Carbon Nanotube Fiber
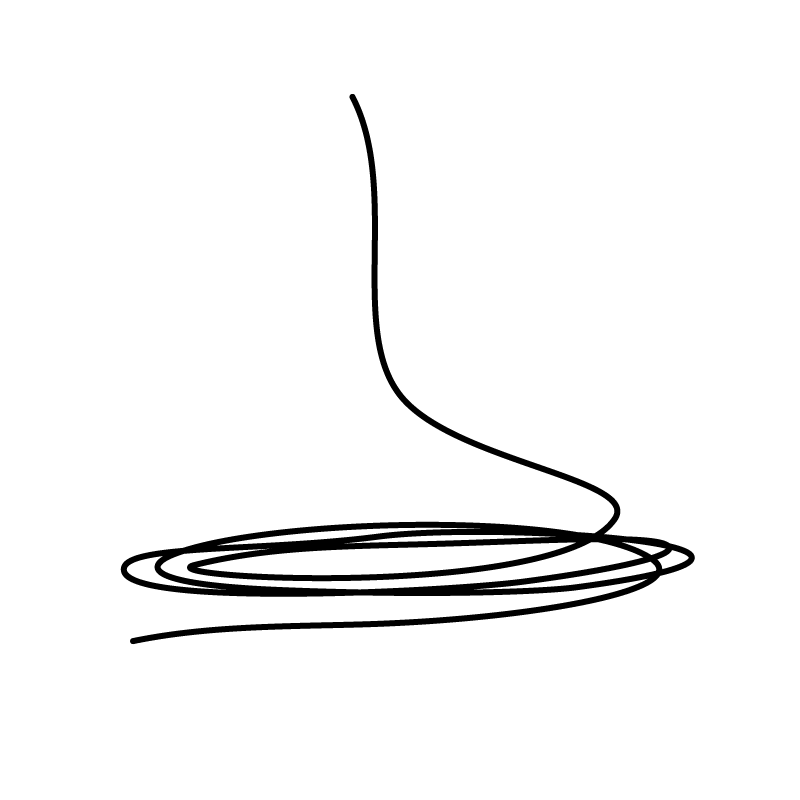
INTRODUCTION
Revolutionizing Wire and Cable Applications
Carbon nanotube (CNT) fibers are transforming industries by offering lightweight, high-strength, and highly conductive alternatives to traditional materials like copper and aluminum. At DexMat, our special Galvorn CNT fiber is at the forefront. It offers unmatched performance for wires and cables in aerospace, defense, automotive, and data centers.
This guide looks at the history, properties, production methods, and uses of CNT fiber technology. It makes the case for why Galvorn is the future of advanced conductors.
Or, watch the webinar: The Future of Conductive Materials is Here
History of Carbon Nanotube Fibers
Carbon nanotubes, discovered in 1991 by Sumio Iijima, marked a breakthrough in nanotechnology. These cylindrical graphene structures, with diameters as small as 1 nanometer, exhibited extraordinary strength and conductivity. Early research focused on individual CNTs, but by the early 2000s, scientists began exploring ways to assemble them into macroscopic fibers to harness their properties for practical applications.
Key Milestones
- 1991: Sumio Iijima’s discovery of multi-walled CNTs in arc-discharge soot (published in Nature) sparked global interest.
- 1998: Single-walled CNTs were synthesized, offering even higher theoretical strength and conductivity.
- 2000s: Researchers developed methods to spin CNT fibers, with early successes in wet spinning and dry spinning from CNT forests.
- 2010s: Advances in CNT alignment and purity enabled fibers with tensile strengths rivaling steel and conductivities approaching copper.
- 2023: Following its 2023 raise DexMat demonstrates 20x scale up and 96% cost decrease.
Richard Smalley’s Pioneering Role in Wet-Spun Carbon Nanotube Fibers
Learn more about DexMat's origins and the pioneering role that nobel laureate, Richard Smalley, had in actualizing wet-spun carbon nanotube fibers.
The evolution of CNT fibers reflects decades of innovation, driven by collaborations between academia, industry, and government agencies like NASA and the U.S. Department of Defense. Today, Galvorn represents the culmination of these efforts, offering a scalable, high-performance solution for next-generation wiring.
Technical Properties of CNT Fibers
CNT fibers combine exceptional mechanical, electrical, and thermal properties, making them ideal for demanding applications. It’s important to note that “macroscale” CNT fibers are a downstream product of raw “nanoscale” CNTs.
