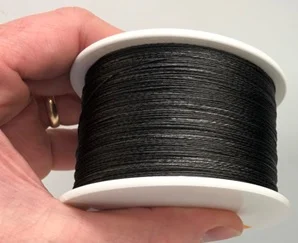
This article is the first of a two-part series about how carbon nanotube (CNT) fibers can be twisted or braided into finished yarns. In this article we will introduce the reasons for making CNT yarn products and discuss the construction, as well as the pros and cons, of twisted yarns. In the second article we will discuss the basic structure of our braided CNT yarns.
Fibers vs. Yarns
DexMat’s Galvorn CNT fiber products are available in three basic formats. The first format is that of an individual, solid fiber filament formed by our proprietary process, which transforms disordered CNTs into an aligned structure. These filaments range in size from 10 microns to around 100 microns in diameter, and the CNTs that compose them are densely packed and highly aligned along the fiber axis. The (relatively) high density and high degree of alignment achievable in this format allows it to achieve high values in many of the material properties we look for in CNT fibers, including tensile modulus, electrical conductivity, and thermal conductivity. However, there is a natural limit to the size that we can achieve in an individual fiber filament, particularly if we want to make compact fibers with a reasonably round cross-section. For this reason, it is difficult to fabricate individual fibers with diameters larger than 100 microns.
For applications that require larger diameters, either to bear more mechanical load or to achieve a lower total electrical or thermal resistance, it is necessary for us to combine individual fiber filaments into larger yarns. When making a yarn, we start not with individual CNT fibers but with a number of parallel fibers collected together in a bundle; several such bundles are then combined together to make the yarn. The total linear mass of the yarn will depend on the size of the individual fibers, the number of fibers in the bundle, and the number of bundles that are combined together into the final yarn; the yarn diameter will depend on the packing density of the chosen yarn structure in addition to the above factors. We offer Galvorn CNT yarns in two formats: plied and twisted yarns with diameters ranging from 130 microns to 500 microns, and braided yarns with diameters ranging from 600 microns to 1000 microns.
Combining individual fibers into larger yarns does introduce some drawbacks in terms of achievable material properties. Even if a yarn composed of many individual filaments is tightly wound, it will always have a density somewhat lower than the density of those filaments; for this reason, properties that are normalized by cross section, such as tensile strength and conductivity, will be lower in a yarn. On the other hand, the yarn structure imparts properties that the individual CNT fiber filaments do not possess on their own: an increase in abrasion resistance, an increase in stretchability, and a stable shape that is more resistant to deformation when bent or compacted. These properties, along with the flexibility and overall density of the yarn, depend to a great extent on the style of construction that is chosen.
Twisted Yarns
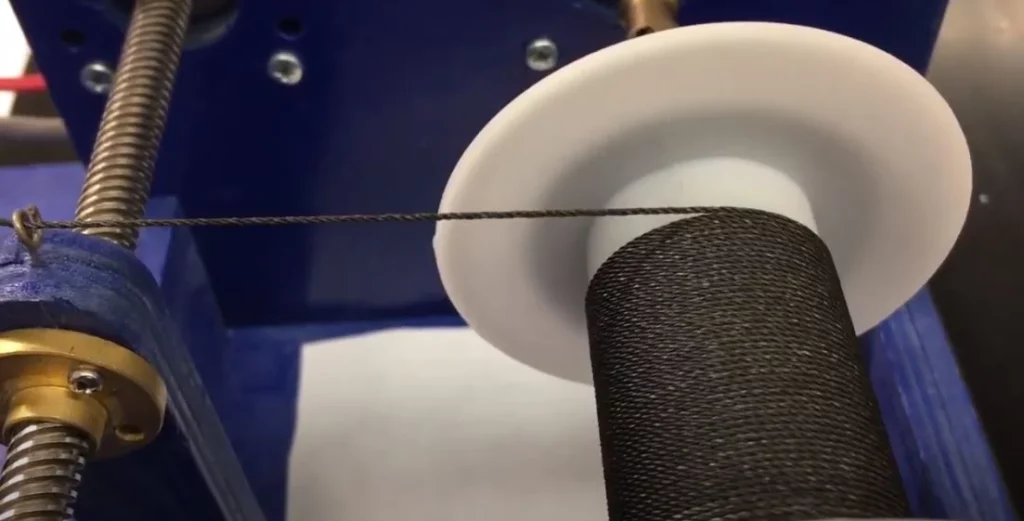
Twisting and plying filaments together into a larger structure is a technique that is used to create many yarns and ropes out of a wide variety of fiber materials with a wide variety of sizes. Regardless of the material, the fundamental construction of twisted yarns is the same: bundles of filaments are twisted around their own axes, and then 3 or more such bundles are twisted together into a larger combined cable. The initial twist imparted to the bundles themselves is crucial: the yarn holds together because the direction of twist within the bundles and the direction in which they are twisted around one another are opposed. The elastic energy that would normally induce the bundles to unravel from each other and the elastic energy that would cause each bundle to untwist create a system of forces that oppose and balance each other out. This type of yarn structure is said to be “locked”, and will not unravel spontaneously.
