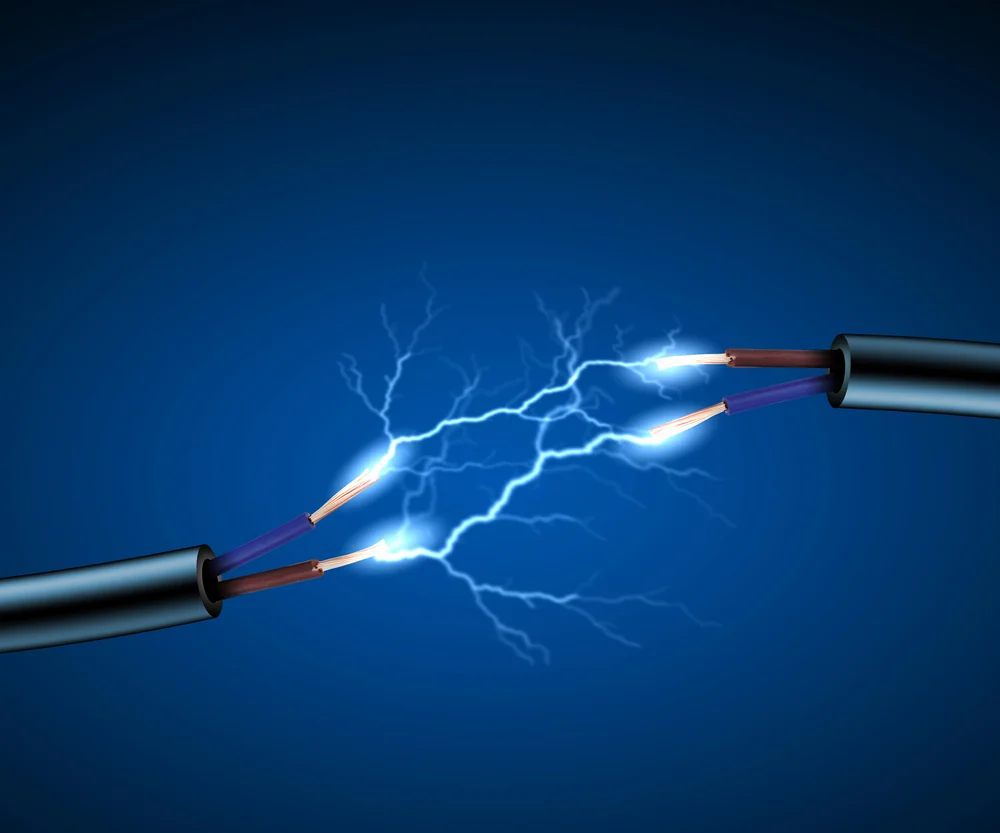
The effects of electromagnetic interactions in aerospace electrical systems are of growing concern due to the increasing susceptibility of system components to electromagnetic interference (EMI), use of automated electronic systems, and pollution of the electromagnetic environment (EME) with electromagnetic emissions. Currently, it is a major challenge to find ways of effectively shielding sensitive electronic equipment from electromagnetic interference without adding significant weight to aircraft or spacecraft. This makes the EMI shielding components of wires and cables a good area to target for improvement in order to reduce the weight of aerospace systems.
Copper wiring makes up as much as one-third of the weight of a 15-ton satellite. Half of this wire weight is typically in the EMI shielding; however, wiring and connectors are particularly vulnerable to electromagnetic interference, and it is important that weight reductions do not come at the expense of EMI shielding effectiveness. By substituting products that offer comparable shielding effectiveness, customers can achieve dramatic results in weight-savings with minimal insertion risk to the application.
