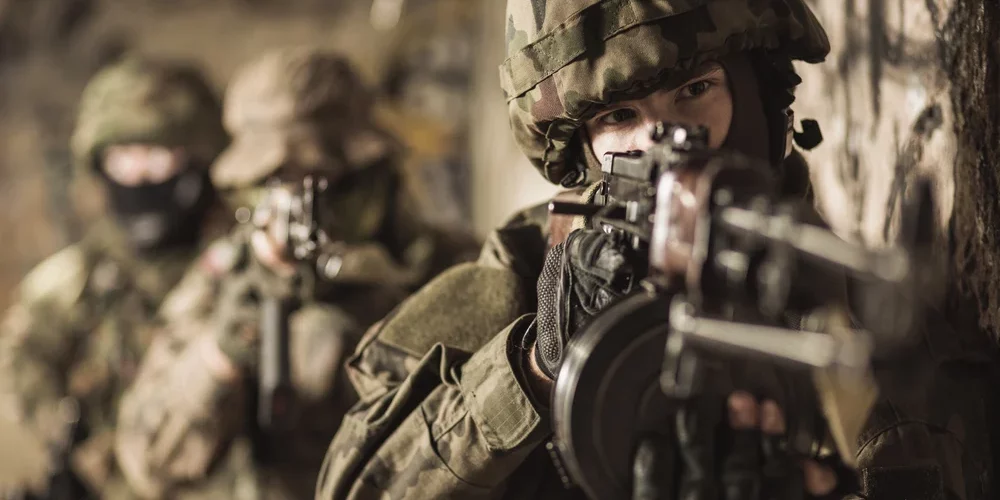
Carbon Nanotube Fiber vs. Aramids vs. UHMWPE
Designing a bullet-proof vest presents a core challenge: balancing robust protection and stopping power with the necessity of lightweight and flexible wear. Traditional thick metal plate armor, while effective, is impractical for daily use.
The mid-20th century saw a breakthrough in synthetic fiber technology, offering a solution. Material scientists developed incredibly tough yet flexible fibers that, when layered, formed a mat strong enough to stop bullets, yet light enough to be incorporated into vests or jackets.
Since then, continuous progress in polymer fiber technology has led to increasingly stronger and lighter ballistic armor. Now, thanks to rapid advancements in carbon nanotube (CNT) material science over the past decade, CNT fibers and their unique properties are poised to rival the most advanced ballistic protection currently available.
Ballistic Fiber Properties
Effective ballistic armor requires specific characteristics. A bullet's impact concentrates significant kinetic energy into a small area, resulting in a high force concentration at the point of impact. The primary function of ballistic armor is to stop the bullet from penetrating the material.
To achieve this, the armor's fibers must possess high tensile strength and high total toughness. Tensile strength measures the stress (force per unit of a fiber's cross-sectional area) a fiber can endure, while total toughness indicates the total energy input a fiber can absorb before fracturing.
Equally crucial is the method of overlapping or weaving the fibers; they must reinforce each other to distribute impact energy across a wider area. The quicker energy dissipates along the fiber strands, the less total energy the fibers at the direct point of impact need to absorb, reducing the likelihood of breakage.
Furthermore, the fibers must absorb this energy without significant stretching, otherwise the wearer will bear a greater portion of the impact. For instance, a vest that absorbs a bullet's energy but stretches several inches like a rubber band would be impractical.
The tensile modulus governs a fiber's ability to rapidly transfer force along its length and resist significant stretching under stress. This property measures stiffness; a stiff fiber with a high tensile modulus can endure substantial stress with minimal elongation.
For ballistic fibers, both tensile strength and tensile modulus are crucial. Since armor must be lightweight for wearability (and lighter materials allow for increased thickness), low density is also essential. Therefore, the most critical properties for ballistic fibers are specific tensile strength (tenacity) and specific tensile modulus, which are the tensile strength and modulus normalized by the material's linear density.
Other vital prerequisites for ballistic fibers include:
- Resistance to wear from flexing and friction
- Resistance to melting and degradation due to heat
- Resistance to chemicals
- Other factors contributing to wearability and durability
Modern ballistic armor typically employs either aramid fibers (e.g., Kevlar, Twaron) or ultra-high molecular weight polyethylene (UHMWPE) fibers (e.g., Dyneema, Spectra).
UHMWPE fibers offer a range of mechanical properties due to their varied formulations. High-performance UHMWPE can slightly surpass aramid fibers in tensile strength and modulus. Furthermore, their lower density results in superior tenacity and specific tensile modulus (as detailed in the table below).