Individual CNT molecules exhibit exceptional properties:
- Tensile strength: > 110 GPa (Steel 5.2 GPa, Carbon Fiber 6.4 GPa )
- Electrical conductivity: ~ 100 MS/m (Cu 59 MS/m, Ag 63 MS/m)
- Thermal conductivity: ~ 3000 W/m-K (Diamond 2000 W/m-K)
- Low density: ~ 1.4 kg/m3 (Steel 8 kg/m3, Aluminum 2.7 kg/m3)
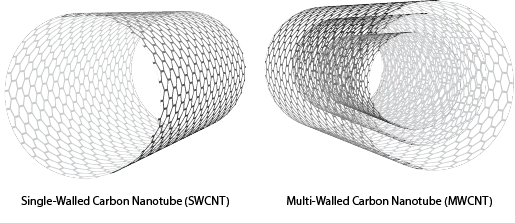
However, the properties drop dramatically when formed into macroscale structures, especially when dispersed or mixed into composites. Carbon nanotube fibers achieve the highest properties at the macroscale. Learn more about the key distinction between CNTs and CNTFs: A Misconception that Obscures the Real Progress of Solid Carbon
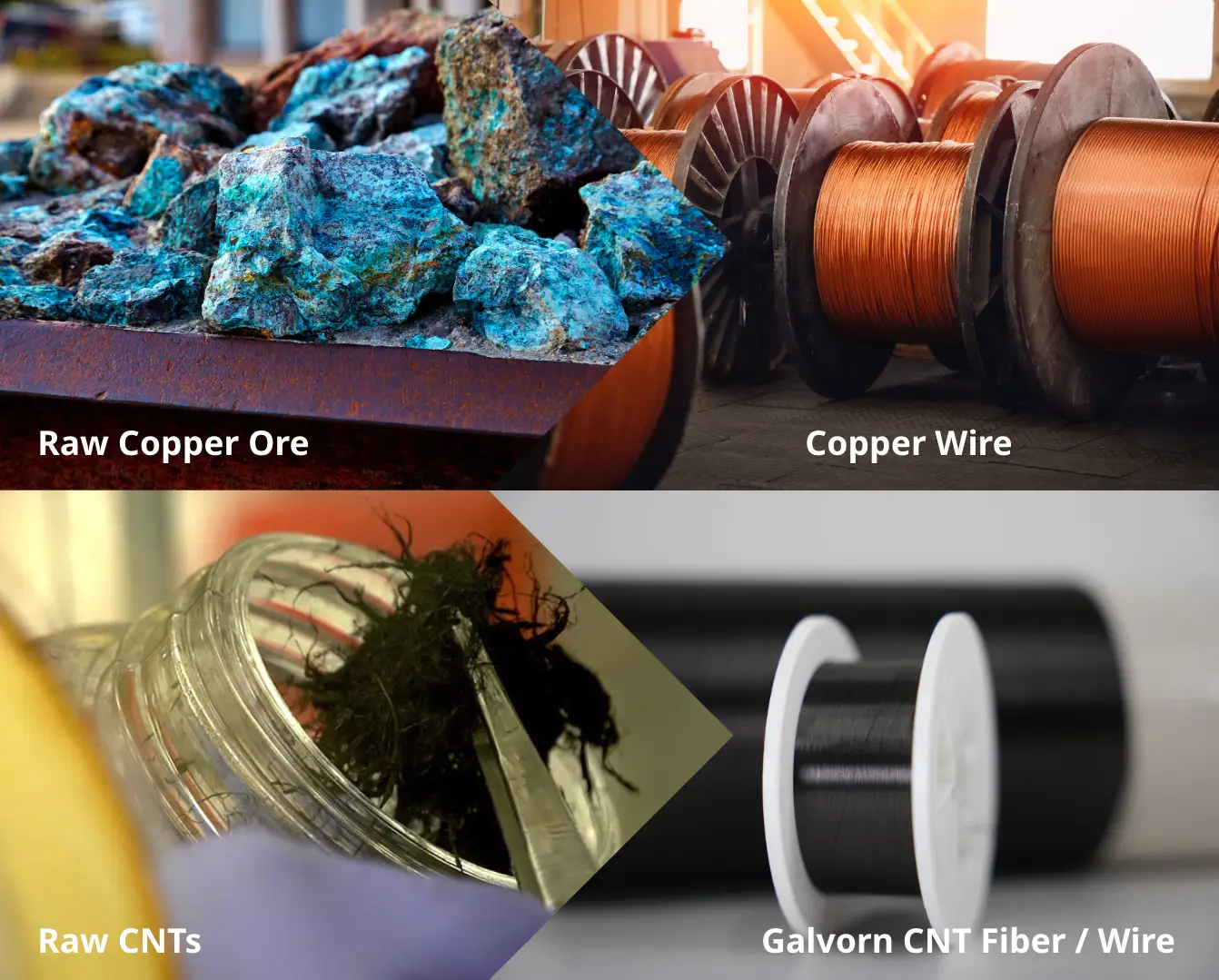
CNT vs. CNTF: Understand the Key Differences
The differences between carbon nanotubes (CNTs) and carbon nanotube fibers (CNTF) are game-changing.
