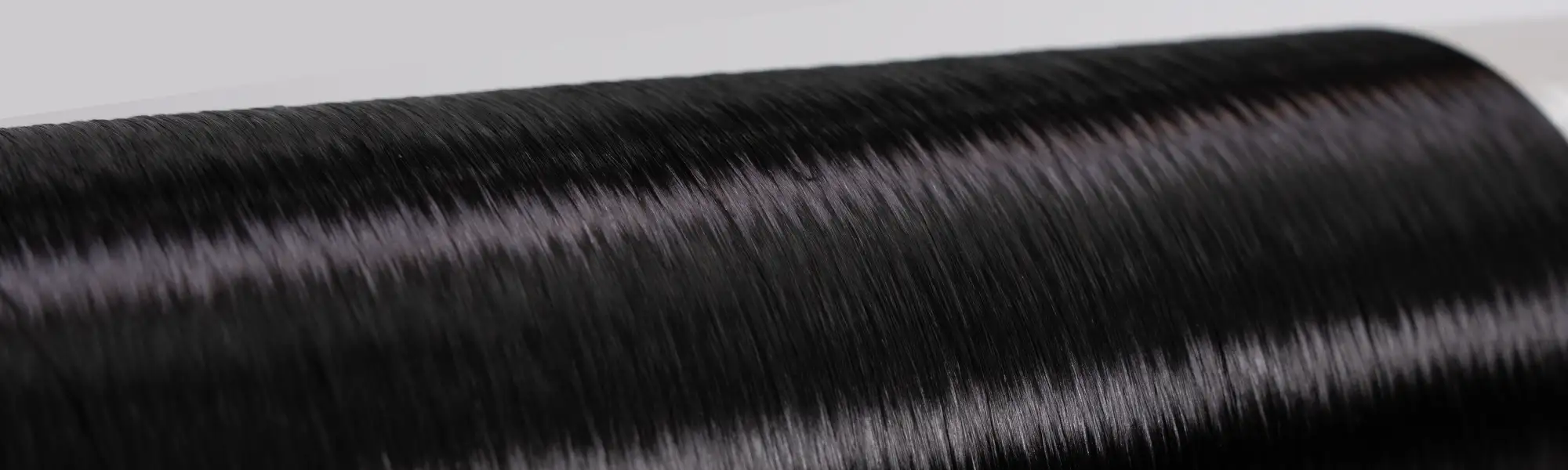
The performance advantage is clear: this study investigates the relationship between the physical properties of six CNT yarns and their structures. (Yarns are fibers that have been twisted or braided together.) The TL;DR? Galvorn is 4 to 152 times more conductive and 1.3 to 23 times stronger than other carbon nanotube yarns (aka “wires”) on the market.
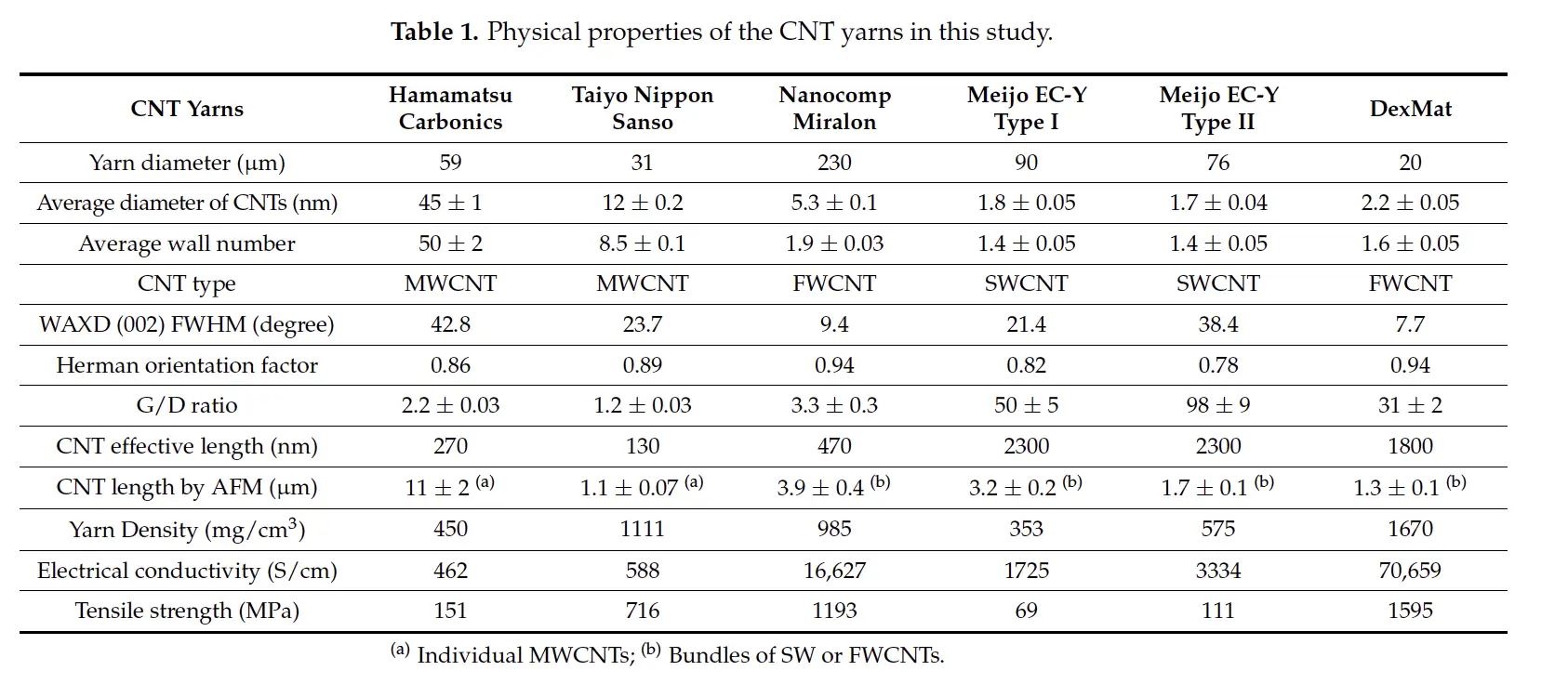
As for scale, we today regularly produce multiple kilometer lengths of Galvorn for our customers. In fact, we recently hit a new milestone, producing the longest length of fiber in a single day: 130 kilometers! To be clear this is just the beginning.
Since Galvorn’s invention, we have scaled up production capacity more than 3,000x, while bringing costs down 99.6%. The scalability of our patented process unlocks a tremendous economic advantage. While other materials innovations have required hundreds of millions just to stand up their first small facility, we can get to comparable tonnage for a fraction of that spend. For example, a “green” steel startup has raised $200M, and just announced that they produced a tonne of steel in the first quarter of