The direction of twist applied to create the final yarn determines the final chirality of the structure. These different chiralities are referred to as “S” or “Z” twists, based on their visual appearance; The image below shows how an “S” and “Z” twist can be identified. In some applications, depending on the types of torque or abrasion forces the yarn is expected to experience, one or the other of these chiralities might be preferred.
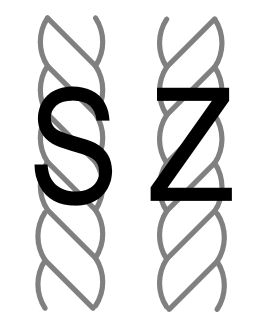
Yarn with a twisted structure has several benefits. When a proper degree of twist is applied it promotes a tight packing density between constituent filaments, particularly once the twist is “locked” into place by a balance of stored elastic energy. This close contact between fibers is beneficial for stress transfer, heat transfer, or (in the case of electrically conductive fibers) transfer of electric current. The twisted structure has additional benefits for the mechanical properties of the yarn: by the nature of the structure, any tensile force applied to the yarn will be partially applied to compress the filaments together even more tightly. Finally, for applications in which some degree of elongation or elastic deformation is important, using a twisted yarn structure is the best way to increase or modify the stretchiness of stiff fibers; untwisted Galvorn CNT fibers fall into this category, having an elongation of only 1% - 2% before they break. The creation of comfortable and flexible e-textiles is an example of an application in which imparting a bit of elasticity into CNT yarns will be crucial.
The twisted yarn structure also comes with a few drawbacks. Primarily, in spite of the balance of torsional forces that create a ‘locked’ yarn structure, it is possible for twisted yarns to come apart as they are worked, particularly if they are subject to a lot of twisting motion or if the ends of the bundles are unsecured and free to unravel; this is less of a concern in braided yarns. Additionally, the increase in elongation that a twisted yarn imparts to a stiff fiber material can be a drawback for applications that require high stiffness, such as the creation of ballistic fabric or various uses for ropes and cables in which stability is paramount; for such applications, untwisted fiber bundles or braided yarns might be more suitable.
Galvorn Twisted CNT Yarns
We make our twisted CNT yarns through a typical plying technique, as described above; for this process, we use a machine very similar to the one shown in the video below. This is a roll-to-roll process, which allows us to create continuous lengths of tens or hundreds of meters of twisted yarn without interruption. Payoff spools containing bundles of CNT fiber are loaded onto a circular rotating wheel; these bundles are brought together through a central aperture and strung across the length of the machine to a single take-up roll. The wheel is turned by a motor, twisting the bundles around one another as the take-up roll draws them forward; simultaneously, each of the payoff spools is counter-rotated within its place on the wheel. Variable braking force can be applied to the payoff spools in order to ensure that there is proper tension in the bundles, creating a dense yarn structure as they are combined.