Below, we break down the key characteristics of CNT fibers, with specific insights into DexMat’s Galvorn.
1. Mechanical Properties
- Tensile Strength: Galvorn single filament fibers have a tensile strength of 3 GPa and a tenacity of 2 N/tex, making it many times stronger than high-grade steel and 50x stronger than copper, weight for weight.
- Flexibility: CNT fibers resist fatigue, with Galvorn enduring millions of flex cycles, making it exceptionally durable and suitable for high-demand aerospace and defense applications.
- Lightweight: Galvorn carbon nanotube fiber is exceptionally light, with a density of 1.6 g/cm³, making it 80% less dense than copper (9.0 g/cm³) and approximately half the density of aluminum (2.7 g/cm³).
2. Electrical Performance
- High Conductivity: CNT fibers approach metallic conductivity, with Galvorn achieving up to 10 MS/m, comparable to copper (58 MS/m) at a fraction of the weight. In fact, on a per mass basis Galvorn's electrical conductivity is nearly equivalent to copper (6150 Sm²/kg for Galvorn vs. 6300 Sm²/kg for copper). Learn more about lightweight signal wire and cable with Galvorn.
- EMI Shielding: CNT fibers provide superior electromagnetic interference (EMI) shielding, critical for defense and aerospace electronics. Learn more about lightweight EMI shielding with Galvorn.
- High-Frequency Performance: Research has shown that carbon nanotube fibers perform better than copper at high frequencies. Thus, Galvorn carbon nanotube fibers could perform as well or better than copper for transfer of data using high frequency AC signals over longer distances. Learn more about the findings, which focused on CNT fiber use in antenna applications.
3. Thermal Properties
- Thermal Conductivity: Galvorn CNT fiber has a thermal conductivity of 450 W/m-K, exceeding copper's 385 W/m-K. This superior heat dissipation capability is vital for high-performance electronics and power cables, allowing for greater current carrying capacity per unit mass.
- Temperature Resistance: Galvorn withstands temperatures from -100°C to 500°C, outperforming traditional conductors in extreme environments.
- Flame Resistance: Unlike polymers, CNT fibers resist burning, enhancing safety in aerospace and defense.
4. Chemical Stability
- Corrosion Resistance: CNTs are inert to most chemicals, making Galvorn ideal for harsh environments like marine or space applications.
- Functionalization Potential: CNT surfaces can be modified for specific needs, such as enhanced adhesion in composites.
These properties position CNT fibers as a game-changer, offering a unique combination of strength, conductivity, and durability that traditional materials cannot match.
Not all carbon nanotube materials are created equal. This study investigates the relationship between the physical properties of six CNT yarns and their structures. The TL;DR? Galvorn is 4 to 152 times more conductive and 1.3 to 23 times stronger than other carbon nanotube yarns (aka “wires”) on the market.
Methods of Producing CNT Fibers
Producing CNT fibers requires advanced techniques to align and assemble nanoscale tubes into macroscopic structures. Below we outline the most common approaches to producing carbon nanotube fibers.
Notably, DexMat’s proprietary process has been optimized for performance and scalability, which allows us to deliver not only the highest performing commercially available fibers, but do so at price points that make it feasible for applications with broad market adoption. The use of carbon nanotube fibers is no longer constrained to niche applications!
Wet Spinning
- Process: CNTs are dispersed in a liquid, extruded through a spinneret, and coagulated into fibers.
- Advantages: Produces continuous fibers with good alignment, suitable for cables. Solution spinning process is highly scalable.
- Challenges: Acid-based processes require careful handling.
- DexMat’s Innovation: Highly scalable and low carbon footprint spinning technology creates best-in-class CNT fiber properties. Learn more about how Galvorn is made.
