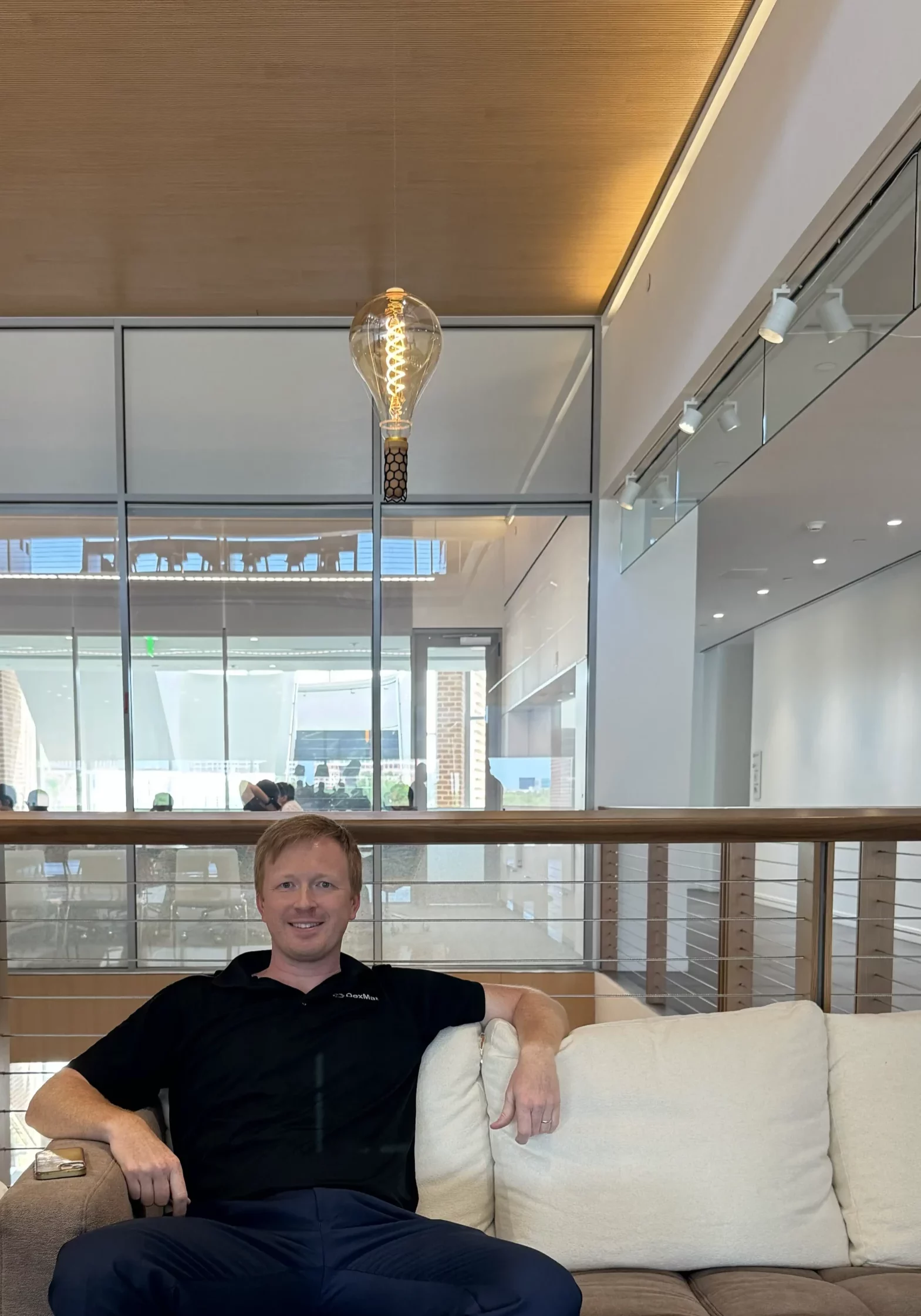
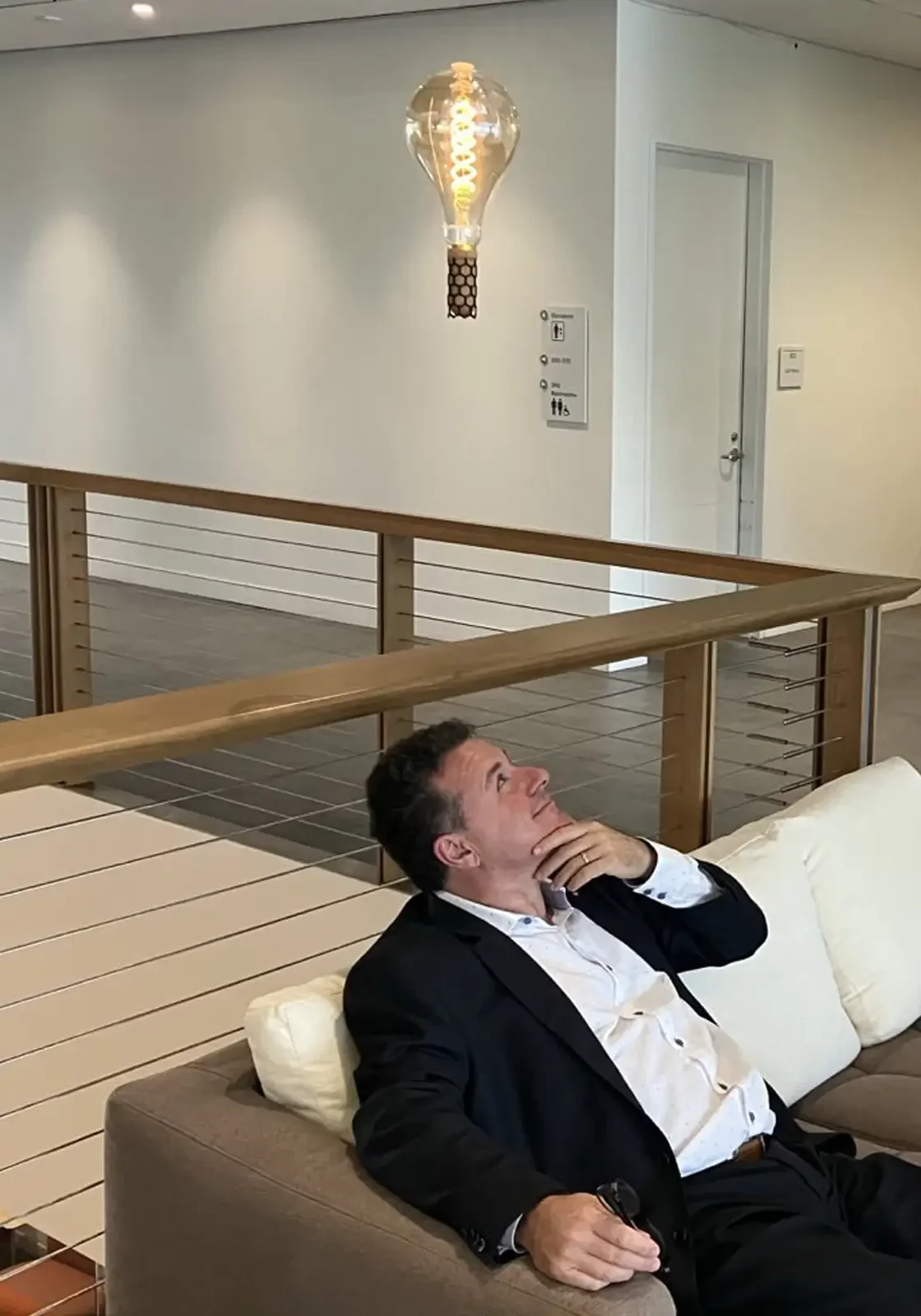
We have officially wrapped up Carbon Hub 2025 where we are gathered here at Rice University with industry, academic, and research leaders for two days of networking, panel discussions, and technical updates focused on advancing sustainable carbon materials and decarbonization.
