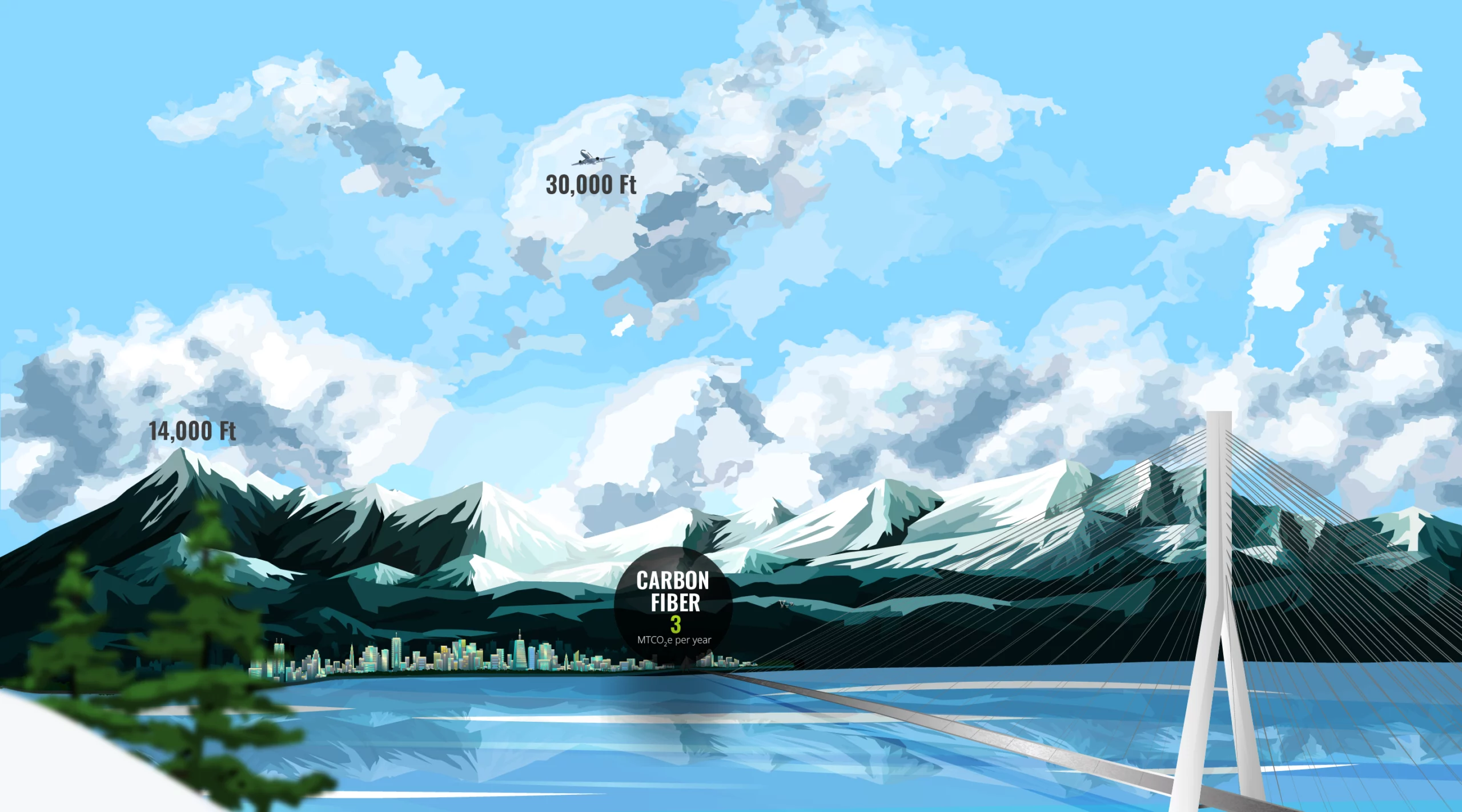
Carbon fiber is prevalent in sports equipment, race cars, boats, wind energy parts, airplane components, and spacecraft. It gained popularity in the late 1950s and industry experts consider it the best materials for lightweight strength. The 1958 invention of “graphite whiskers” was the first example of this high-performance material. Since then it has evolved into a 6.5 billion dollar market, expected to exceed 21 billion by 2032.