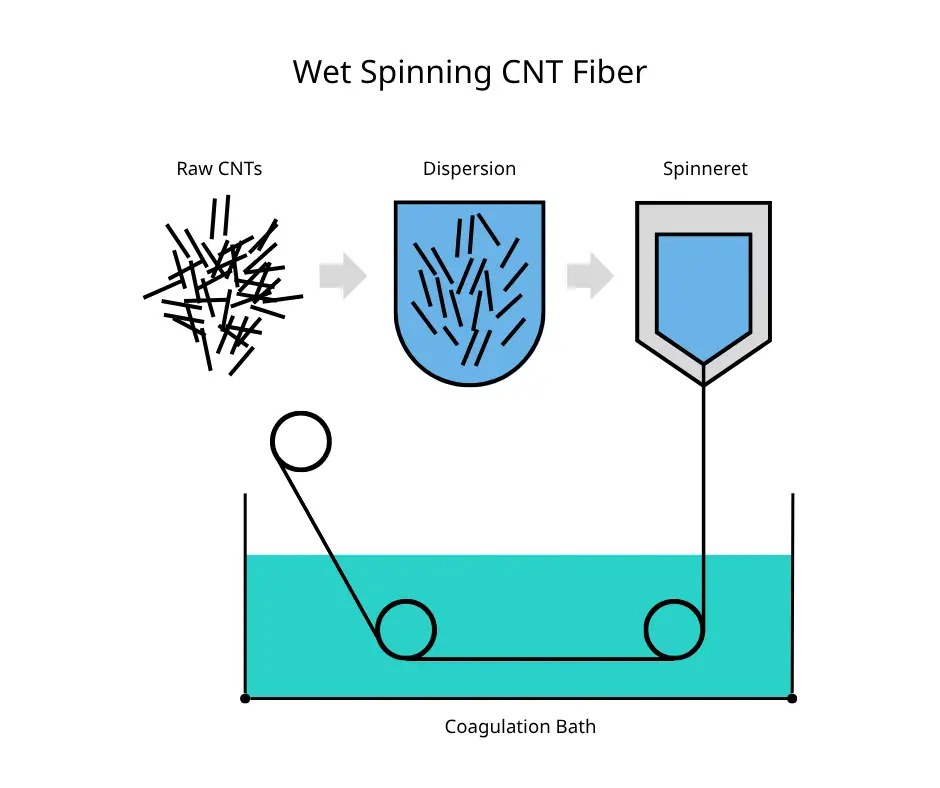
Dry Spinning from CNT Forests
- Process: CNTs are grown as vertically aligned “forests” on a substrate, then drawn into fibers or yarns.
- Advantages: High aspect ratio nanotubes enhance strength.
- Challenges: Limited by forest size and growth uniformity. Ultimately not scalable for manufacturing fibers.
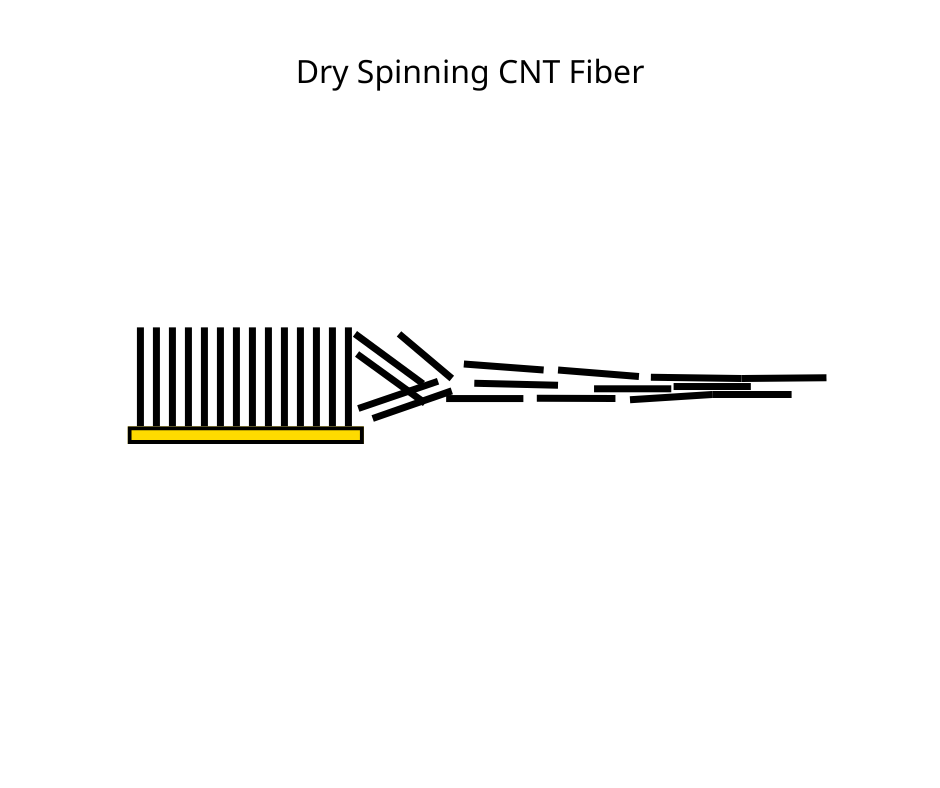
Direct Spinning from CVD Reactor
- Process: CNTs are spun directly from a CVD reactor as they form, creating continuous fibers.