Seeing how much this event has grown over the years we cannot help but reflect one of the most eminent figures in solid carbon’s origin story: Richard E. Smalley, a Nobel Prize-winning chemist whose visionary work laid the foundation for these remarkable materials.
We are not alone in this thinking. Over the weekend students of Professor Matteo Pasquali, who continued the work and vision of Smalley after his passing in 2005, along with the help of other Rice University staff stealthily set up an installation to honor these origins.
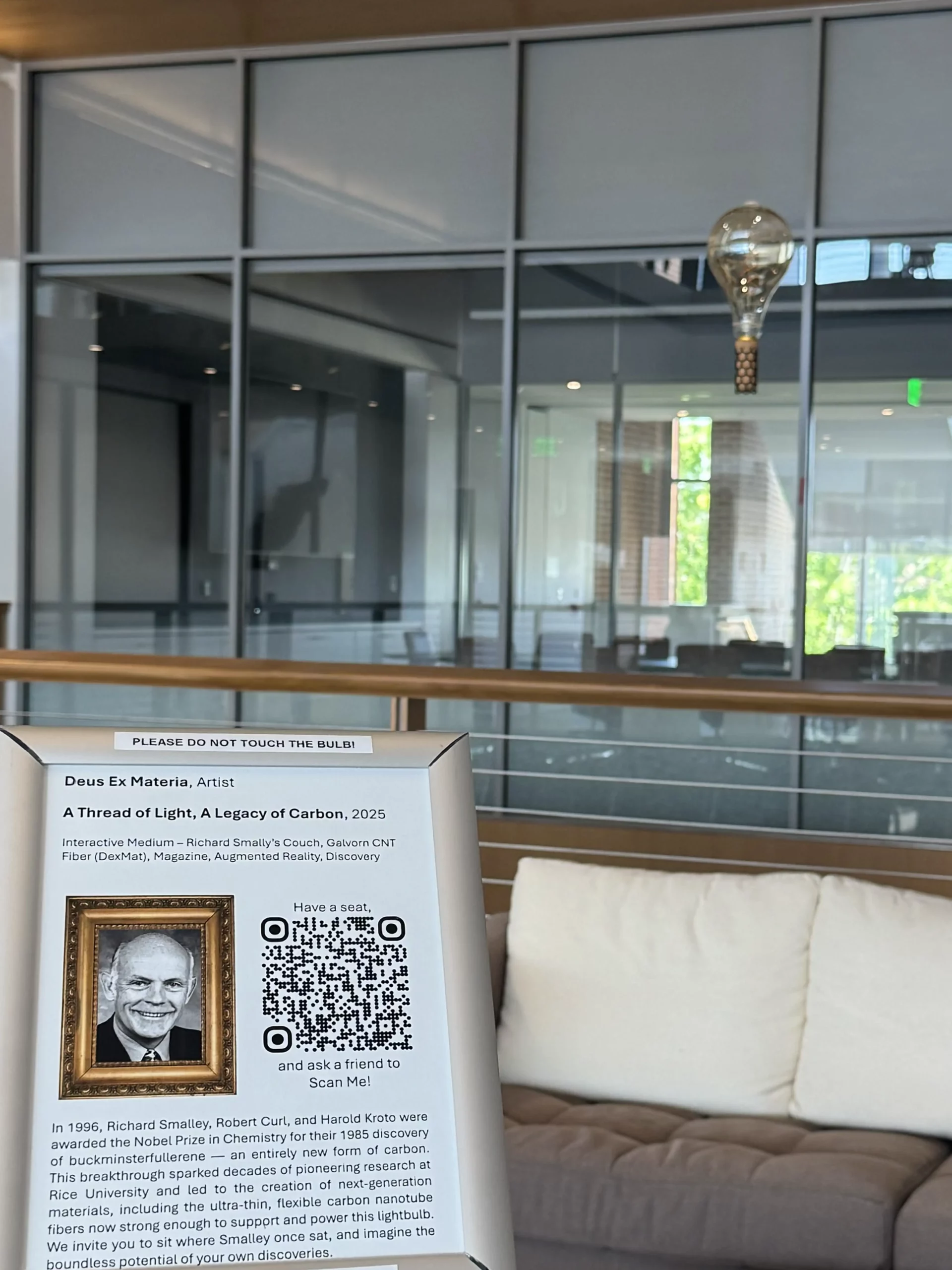
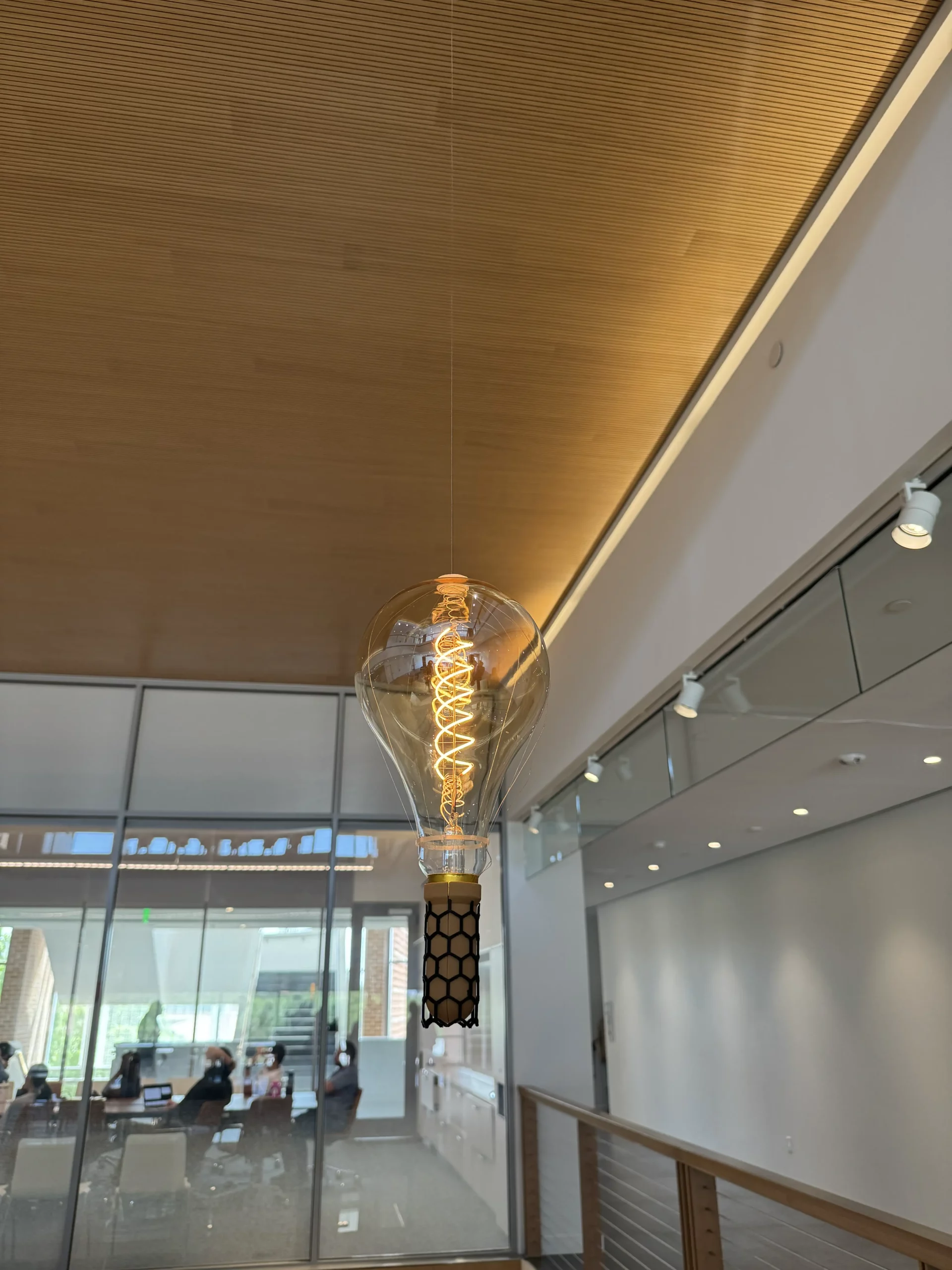
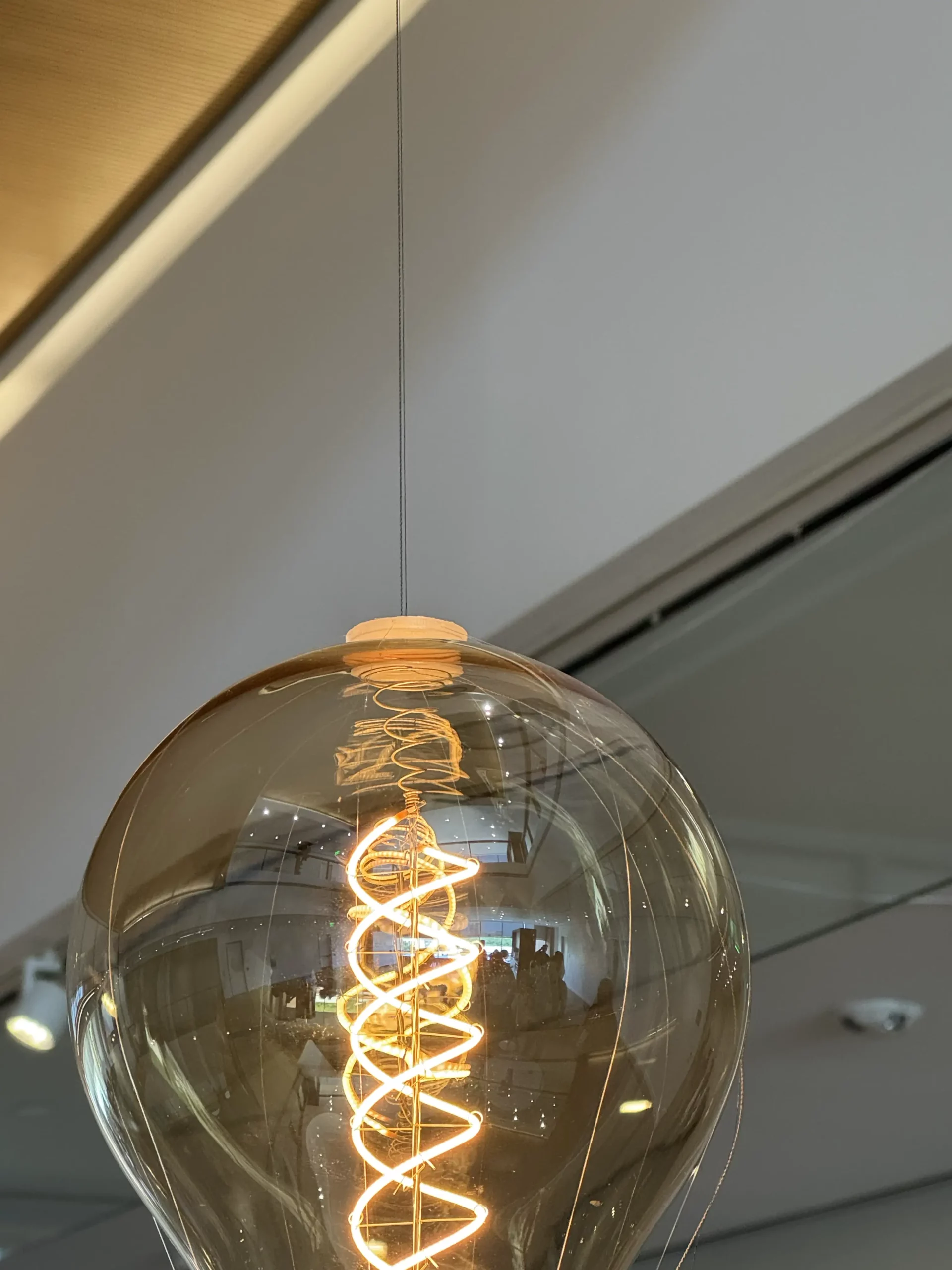
In this post we explore Smalley's critical role in developing wet-spun CNTFs, the impact of his contributions, and the exciting opportunities that lie ahead.
