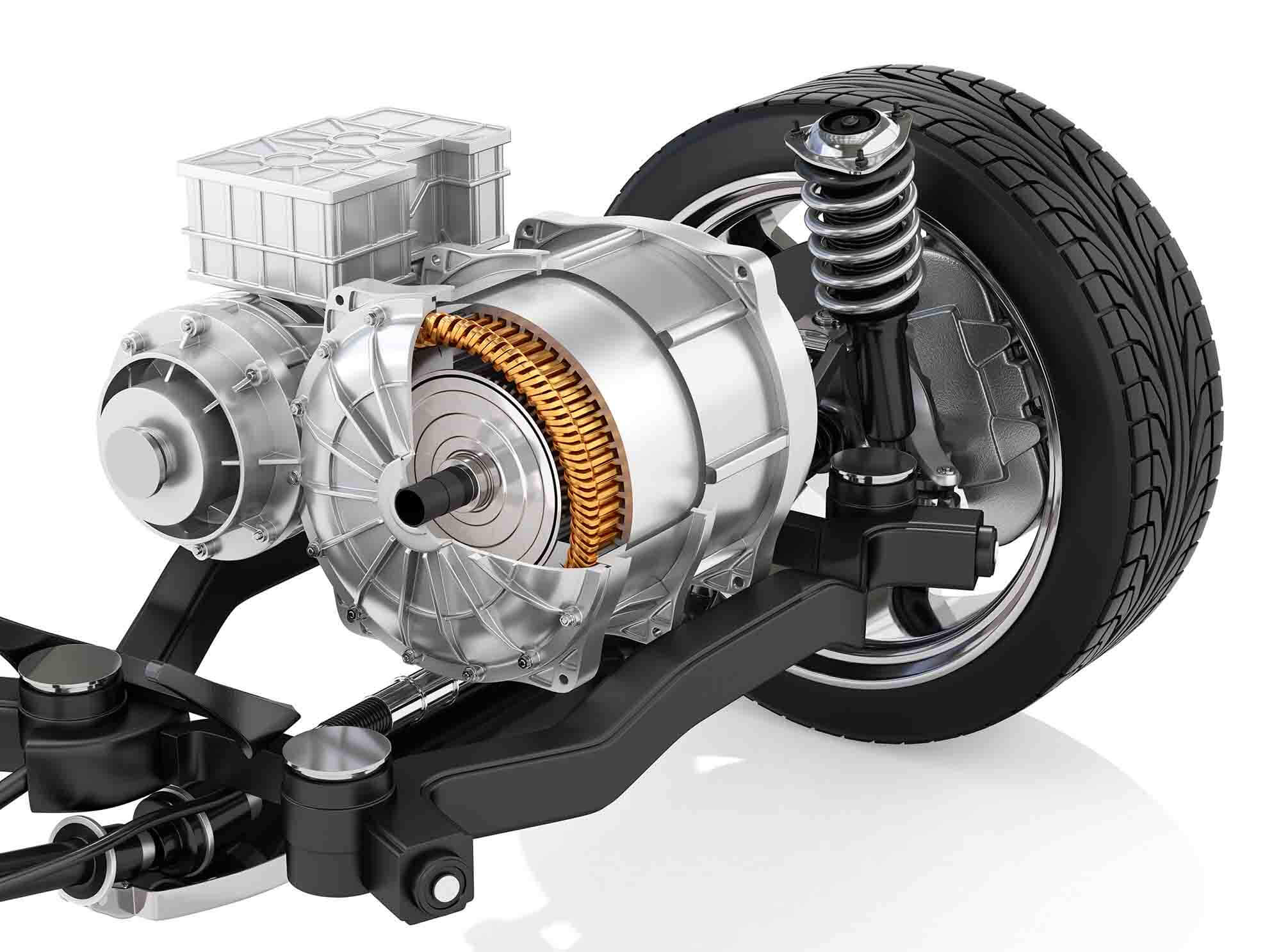
When we examine individual parts of a motor, we can identify areas areas for improvement. We can implement new materials or designs to enhance the motor's performance and efficiency. Improving the efficiency of motor construction and operation starts with the windings. Motor windings are the most basic, but possibly the most important, component of the motor.
Motor windings are designed to produce a magnetic field in response to an electric current. The winding materials are often insulated wires wrapped tightly together in a dense coil.