- Advantages: High aspect ratio nanotubes enhance strength.
- Challenges: Prevents optimization of CNT production for high quality CNTs, as the reactor must be operated to produce a drawable aerogel. Requires precise control of CNT growth. Electrical conductivity is low. One fiber per reactor limits scalability.
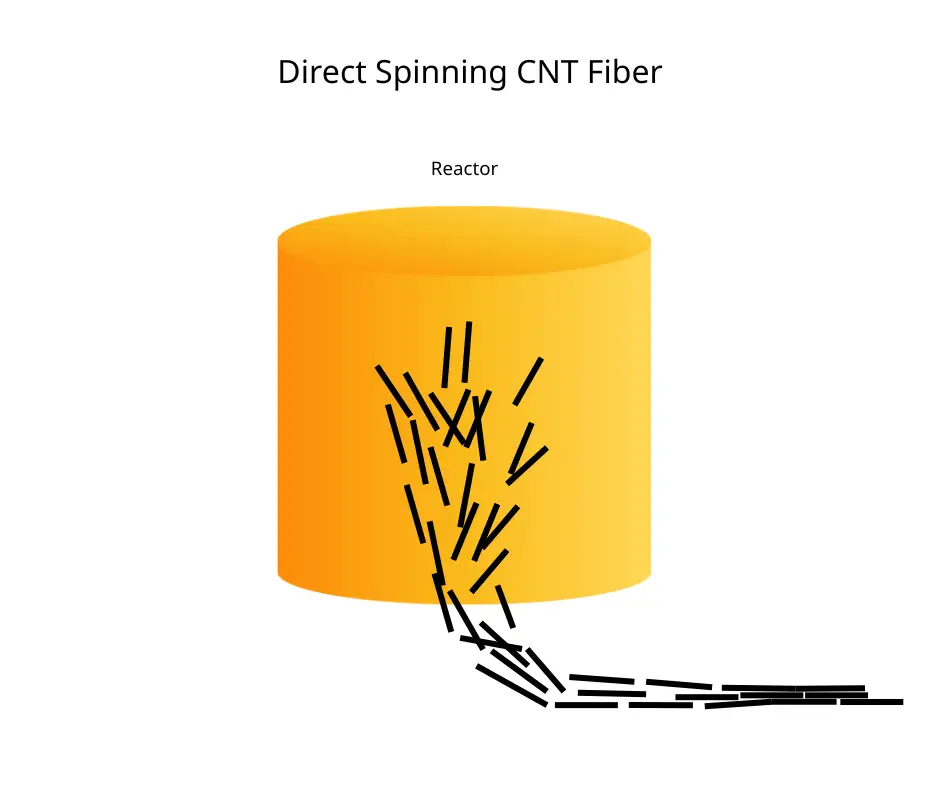
Scaling Challenges and Solutions
- Cost: Early CNT fibers were prohibitively expensive, however, DexMat’s innovations have reduced costs, making Galvorn competitive with specialty conductors.
- Purity: Impurities degrade performance. DexMat employs rigorous quality control to ensure high-purity CNTs.
- Scalability: As noted above, not all approaches to producing CNT fibers are scalable. DexMat’s proprietary processes, developed with Rice University, enable large-scale production that can meet the commercial demands of broad aerospace, defense, data center, and automotive applications.
These methods highlight the complexity of CNT fiber production, but DexMat’s advancements make Galvorn a practical, scalable solution.