The sailing industry, for example, prefers carbon fiber over fiberglass for boat construction. The material is six times harder, half the weight, and twice as strong. These characteristics carry important implications for speed and fuel efficiency of the watercraft.
Carbon fiber is strong and light, making it a top choice in its category. However, it also has drawbacks: It is energy-intensive to produce and it is complicated to manufacture. These realities ensure that it will always be an expensive option for applications that require strength and light weight.
Carbon fiber sustainability is a major challenge. As a polymer, the recycling process is difficult and it is non-biodegradable. The growing concern of its environmental impact is driving the shift to consider more sustainable alternatives.
Below we take a closer look at why carbon fiber is still the leader of the pack across many industries. We examine some of its downsides and discuss high-performing alternatives.
Carbon fiber 101: What is it, what are its current applications?
Carbon fiber is a polymer (also known as graphite fiber). It is generally the material of choice when both high strength and light weight are a requirement.
Because it possesses these highly desirable qualities, carbon-fiber-reinforced composite material has a host of applications. Carbon fiber can be found in airplanes, cars, bikes, golf clubs, and sailboats, and more.
Carbon fiber limitations
While carbon fiber offers many advantages over its precursors, its positive attributes do not come without a cost. Although it is strong in its final form, it is quite dense and brittle at the in its raw form. Producing the carbon fiber end product is inherently energy intensive.
The raw material used to make carbon fiber is called a “precursor.” Although the precise makeup of precursors can vary, 90% of carbon fibers employ polyacrylonitrile as its precursor.
Production depends highly on the specific goals of the end product. A variety of chemicals and mechanical processes are used to manufacture the final carbon fiber composite. Typically, the product goes through many stages, from spinning, stabilizing, and carbonizing, to treating the surface and sizing.
Several of these steps are complex and require high heat. It renders the process both energy intensive, as well as expensive. Making one kilogram of carbon fiber uses 100-900 megajoules of energy, as shown in a new study. Compare this to steel production, where the energy consumption is 20-30MJ per kilogram.
Consider the production costs of carbon fiber. A top-notch assembly line has a capital cost of at least $25 million for the equipment alone.
And the complicated manufacturing process carries with it a substantial environmental toll as well. It takes ten chemical reactions, four phase changes, and four mechanical processes to produce carbon fiber.
According to a recent study, the greenhouse gas (GHG) intensity of carbon fiber production versus steel is striking. Carbon fibers made from polyacrylonitrile produce 24 kg of CO2 per kg. In comparison, steel only produces 2-3 kg of CO2 per kg.
Galvorn carbon nanomaterial is a high-performance sustainable alternative
Galvorn can compete with carbon fiber on performance. Using Galvorn in composites instead of carbon fiber can offer similar benefits, but have less impact on the environment.
Similar to carbon fiber, Galvorn is both strong and lightweight. Galvorn is actually is lighter than carbon fiber (1.6 g/cc), while maintaining high strength (3 GPa). Because it is also significantly more flexible than carbon fiber, it is also more durable and potentially easier to manufacture.
Galvorn also has 10x greater electrical conductivity than traditional carbon fiber composites. In our connected world conductivity opens the door to countless exciting applications. Imagine real-time signals beamed from snowboards, bikes, surfboards, tennis rackets, football helmets, hockey sticks, and more, while maintaining that strength and light weight.
Galvorn has a carbon-negative impact at scale
Galvorn has an impressive combination of highly-valued properties. This carbon nanomaterial is conductive, 10x stronger than steel, half the weight of aluminum, 100x the flex life of copper and carbon fiber, cut-resistant, flame-resistant, biocompatible, and recyclable. Galvorn sacrifices nothing on performance while opening the door to greatly enhanced sustainability.