Superior electric motor windings may be the key to improved performance of electric vehicles. Of course, the demand for efficiency and improved performance goes beyond electric vehicles. It also applies to other devices requiring a tight coil of insulated wire such as generators, transformers, and electromagnets.
The ability to make motors lighter and smaller is necessary to achieve higher power efficiency ratings. In this article, we focus on the winding or magnet wire portion of the motor. We consider the common materials used for these parts, as well as a more advanced material. Galvorn can improve the performance, efficiency, and overall cost of motor and generator winding constructions.
Copper
Copper is the most common magnet wire choice due to its high conductivity and relatively low cost. For most motors, like the one shown below, we use copper with a thin enamel coating. We tightly wrap the wire to create the winding that will build the electromagnetic field to drive the motor.
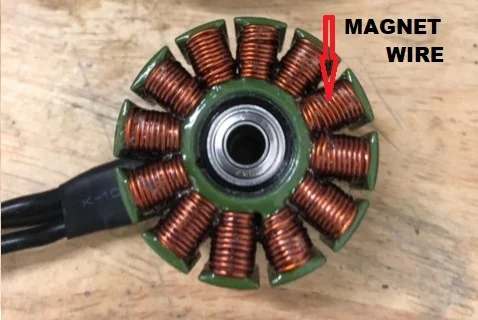
The photo of a drone motor shown above gives a good perspective on how much copper goes into the motor. The material weight is important to increase the efficiency of the motor. Ideally we could decrease the weight of all that copper on the motor while maintaining its power output. The result: we can decrease the amount of power required to fly the drone.
Copper is a great choice for motor windings because of its high conductivity and relatively low cost. But it is also a highly dense and heavy material. It presents a particular challenge for motors used in electric vehicles or aircraft, which need to be lightweight.
Copper will work just fine for most motor applications. Are weight, strength, and stability in high temperature (or other demanding environments) are a requirement? Then we should consider other materials.
Aluminum
If we were considering weight alone, Aluminum wire would be a great choice for magnet wire construction. Aluminum is a commercially available magnet wire option, but it is less conductive than copper. Larger wire diameters and correspondingly larger motors would be necessary to create the same power outputs.
Furthermore, aluminum is more prone to flex fatigue and likely to break more easily after repeated movements. Another downside to aluminum is the increased potential for corrosion and the difficulty of keeping the contacts clean. That degradation can cause a higher localized resistance and potential for connection point thermal failure.
Improvements could be gained by using a combination of aluminum with other metals to increase the conductivity. We can maintain the same physical motor size and the same power output as a motor with copper windings while still decreasing the weight.
Gold and Silver
Wires made from gold and silver offer a low resistance. They are also more corrosion resistant than aluminum or copper. In fact, silver conducts electricity lightly better than copper itself.
However, both gold and silver are substantially more expensive than copper. The increased cost and low availability of these materials make it difficult for these materials to become mainstream magnet wires for electric vehicles and aircraft.
Carbon nanotubes (CNTs)
Galvorn carbon nanotube fibers and yarns offer an incredible combination of properties, gaining the attention of electric motor and power generation industries. They are a highly flexible, strong, and lightweight option for motor winding constructions. Galvorn has a conductivity that is 15 - 20 % that of copper. But it has a history of doubling conductivity every three years.
There may, however, be an advantages in motors that operate at higher frequencies. Galvorn maintains its electrical conductivity at higher frequencies. Copper, on the hand, reduces electrical performance at higher frequency operation.
The flexibility of Galvorn is vastly superior to copper. The CNT fibers are more comparable to that of a textile thread with the ability to survive millions of flex cycles. Combined with its high strength, it is possible to increase packing efficiency of motor windings. Thus, improving magnet wire constructions with faster, more reliable installation methods.
Galvorn is also by far the lightest option for a magnet wire. These CNT fibers and yarns are 9 times lighter than copper wire and 3 times lighter than aluminum wire.
Wire Shape
Material choice plays a large a role in determining a good magnet wire candidate. However, changing the shape of the wire can also improve efficiency. For example, most wiring materials are typically made with a round cross-section. They can, however, also be made into a film or ribbon shape.
A major benefit of the ribbon shape is an increased packing density versus a round wire. The higher packing density can result in a more compact motor with the same power output. However, this construction does come with some drawbacks.
Common problems with wire in the ribbon format include heat retention, flexibility, and installation complexity. With the right combination of insulating materials, the flexibility, thermal capacity, and strength of carbon nanotube films could make them an interesting option for flat magnet wiring.