Industry Applications of CNT Fibers
CNT fibers, particularly Galvorn, are revolutionizing wire and cable applications across multiple industries. Below, we explore how CNT fibers address specific challenges in aerospace, defense, automotive, and data centers.
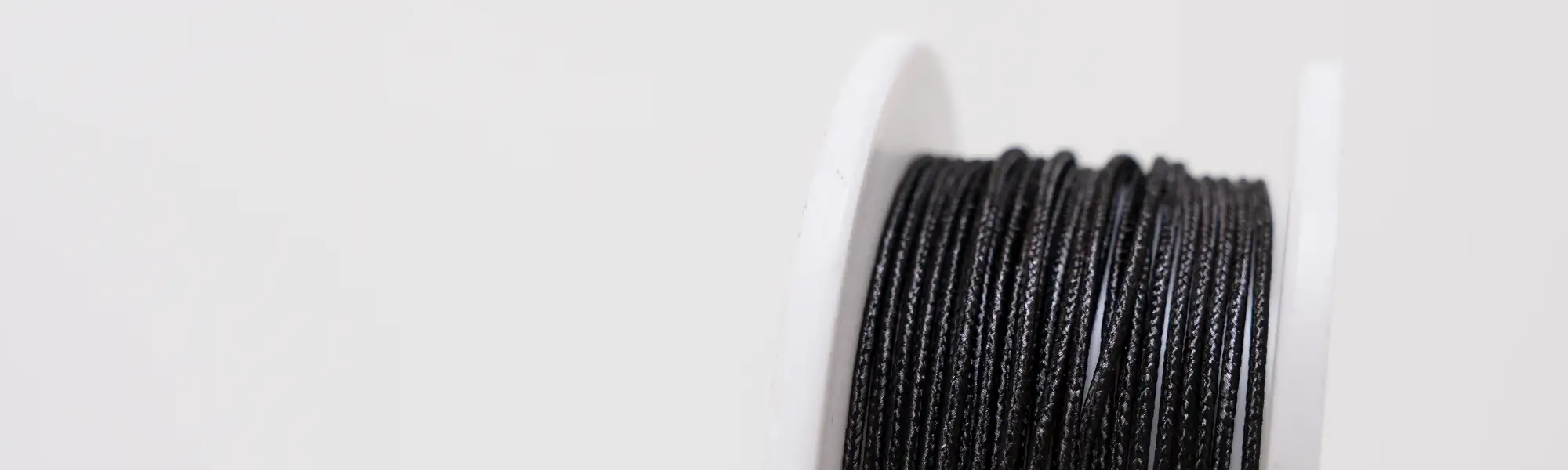
1. Aerospace
Carbon nanotube fibers, formed into carbon nanotube wiring, can be a superior alternative to traditional copper and aluminum conductors in the aerospace industry. In this blog post, The Future of Aerospace Cables, we discuss key applications for carbon nanotube wiring in aerospace, such as lightweight signal wire and cables, EMI shielding, and antennas.
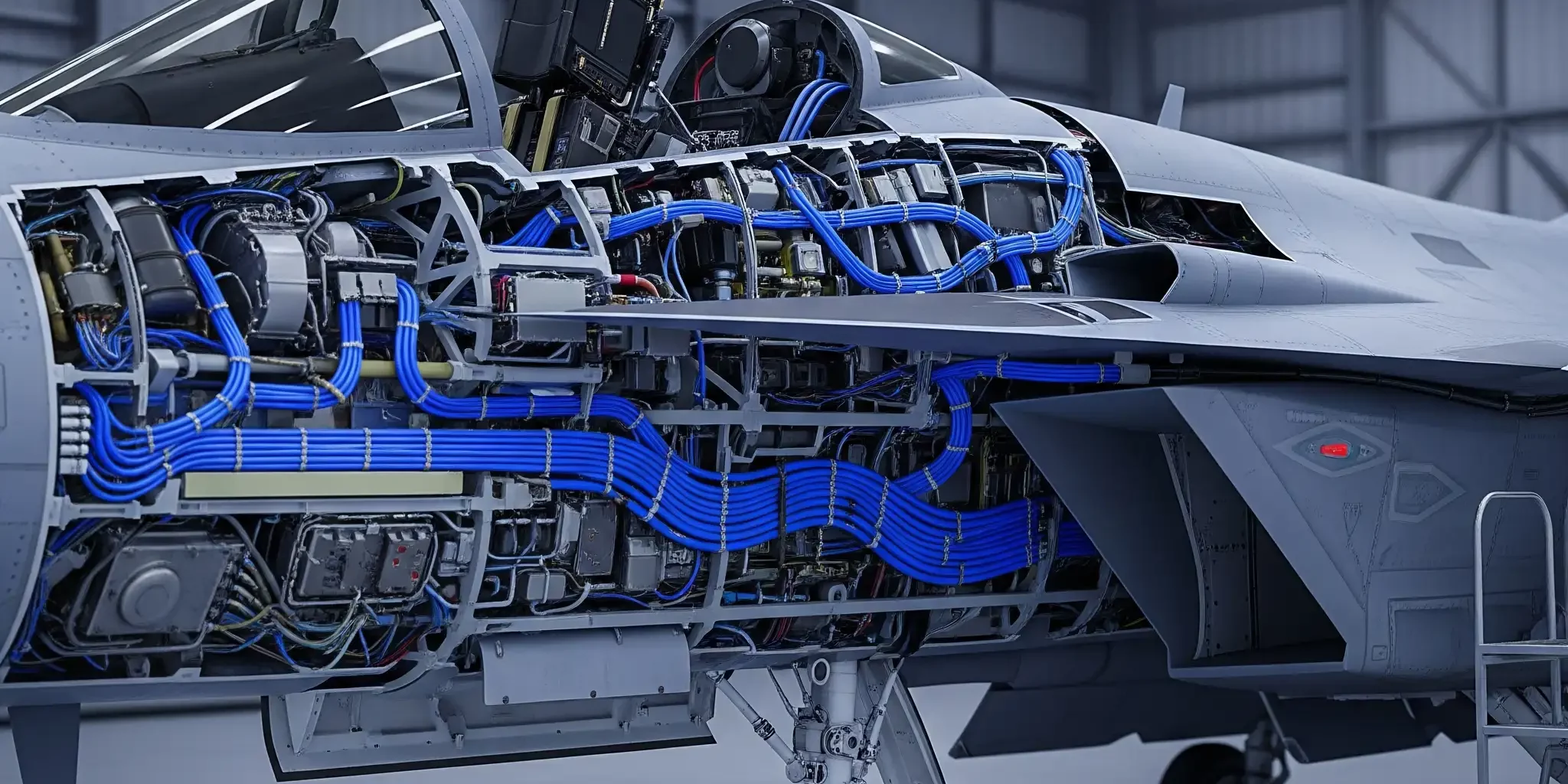
The Future of Aerospace Cables
Copper and aluminum have long been the standard for aerospace cables, but their limitations are pushing engineers to seek alternatives.
2. Defense
The defense industry has a long history of exploring and developing CNT-based applications. This paper, “Properties and Defence Applications of Carbon Nanotubes” in the Journal of Physics, provides a comprehensive study of the diverse array of defense applications where carbon nanotubes demonstrate performance improvements. There is no shortage of applications where carbon nanotubes can significantly increase performance.
However, as we discuss in this blog post, discussing the key differences between CNTs and CNT fibers, one of the key challenges has been producing macrostructures with CNTs that not only exhibit high-performance properties, but doing so in a scalable and efficient manner.