this year. With orders of magnitude less capital, we are already near that production capacity—and we have a much greater "equivalent production capacity," given how much stronger Galvorn is than steel.
Perhaps the most fundamental way to evaluate economics is to look at the energy intensity of materials production. Galvorn production today—at a relatively small scale—already requires less energy than carbon fiber and aluminum. At scale, it will demand less energy than steel and copper—and by extension reach commodity-scale production costs, while still delivering ultra high-performance properties.
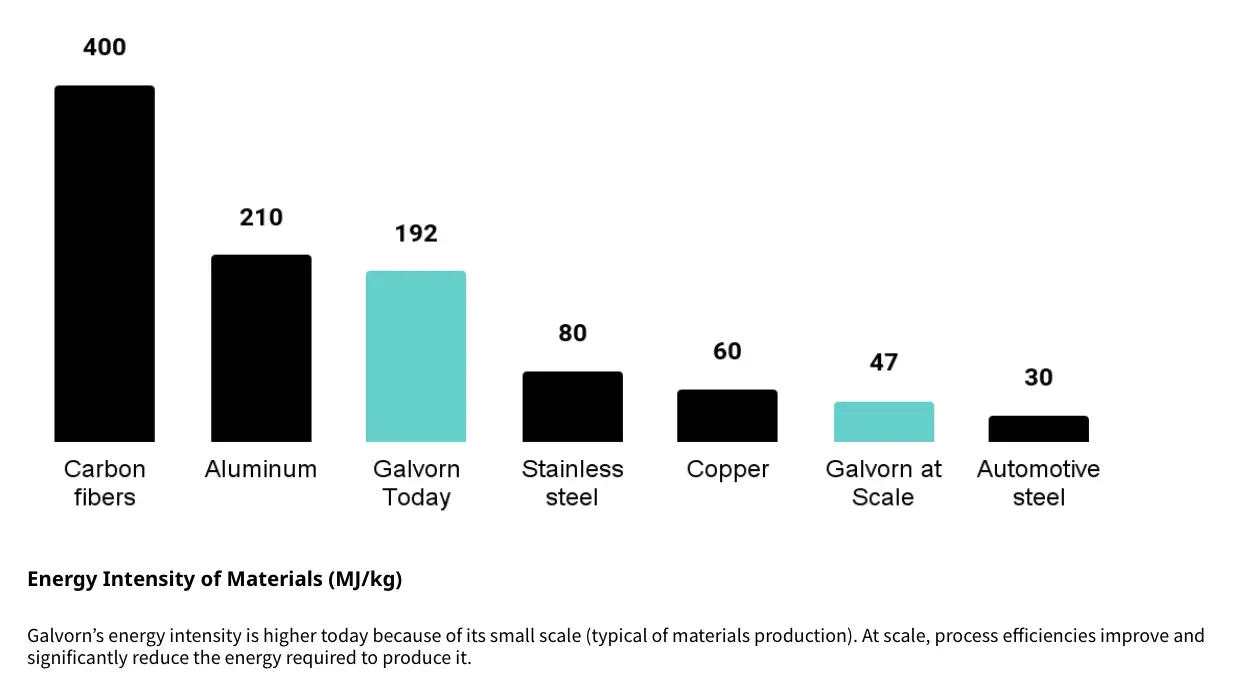
Why CNT fibers are a game changer
While it took the vision of a Nobel-winning scientist to imagine that macroscale structures with exceptional properties could be achieved through fiber wet-spinning CNTs, the significance of this accomplishment is something we can all appreciate. Carbon nanotube fibers change the game across numerous dimensions. They are better performing than incumbent metals, they can be produced at scale with consistent properties, their CapEx requirements are significantly lower than metals, and so too are the energy costs.
