DexMat receives Air Force funding to produce next-gen cathodes
Earlier this year DexMat was awarded funding by the U.S. Air Force to continue developing a Galvorn CNT cathode. Previous work has demonstrated that Galvorn CNT fibers can out-perform the current state-of-the-art flocked carbon fiber cathodes, while also achieving scalable production. In this post, we discuss how a Galvorn woven cathode works so well, and what it means for the future of field emission applications.
Why is Galvorn a great material for field emission cathodes?
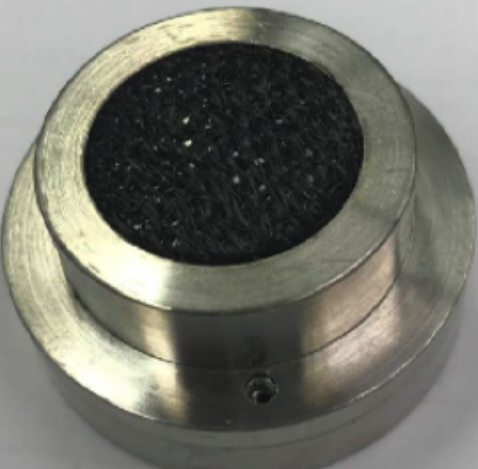
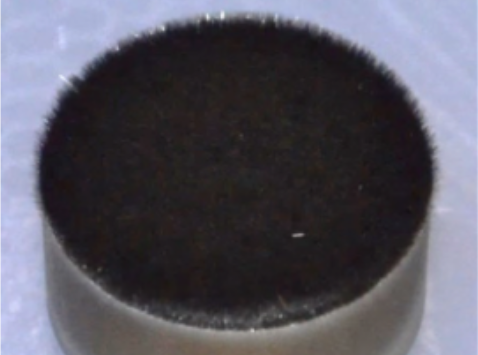
Above: (Left) Galvorn CNT Cathode, (Right) Flocked Carbon Cathode
Performance
One of the initial prototypes that DexMat has developed is a knitted Galvorn CNT cathode. Field emission tests show that this cathode performs more than 20x better than the existing state-of-the-art cathode in terms of emitted current. How is this possible? Galvorn’s electrical conductivity is two orders of magnitude greater than graphite, and its high thermal conductivity, coupled with the stable molecular structure of CNTs, allow it to withstand massive amounts of energy. The conductivity enables lower turn-on voltages, meaning it is faster to power and thus increases the repetition rate of the device. It also produced 350x more current per equivalent field strength (measured in volts per unit length, ex. meters) under DC testing in a laboratory setting. In other words, Galvorn is 350x more productive at turning current into directed energy.Â
Scalable Manufacturing
The performance benefits are clear, but Galvorn also has a notable manufacturing advantage. For all its super strength and conductivity, it is flexible and behaves like any textile.
Above: Galvorn fabric. Super strong yet super flexible fibers have an almost silk like feel.
To develop the cathode was as simple as knitting Galvorn into the right size and shape for the device. Current state-of-the-art flocked carbon fiber cathodes are complex and expensive to produce. Previous work on Galvorn CNT fibers and Galvorn CNT fiber cathode manufacturing, with feedback and funding from Air Force Research Laboratory (AFRL), has shown that using CNT fibers in field emission cathodes can achieve scalable production. The cathodes can be produced more quickly, reliably, and at a lower cost than the current state-of-the-art.
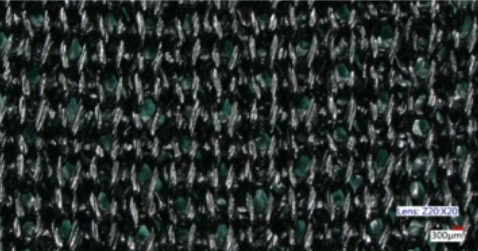
Left: Galvorn knitted fabric. The textile form factor enables scalable production. It can be produced more quickly, reliably, and at a lower cost than the current state-of-the-art graphite cathode.
DexMat is continuing to scale up Galvorn production capacity and bring costs down, ensuring the suitability of this solution for mass production. Yet even now, at its current price point it is more economical than the current state-of-the-art which sells for over $3,000 per cathode.Â
Field emission technology in commercial applications
Technologies that leverage the emission and acceleration of electrons have many applications beyond defense, including:
- The creation of X-rays for medical and industrial imaging.
- The amplification of radio waves in TV, terrestrial microwave, and satellite communication.
- The radar used for Air & Sea traffic monitoring, as well as weather tracking.
- The precision high power requirements of a modern particle accelerator.
The possibilities abound when you have a material that is conductive, super strong, super lightweight–and behaves like a textile. We are grateful to the AFRL for their continued support and look forward to sharing future results from our work in this space. In our next post, we will dive further into the process of field emission and the physical properties that are proving to make Galvorn carbon nanotube fibers so suitable for this application.