In many applications mentioned in the Journal of Physics study, raw CNTs are added to composites, polymers, or metals. Dispersion methods are complex. It is hard to evenly spread the CNTs. Also, the property improvements are only a small part of what carbon nanotube fibers can do.
A perfect example of a defense application that benefited from the high-performance properties of CNT-based products AND the manufacturing scalability that CNT fibers offer is the Air Force Research Laboratory’s (AFRL) development of field emission cathodes with Galvorn. Current state-of-the-art flocked carbon fiber cathodes require a complex process to essentially get very tiny carbon fibers to stand vertically on a substrate.
By contrast, Galvorn carbon nanotube fibers and yarns behave like textiles. They are simply knitted into the correct size and shape for the device. Galvorn carbon nanotube fibers enable scalable manufacturing processes, as well as deliver better performance.
As the defense, and other industries, take advantage of the performance benefits of carbon nanotube fibers, they can also rest assured that their investments support scalable and efficient manufacturing.
3. Automotive
The most widespread use of carbon nanotubes (CNTs) today is in lithium-ion batteries, particularly as conductive additives in electrodes for electric vehicle (EV) batteries and energy storage systems. CNTs enhance electrical conductivity, improve energy density, and boost charge-discharge performance, making them critical for high-performance batteries in EVs, consumer electronics, and renewable energy grids.