Carbon nanotubes (CNTs) are renowned for their extraordinary strength, electrical conductivity, and lightweight properties, making them a cornerstone of nanotechnology. Among the many advancements in CNT applications, wet-spun carbon nanotube fibers (CNTFs) stand out for their potential to revolutionize industries like aerospace, electronics, and energy.
Richard Smalley's Role in Wet-Spun Carbon Nanotube Fibers
Richard Smalley, co-discoverer of buckminsterfullerene (C60) and a 1996 Nobel laureate, was a trailblazer in nanotechnology. His work at Rice University’s Carbon Nanotechnology Laboratory (CNL) extended beyond fullerenes to carbon nanotubes, which he saw as transformative for materials science. In the early 2000s, Smalley turned his attention to creating macroscopic CNT structures, particularly fibers, that could harness the nanoscale properties of individual CNTs—strength surpassing steel and conductivity rivaling copper—on a practical scale. (Here’s our post on the transformative distinction between carbon nanotubes (CNTs) and carbon nanotube fibers (CNTF): A Misconception that Obscures the Real Progress of Solid Carbon.)
Smalley’s pivotal contribution to wet-spun CNTFs began with his collaboration with Matteo Pasquali and other researchers at Rice University. In 2000, Smalley’s team started exploring wet-spinning, a technique inspired by industrial processes used for high-performance fibers like Kevlar and Zylon. Wet-spinning involves dissolving CNTs in a liquid, extruding the solution through tiny holes, and solidifying the strands into continuous fibers. However, early attempts faced challenges: CNTs were difficult to dissolve, and the resulting fibers lacked the strength and conductivity needed for practical applications due to misalignment and gaps between nanotubes.
A breakthrough came in 2004 when Smalley, Pasquali, and their team published a landmark paper in Journal of Physical Chemistry B, demonstrating the use of a solvent that allowed stable, high-concentration CNT dispersions. This innovation enabled the formation of thermodynamically stable spinning mixtures, which were extruded into coagulants to produce highly aligned, densely packed CNTFs. Unlike earlier methods, the new approach was reversible and non-destructive to the CNTs, preserving the CNTs’ large aspect ratios and intrinsic properties.
Smalley’s vision was to create “buckycables”—continuous, kilometer-long CNT fibers that could serve as ultra-strong, conductive replacements for traditional power transmission cables. His work established an industrially relevant wet-spinning process, drawing parallels with commercial aramid fiber production. Following Richard Smalley's passing in 2005, Matteo Pasquali, a founding member of the project and DexMat's Co-Founder and Chief Science Advisor, continued the research.
The foundational research that Smalley led set the stage for subsequent advancements, including a seminal 2013 publication by Pasquali’s team showing that very highly aligned and densified CNTs led to CNTF with metal-like conductivity and the strength of carbon fibers. This team included Dmitri Tsentalovich, PhD, now DexMat Co-Founder and CTO; Colin Young, PhD, now DexMat Senior Research Scientist; and Natnael Behabtu, now DexMat Production Advisor. Over the years, the team continued to improve the properties, eventually founding DexMat to scale up and commercialize the material we now call Galvorn.
Impact of Smalley’s Contributions
Smalley’s pioneering work on wet-spun CNTFs has had a profound impact across scientific and industrial domains:
- Scientific Advancement: Smalley’s introduction of CNT wet-spinning provided a scalable method to translate the nanoscale properties of CNTs into macroscopic materials. The solution spinning process Pasquali and his team built from Smalley’s work remains a cornerstone of CNTF research, enabling fibers with tensile strengths up to 4.2 GPa, electrical conductivities of 10.9 MS/m, and thermal conductivities rivalling metals and traditional carbon fibers.