Conversely, aramid fibers demonstrate greater durability against specific chemicals and high temperatures. They also tend to be more flexible than the highest-performing UHMWPE products.
To achieve an optimal balance of weight, strength, and flexibility in ballistic armor, both aramid and UHMWPE fiber types are sometimes combined.
Tenacity (mN/tex) | Specific Modulus (N/tex) | |
Aramid Fibers | 20801 | 49 – 721 |
UHMWPE Fibers | 1610 – 42502 | 87 – 1592 |
Galvorn CNT Fibers | 21613 | 2003 |
Representative specific mechanical properties for aramid, UHMWPE, and CNT fibers. References:
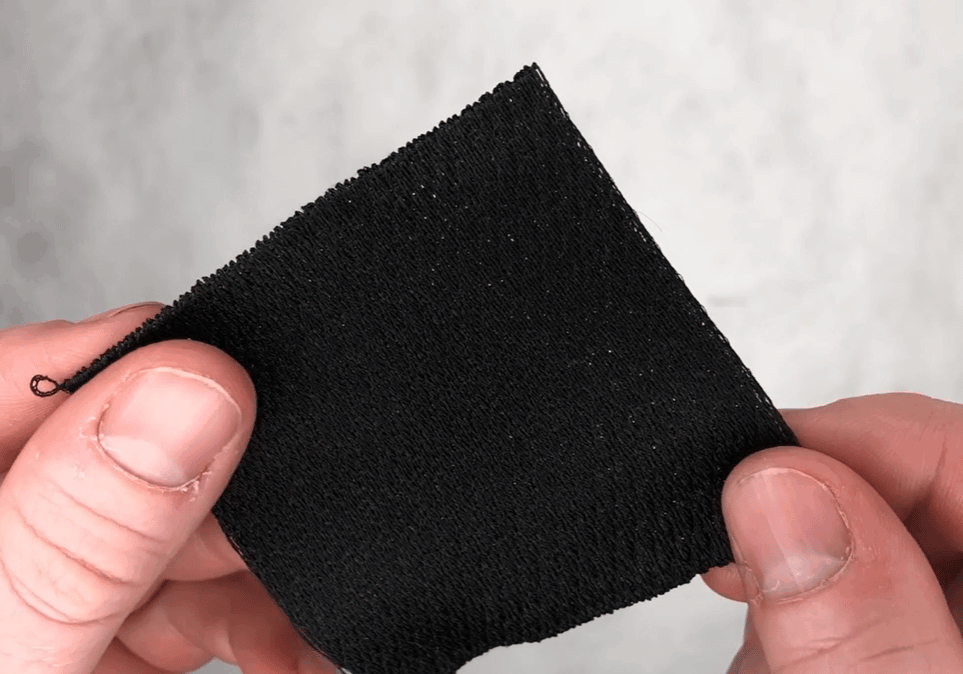
Ballistic Carbon Nanotube Fiber?
With similar high tensile strength, stiffness, and low density to aramids and UHMWPE, CNTs are long-chain molecules ideal for lightweight, high-strength fibers. This potential raises the question of their near-future use in ballistic armor. While past informal tests have shown Galvorn CNT fiber's toughness and resistance to cutting impacts, a deeper comparison of CNT fiber properties to state-of-the-art ballistic fibers is warranted.
A single carbon nanotube (CNT) molecule boasts exceptional tensile strength (up to 100 GPa) and tensile modulus (up to 1 TPa). However, the properties of a macroscopic fiber, composed of millions of interlinked and overlapping CNTs, are contingent upon its assembled structure.
The fiber's tensile strength is dictated by how effectively stress is transferred between neighboring molecules, which in turn depends on their alignment, packing, and the length of their contact interfaces. This determines if molecules slip past each other before breaking. Similarly, the modulus is influenced by the alignment of CNTs within the fiber, as "slack" in the structure can allow stretching before the CNTs themselves bear tension.
Studies have shown that lab-produced CNT fibers subjected to supersonic impact loads exhibit tensile strengths surpassing those of aramid fibers under similar conditions. This suggests their potential for ballistic protection applications may be even greater than their static mechanical properties indicate.
CNT fibers offer additional advantageous properties for ballistic armor, including thermal stability and exceptional chemical resistance. However, their electrical conductivity truly distinguishes them from current ballistic fibers, as both aramid and UHMWPE fibers are insulators. This unique characteristic opens up possibilities for developing ballistic vests that double as smart clothing, incorporating features like biometric sensors, heating elements, or other electrical functionalities.
CNT fibers could very well displace the current generation of ballistic polymers and herald a new generation of ultra-lightweight body armor.