Major suppliers like LG Chem and Cabot Corporation produce CNTs for this purpose, with applications spanning automotive giants like Honda and others in the EV sector. This dominance is driven by the global push for electrification and sustainable energy, with CNTs valued for their ability to reduce electrode resistance and enhance battery efficiency.
Other applications commercially on the market include:
- Fuel Systems: CNTs provide antistatic properties in fuel lines and components, reducing rupture risks and enabling conductive plastics for electrostatic painting.
- Composites and Structural Parts: CNT-reinforced composites are used in bumpers, fenders, and structural reinforcements to improve strength, stiffness, and crashworthiness while reducing weight.
- Coatings and EMI Shielding: CNTs enhance conductivity in coatings for exterior parts and provide EMI shielding for electrical systems.
As with other industries, however, the difficulty of working with raw, disordered CNTs and challenges with scalability—a must-have for the automotive industry—have limited truly widespread adoption.
With the advent of carbon nanotube fibers, however, we are at an inflection point. Carbon nanotube fibers, constructed into wire / yarn and fabrics behave like a textile. They can be embroidered, knitted, or woven for advanced textile applications; fabrics and weaves made of carbon nanotube fibers or yarns are much more easily composited (no dispersion complexity!).
The automotive application with the greatest drop-in advantage, however, is lightweighting wire and cable. Galvorn CNT wire can replace copper conductors in signal wire, while Galvorn CNT film provides extremely lightweight EMI shielding—demonstrating up to 30-60% overall weight savings for cables, while meeting Mil Specs.
Lightweighting has long been a focus for the automotive industry: it increases fuel efficiency in internal combustion and hybrid vehicles, and extends EV range. With carbon nanotube fibers, which can be produced in multi-kilometer lengths, the industry can finally realize the promise of CNTs.
4. Data Centers
The use of carbon nanotubes (CNTs) in data center applications is an emerging field. Specific applications in data centers are less widespread compared to other industries like automotive, aerospace, or electronics, and the adoption is often at an exploratory or research stage.
Histoically, the primary focus of CNT use in data centers revolves around memory (ex. Nantero’s NRAM), transistors (ex. SkyWater), and potential thermal management solutions (ex. Carbice.)
Today carbon nanotube fibers can be twisted or braided into wiring, offering a superior alternative to traditional copper wiring. Below are some of the advantages of CNT fibers in data center applications, including:
- Lightweight Power Distribution and Interconnects: CNT fibers significantly reduce cable weight and optimize space within server racks, especially for low-to-medium-current applications.
- Improved Thermal Management: Their high thermal conductivity helps dissipate heat efficiently from components, potentially lowering cooling costs.
- Flexible and Durable Cabling: CNT fibers offer superior flexibility and strength, making them ideal for dense configurations and reducing wear from frequent reconfigurations.
- Support for Emerging High-Frequency Applications: CNT fibers are suitable for high-frequency interconnects and antennas in next-generation networks due to their signal performance and lightweight nature.
Across industries, CNT fibers change the game. Galvorn produces the highest performing carbon nanotube fibers using a process (fiber wet spinning) that has been proven at kiloton scale. By delivering performance at scale, we can finally realize the full promise of advanced carbon materials.
Why Choose Galvorn CNT Fibers?
DexMat’s Galvorn CNT fibers stand out due to their unique combination of performance, scalability, and sustainability.
- Performance: Galvorn approaches copper’s conductivity on a per mass basis, with superior strength and durability.
- Scalability: DexMat’s proprietary production methods enable industrial-scale supply, meeting demands from aerospace to automotive.
- Sustainability: Galvorn’s efficient manufacturing reduces the environmental impact compared to metal conductors.
- Innovation: Backed by partnerships with Rice University and funding from NASA, Galvorn represents cutting-edge CNT technology.
Our commitment to quality and innovation makes Galvorn the preferred choice for forward-thinking industries.
Conclusion
Carbon nanotube fiber technology is redefining wire and cable applications, offering lightweight, strong, and conductive solutions for aerospace, defense, automotive, and data centers. From their discovery in 1991 to DexMat’s scalable Galvorn fibers, CNTs have evolved into a practical, high-performance material. With exceptional mechanical, electrical, and thermal properties, advanced production methods, and transformative applications, CNT fibers are poised to replace traditional conductors. DexMat leads this revolution, delivering Galvorn as a sustainable, scalable solution for the future.