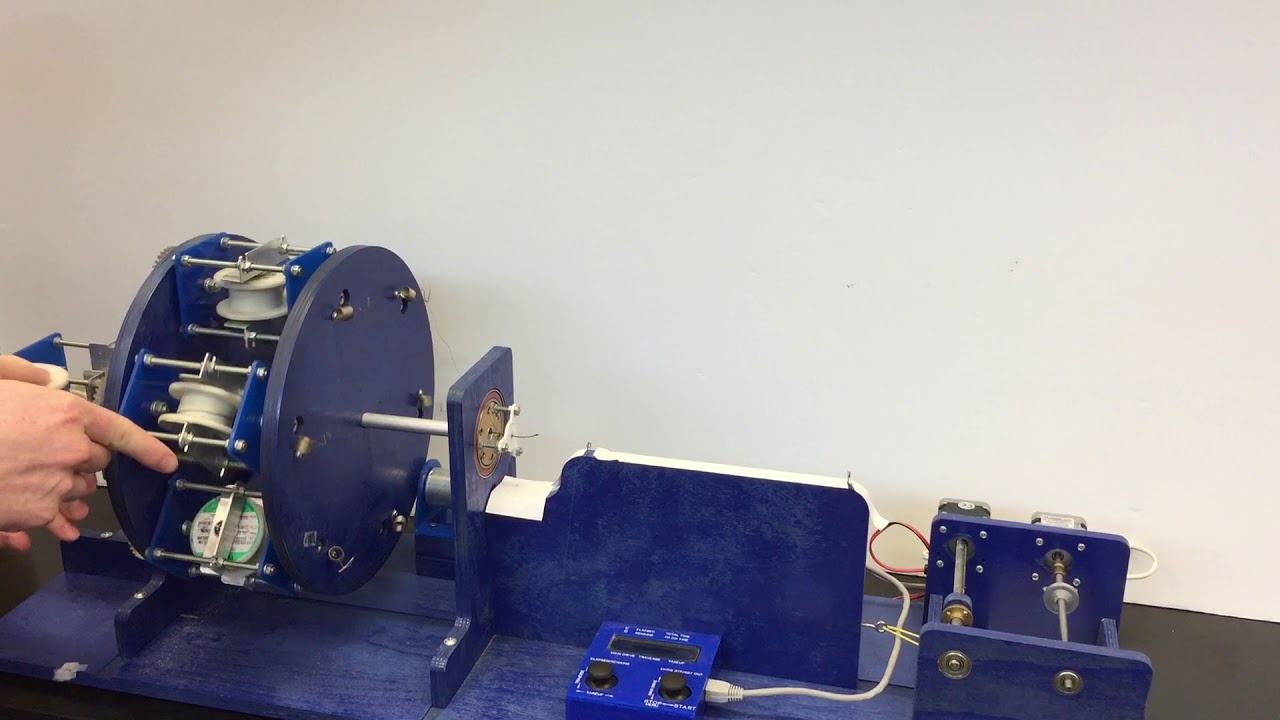
Several parameters can be varied during the production of our Galvorn yarns, and we pay close attention to these parameters to ensure that we maximize the performance and properties of the resulting yarn. One variable is the direction of twist, determining whether the yarn we create will have a “Z” or “S” construction. A second, much more critical, parameter is the degree of twist imparted to the yarn as it is being plied; this can be measured in the number of twists per inch (TPI) of yarn length. Increasing TPI helps us to achieve a high density yarn in which the individual CNT fibers are well packed with one another with very little void space; this is important for the mechanical performance, durability, and abrasion resistance of the yarn. However, we have observed that a high level of twist has a negative impact on CNT yarn conductivity. In addition, the tensile strength of yarn only increases with increased twisting up to a certain point; if the yarn is over-twisted then the tensile strength plateaus and then begins to decline.
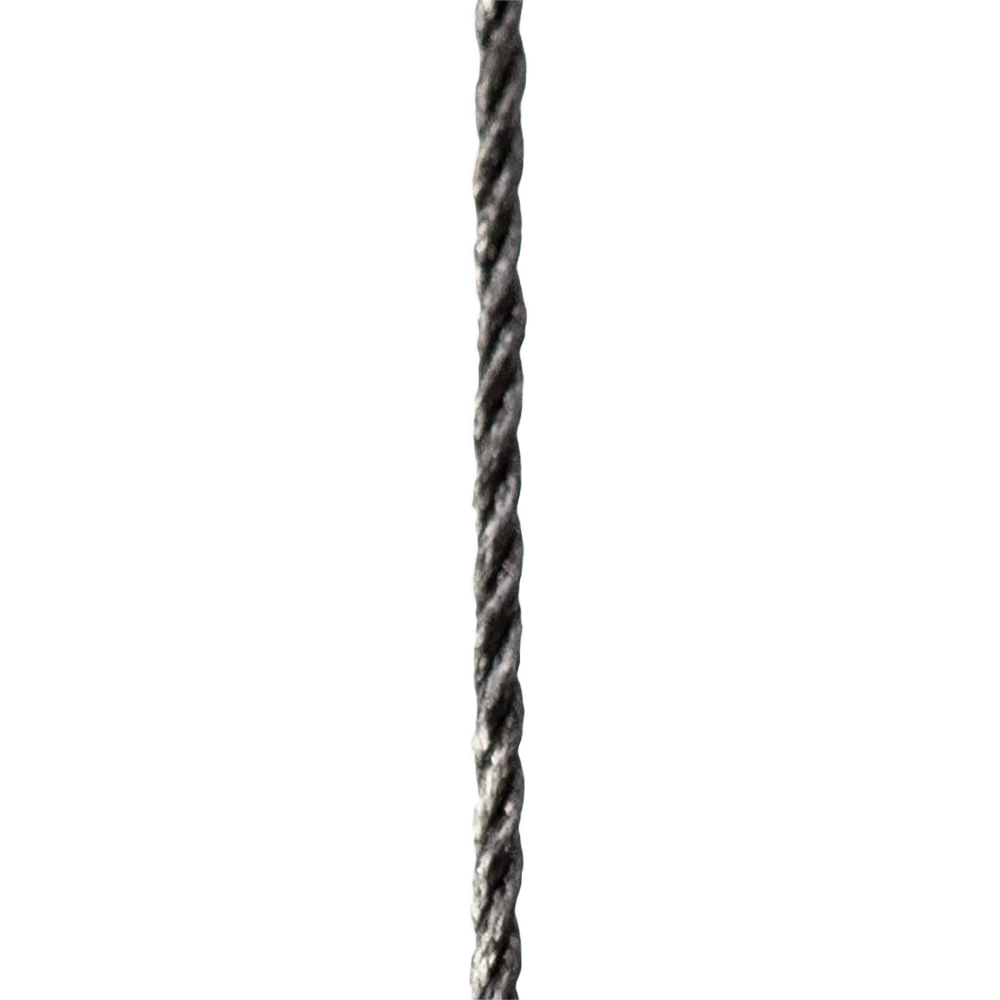
Finally, we can vary the number of CNT fiber bundles that will be combined together to make the yarn. With our current equipment we are able to twist together up to six bundles, and one additional non-twisted bundle can be included to form a core. We have achieved the best yarn properties using a simple 3-ply construction, with three bundles twisted together. However, plying yarn with four or seven bundles is a useful technique when a larger diameter twisted yarn is required. Of course, the yarn diameter can also be increased by increasing the diameter of the constituent bundles, but in some circumstances process limitations or performance requirements may limit the maximum size of the bundles.