Galvorn's production process is much more simple and efficient than carbon fiber. It requires only three chemical reactions, two phase changes, and two mechanical processes.
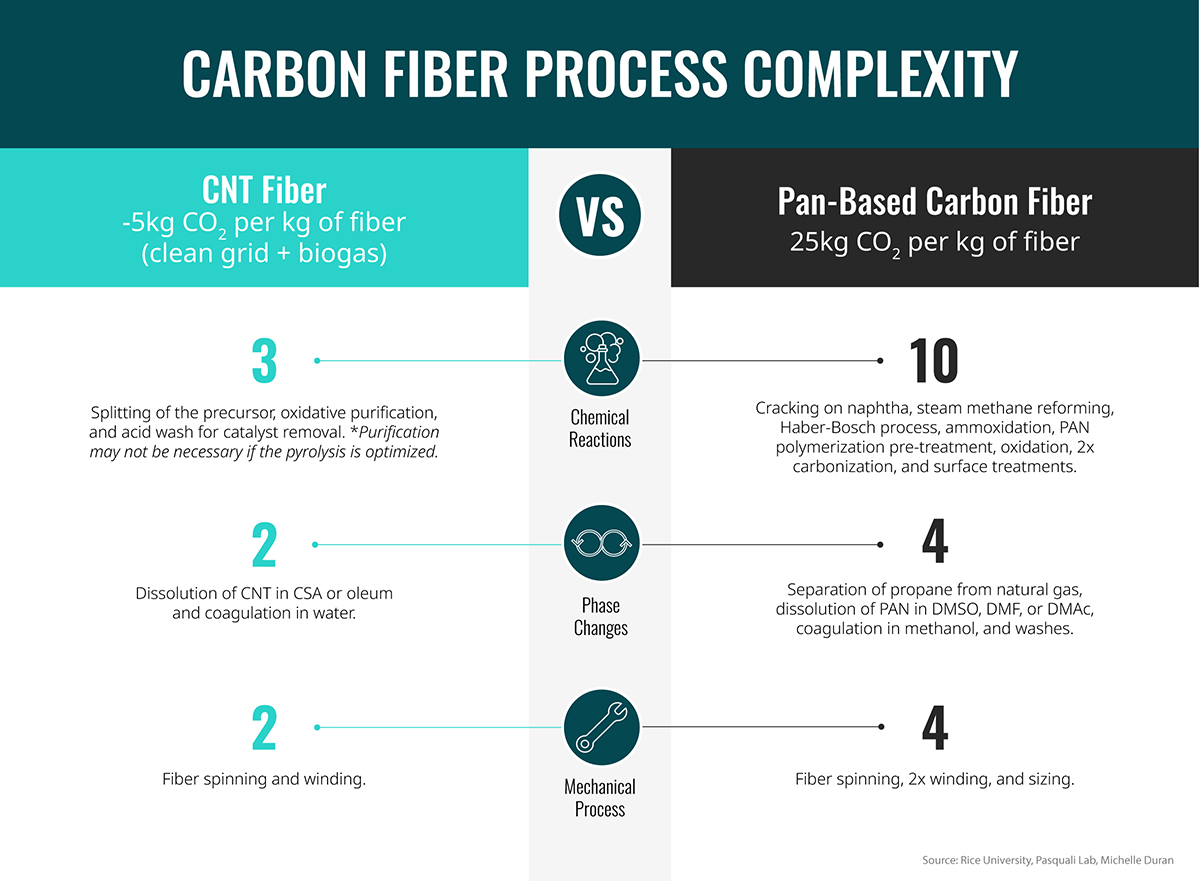
In just a few short years, Galvorn's shrinking carbon footprint will be smaller than steel, copper, and aluminum.
Galvorn is sustainable alternative to carbon fiber, with the potential to make stronger, lighter bicycles, boats, airplanes, and spacecraft. Its benefits are evident in various industries—all while minimizing cost, energy, and emissions.