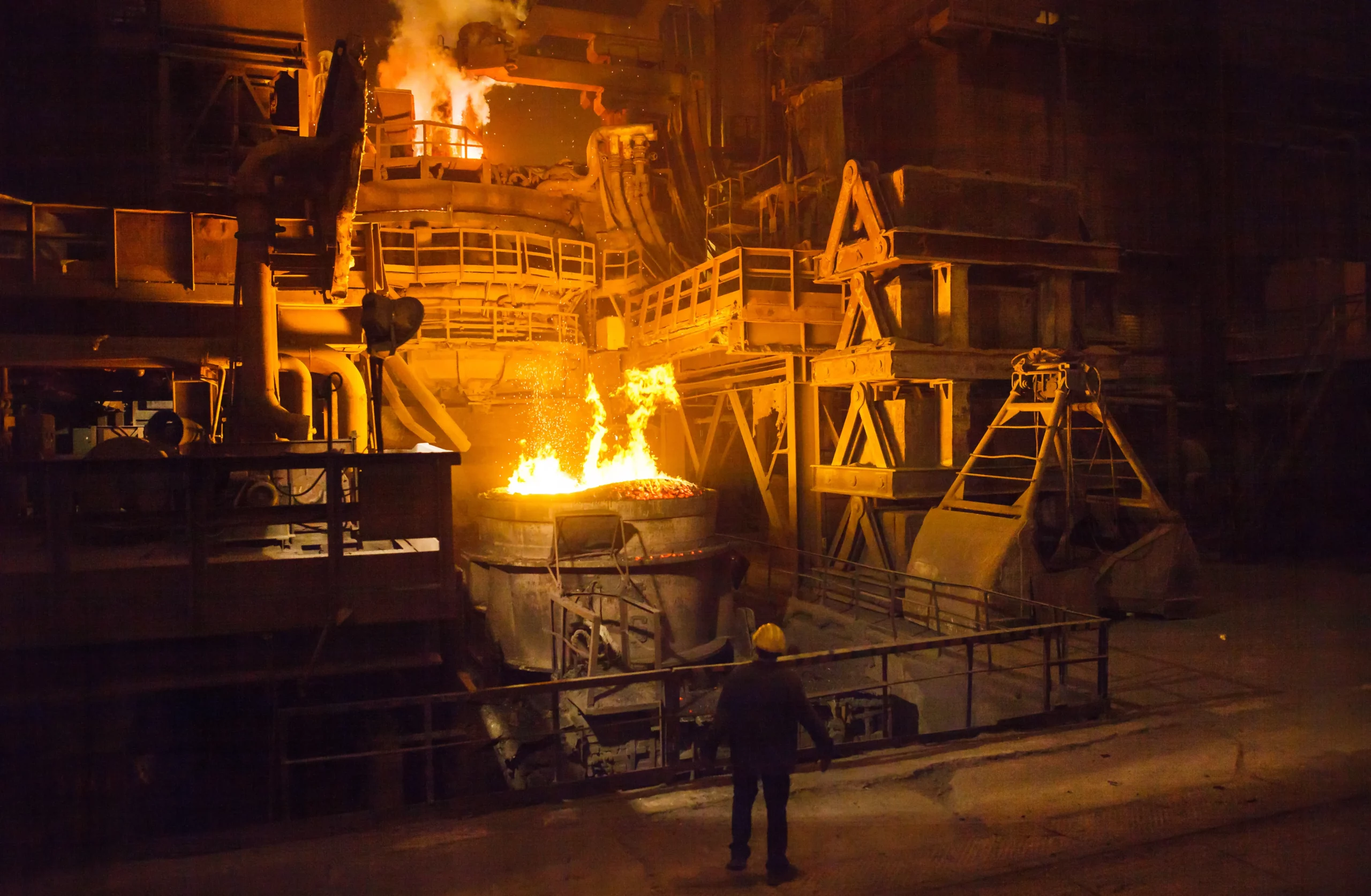
In a "full circle" moment, I'm elated to share that, five years after founding Third Derivative (D3), and two and a half years after stepping away from leading it to join DexMat as CEO, DexMat is now joining D3's inaugural Industrial Innovation Cohort focused on decarbonizing steel.
The challenges our fellow startups are tackling are of paramount importance, as the steel industry alone contributes 7-9% of global emissions. The problem is massive, but the good news is that there are many solutions to solving it. The many members of this cohort are a testament to that. Shoutout to the other members of our steel cohort: Binding Solutions Limited, Greenore, Helios, Hertha Metals, Inc., and SUN METALON. Like DexMat, the solutions they are bringing to market are not simply making legacy materials “greener,” but as D3 notes in their announcement, their portfolio theses come down to three categories:
- Can we make less material? Reduce materials demand by substitution, recycling, upcycling, and increasing supply chain and material use efficiency.
- Can we make better materials? Reducing emissions in existing processes through direct electrification, materials and feedstock innovations, and process efficiency.