The high magnification image below, acquired from a scanning electron microscope, shows off the detailed structure of a Galvorn CNT yarn. This is a 3-ply yarn with a “Z” twist construction; the fiber bundles themselves have a clearly visible “S” twist arising from the counter-twist that was used to lock the yarn during the plying process.
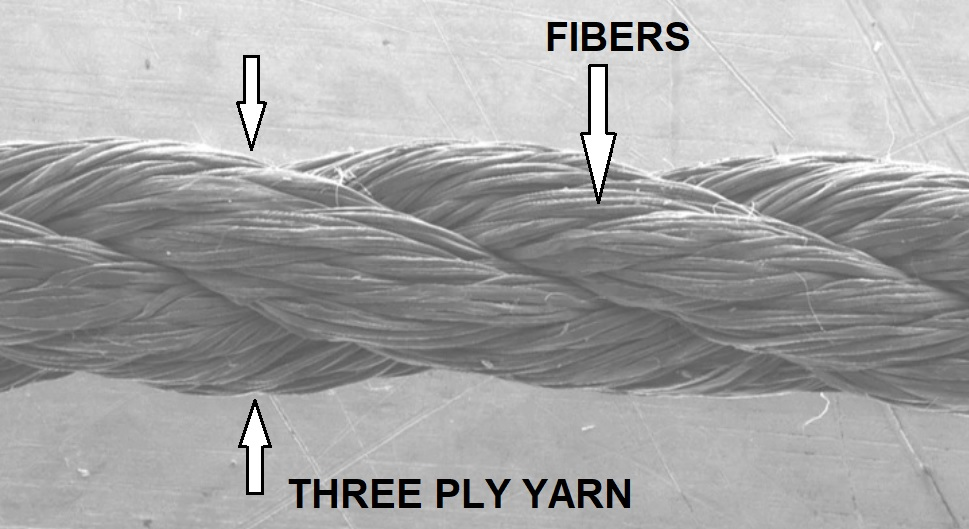
This electron microscope image also provides a useful illustration of one of the drawbacks of twisted / plied yarns compared to braided yarns or individual fibers: plied yarn has a non-uniform diameter and a cross section that is further from being round, especially when it has been plied from only 3 or 4 bundles. This deviation from the more compact cylindrical construction leads to a decrease in the effective density of the yarn. This drawback is more pronounced when larger bundles are used, such as in the creation of large-diameter 3-ply yarn. By following the link below to our online store, you can see that our Galvorn twisted yarn is currently available in diameters up to 500 µm. This does not represent an absolute limit on our capability, but rather a point beyond which we have so far found it easier to achieve high performance using braided yarns, which maintain a more compact cylindrical shape.
More can be said about the challenges and opportunities for optimizing CNT yarn performance, and on the differences between twisted yarn and the various styles of braided yarn. Check back in a week for our next post in this two-part series, in which we will describe the pros and cons of braided constructions. In the meantime, you can follow the link below to see the various yarn products offered in DexMat's online store.