Hybrid Wire
We can also consider using a mix of materials to make magnet wiring better. Not all electric motors and generators are designed the same way. Not all motors and generators are trying to achieve the same job.
When we compare the requirements of aircraft and the requirements of locomotives we see a large number of differences. An ever-present challenge: how critical the motor weight might be. The one requirement that is universal in every application is increasing the efficiency of power consumption.
That said, designers of future motor tech should consider the needs of different application uniquely. Maintaining an open mind to new materials or a hybrid combination opens the door to new solutions.
One good example of a hybrid wire is a combination of copper and carbon nanotubes. This combination of materials can provide wires with a thermal stability much higher than copper alone. For example, some motors operate at higher frequencies and higher temperature ranges.
A CNT-Cu composite could be the next version of commercialized magnet wire. It would maintain efficiency for electric motors and generators running in harsh and demanding conditions.
In this video, we show some of the experiments done at DexMat to make CNT-Cu composite wires. Watch to see a quick overview of the work. Here, we use an electroplating process to coat carbon nanotube yarn with a layer of copper. The resulting material has both the conductivity of copper and the strength of lightweight carbon nanotube yarn.
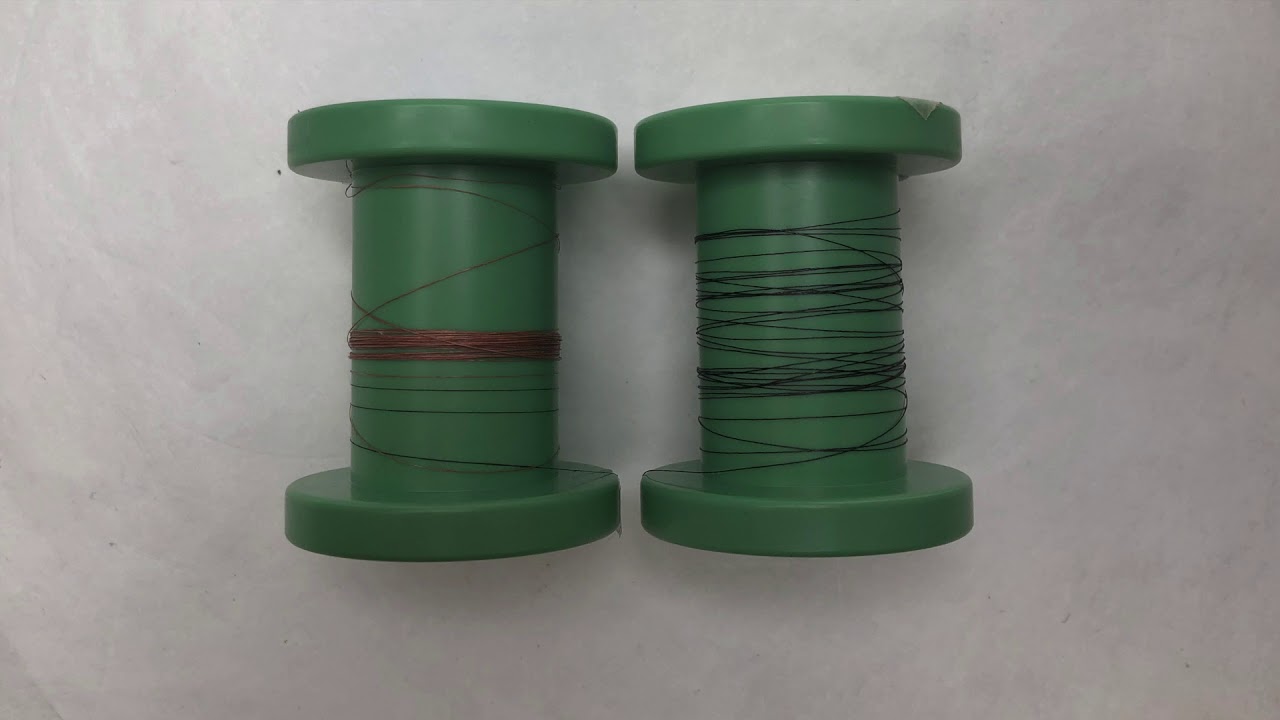
Galvorn offers a mix of high-performance properties uniquely suited to certain applications
Galvorn offers less weight, higher strength, more flexibility, and better thermal conductivity. Its electrical conductivity is lower today, but it can be combined with other materials. Consider this carbon nanomaterial for your next big innovation in magnet wire for lightweight motors.