- Can we make new materials? Disruptive technologies and novel processes to fundamentally change how materials are produced, with low or zero emissions.
The key challenge in fulfilling these theses is not constraining tomorrow’s solutions to the problems created by yesterday’s technologies. Centering decarbonization on the perpetuation of steel, a millennia-old technology, artificially reduces our solution space to treating symptoms rather than the underlying disease. “Green” steel production uses green hydrogen (or other clean or renewable energy sources) to reduce CO2 emissions. However, we must also find new and better alternatives. Here’s my take on the limitations of green steel and why we need to use first principles to expand our solution space to include steel alternatives.
"Green" steel is at a fundamental disadvantage for several techno-economic reasons, including:
#1 Steel production is an energy intensive process—and clean energy is a limited resource. Even if you’re only using clean energy to produce steel, you still need a lot of energy. The IEA finds that a transition to “green” steel production increases the sector’s electricity demand by 60%.
Global demand for energy already outpaces the supply of clean energy (and that supply is not readily available everywhere). Allocating clean energy to the production of an inferior material is irresponsible; that clean energy has better decarbonization ROI in other sectors.
#2 Clean hydrogen is expensive. Much of the focus on “green” steel is predicated upon using clean hydrogen sources. Hydrogen is energy dense, which seems a fitting match for energy-intense steel production.
However, clean hydrogen production is expensive and would require significant subsidies to be economic for steel. Bloomberg NEF predicts that any clean hydrogen projects operating by 2030 will have production costs between $3 and $5 per kilogram, at a minimum.
From the perspective of steel plants, clean hydrogen needs to be cost-competitive with natural gas. This would require clean hydrogen to sell at about $2.50 below production or import cost. Scaled globally, "finance ministries of the world would need to slap no less than $2.3 trillion dollars on the table [to hit stated clean hydrogen supply targets], and do it in time to build the projects before 2030.”
To put that in perspective, for $2.3 trillion dollars, DexMat could build enough Galvorn production capacity to displace all global steel production globally! The economics of clean hydrogen for “greening” steel production simply don’t pencil out.
#3 There isn't enough clean hydrogen. According to Bloomberg, just under $280 billion has been committed to fund clean hydrogen around the world. In this article, Michael Liebreich estimates that investors will disburse just $200 billion of that amount in time to produce clean hydrogen by 2030. He also estimates that the production of low-carbon hydrogen in 2030 would be no greater than 15 million tons.
15 million tons of hydrogen can supply about 450 terawatt hours of electricity. According to the IEA, “greening” global steel production would require more than 1900 terawatt hours of electricity today, and likely more by 2030. At 15 million tons of production capacity, clean hydrogen could only power a fraction of that demand.
#4 It is extremely expensive to retrofit existing steel plants. Converting existing coking-coal based plants requires billions of dollars of investment. On top of this capex, these retrofitted plants then incur “hundreds of millions more per year in higher running costs.”
According to RMI, as of 2019 all the steel mills from all the companies currently investing in or committing to zero-carbon technology only represented 8% of global steel production. There have been many decarbonization targets set and commitments made, but actions speak louder than words; greater capex and greater opex limits the speed and scale of “green” steel deployment.
"Green" steel is also at a disadvantage from a broader environmental and performance impact:
#1 “Green” steel does not avoid the environmental impacts of mining, which include deforestation, noxious air pollution, and toxic liquid waste. It only addresses CO2 emissions.
#2 Steel, green or not, is no longer the highest performing material on the market. The metal is heavy, brittle, susceptible to corrosion, and can fail with fluctuations in temperature.
This is why, for many applications, alternative materials have already displaced steel based on performance. For example, carbon fiber has displaced steel (and aluminum) in automobiles, aircraft, and bicycles, as well as in power transmission line cores. The lightweight, super strong, and non-corrosive material is also seeing growing adoption in building and construction.
Carbon fiber is problematic in other ways—slow/expensive to produce, and even dirtier than steel—but it has demonstrated that markets and applications are ready to upgrade from steel to materials with superior properties.
There can be no energy transition without a materials transition.
Whether you're concerned about the economics or the climate impact, it’s hard to justify “green” steel over alternative materials.
Materials like Galvorn are inevitable. Over the arc of human history, materials with better properties and lower costs that enable new applications and generate less waste inevitably hit an inflection point and displace their legacy incumbents at global scale—so much so that we even name eras of human civilizations after them.
Whether Galvorn hits that inflection point in centuries, like steel, decades, like plastics, or years has gigaton-scale climate implications. Accelerating our path to that inflection point is where we think the D3 ecosystem will be catalytic for DexMat’s progress.
As I have said since the earliest days of D3: together, and only together, will we build the sustainable, prosperous, equitable future. I am both grateful and excited to be back together with my D3 and RMI colleagues, and together for the first time with these other amazing startups in the Industrial Innovation Cohort. Let’s go!