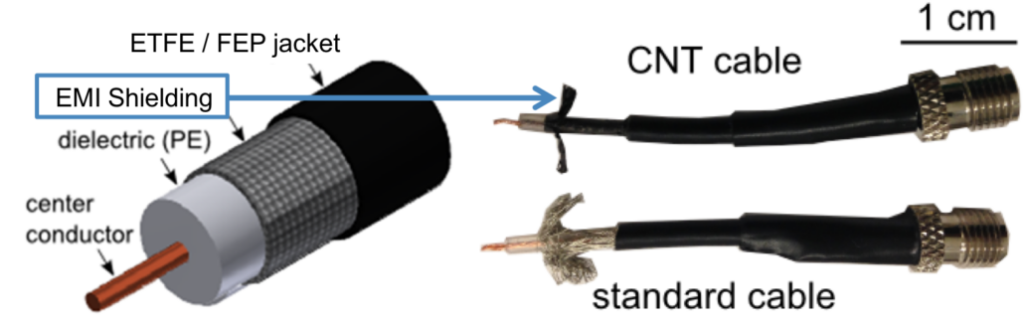
Carbon Nanotube Fibers and Films
Carbon nanotubes (CNTs) are advancing as the most promising solution for reducing the weight of spacecraft wires. CNTs combine high strength, electrical and thermal conductivity with low density, which makes them ideal for applications where weight reduction is a priority. Compared to a copper wire with the same diameter, a DexMat CNT fiber has 6 times higher strength, more than 6 times lower density, and at least 25 times higher flexure tolerance, all of which are essential qualities for conductors in aerospace applications. The image above shows a standard copper braid cable shield compared to a CNT shield for an RG-316 cable. CNT film / tape shields are 95% lighter than the copper double braid shields, while offering comparable shielding effectiveness and insertion loss properties. The CNT film shielded cables also have the following advantages:
- Overall cable weight reduction of CNT shielded vs. Cu double braid shielded cable without connectors is over 50%
- CNT film shield is 100 microns thick compared to 500 micron thick Cu double braid shield
- It is easy to apply CNT film to coaxial cables as well as twisted pair type cables
- CNT film shielded cables survive at least 1000 flex cycles with a minimum bend radius of at least 7.5X the jacketed cable diameter
Metalized Polymeric and Carbon Fibers
Metalized aramid fibers (Aracon) and metalized PBO fibers (Amberstrand) are strong, lightweight alternatives for cable shielding. These materials can be as much as 70% lighter than traditional copper braid shields. However, the relatively low conductivity of the metalized fibers results in less effective shielding performance at frequencies below 10 MHz. While this limits the range of shielding applications that these materials can be used for, metalized polymeric fibers are currently being used as shielding materials on board various aircraft. Metallized carbon fibers are another potentially competitive material. Nickel coated carbon fibers from Toho-Tenax Co., Ltd. and from Conductive Composites Co., LLC are significantly stronger than Aracon or Amberstrand fibers; however, the lower conductivity of the nickel-coated carbon fibers makes them unsuitable for cable shielding applications.
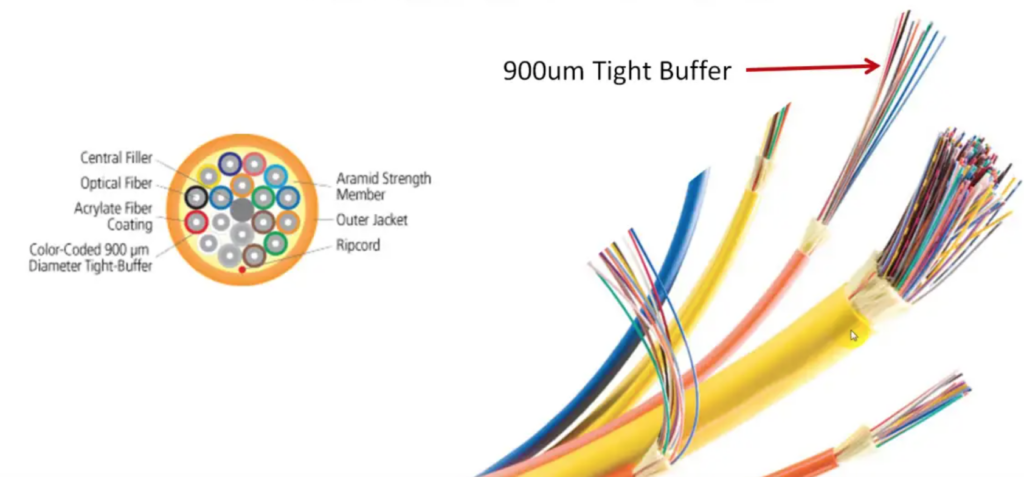
Fiber Optics
Fiber optic cables are another lightweight cable option that is already currently being used in aircraft. Because these cables convert information into light and transmit that data through glass fibers, they are not susceptible to EMI and do not need any EMI shielding. Therefore, fiber optics communications cables are typically as much as 50% lighter than copper braid shielded cables. Fiber optics communication systems are currently featured on F-35 fighter jets, but there have been maintenance issues with the use of fiber optics in aircraft as a result of the tight bends and limited space that cables need to be crammed into on aircraft. Fiber optics systems also require additional equipment to process data signals, which can add weight to aircraft.
Ultimately, there is room for multiple lightweight cable options in aerospace and next generation aircraft, and spacecraft will likely continue to use metalized polymer as well as fiber optics cables. While CNT shielded cables are not in commercial use in aerospace systems at this time, the superior weight reduction and durability of CNT shielding is likely to lead to the adoption of CNT materials for aerospace cable shielding in the near future.