These advantages are not just transformational, they are practical. We live in a world increasingly in need of conductivity, and perpetually demanding stronger, lighter materials. It’s time to recognize that carbon nanomaterials are not science-fiction or magic, they are increasingly the practical solution to the modern built environment.
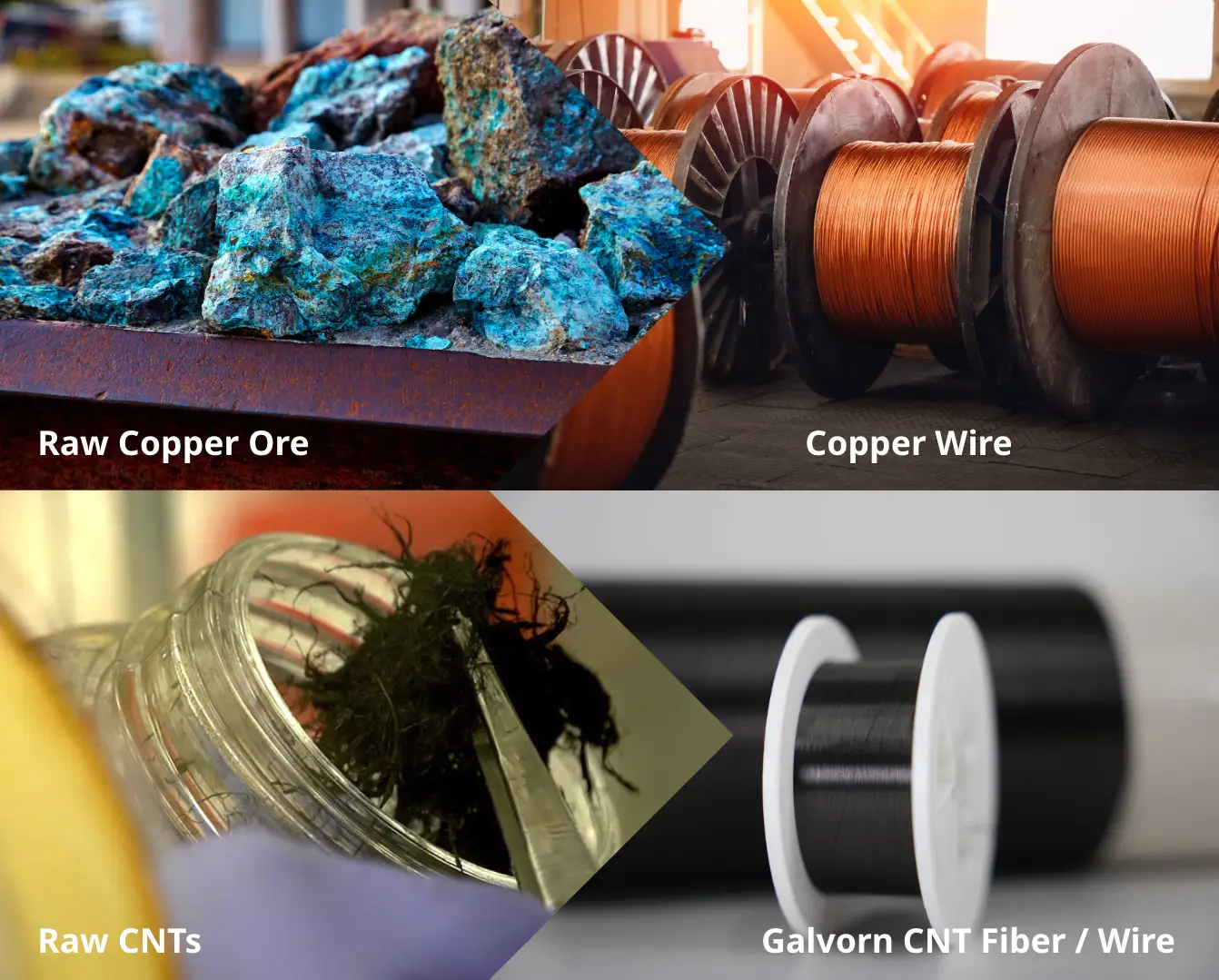