- Industrial Relevance: By adapting wet-spinning techniques from established fiber industries, Smalley’s work made CNTF production compatible with existing manufacturing infrastructure. Collaborations with companies like Teijin Aramid, initiated during his tenure, led to fibers that combine the strength of carbon composites with the conductivity of metals, as reported in a 2013 Science paper. Despite lower conductivity, these fibers rival copper in current-carrying capacity and are lighter, making them ideal for aerospace and defense applications.
- Inspiration for Innovation: Smalley’s vision of CNTFs as a transformative material inspired a generation of researchers. His ambitious ideas, such as space elevators and ultra-efficient power transmission, continue to drive research into high-performance fibers. The Richard E. Smalley Institute for Nanoscale Science and Technology at Rice University, named in his honor, remains a hub for CNTF advancements.
- Commercial Potential: Smalley’s work catalyzed commercial interest in CNTFs. Today DexMat is the leading provider, producing Galvorn with unmatched properties and utilizing a production process that can achieve kiloton scale. In fact, since Galvorn’s invention, DexMat has scaled up production capacity more than 3,000x, while bringing costs down 99.6%.
Opportunities Ahead
The legacy of Smalley’s work on wet-spun CNTFs opens up a wealth of opportunities for future innovation:
- Energy Transmission: As global demand for renewable energy grows, CNTF-based cables could revolutionize long-distance grids with stronger, lighter cables, supporting solar and wind farms. Smalley’s vision of “buckycables” is closer to reality, with ongoing research improving fiber conductivity and scalability. You can learn more about DexMat’s ongoing work with Prysmian (funded by the U.S. Department of Energy) in this post: The Future of Advanced Conductors: ACSR vs. ACCC vs. Galvorn ACNT.
- Aerospace and Defense: Lightweight, strong, and conductive CNTFs are ideal for aerospace applications, where weight reduction is critical. Opportunities include wiring for satellites, UAVs, and aircraft, electromagnetic shielding, as well as structural composites for aircraft. The U.S. Air Force and other defense entities have supported CNTF research, signaling strong potential for military applications. Learn more about our work advancing field emission with the Air Force in this case study.
- Smart Textiles and Wearables: CNTFs’ flexibility and conductivity enable their use in e-textiles, such as smart clothing with embedded sensors for health monitoring or antennas for communication. These applications align with the growing wearable technology market, offering durable, washable, and corrosion-resistant alternatives to traditional electronics. Download Unlocking the next generation of smart textiles with Galvorn.
- Medical and Biotechnology: CNTFs’ biocompatibility and conductivity make them suitable for medical implants, such as neural interfaces or corrosion-resistant electrodes. Research into CNTF-based scaffolds for tissue engineering could lead to breakthroughs in regenerative medicine.
- Sustainability and Scalability: Advances in CNT synthesis, such as deep-injection floating-catalyst chemical vapor deposition (DI-FCCVD), promise high-aspect-ratio CNTs at lower costs. Combined with wet-spinning, these developments could make CNTFs competitive with carbon fibers and metals. Sustainable production methods, like recycling CNT films, are also emerging, aligning with global sustainability goals. In fact, Professor Pasquali and his team, including Oliver Dewey, PhD, DexMat Process Development Engineer, recently published their work on recycling CNTs in the journal Carbon.
Smalley’s emphasis on interdisciplinary collaboration continues to guide research in these areas. That spirit lives on in the annual gathering at Carbon Hub, as well as the work we do here at DexMat, working closely with upstream suppliers, downstream manufacturers, and end-use customers to actualize a solid carbon value chain that can have gigaton-scale climate benefit.
From Extraordinary Vision to Tangible Technology
Richard Smalley’s pioneering work on wet-spun carbon nanotube fibers transformed a visionary idea into a tangible technology with far-reaching implications. His introduction of CNT wet-spinning enabled the creation of high-performance CNTFs, bridging the gap between nanoscale properties and macroscopic applications. The impact of his contributions is evident in the scientific advancements, industrial collaborations, and commercial potential that followed, including, of course, the founding of DexMat.
Looking ahead, Galvorn CNTFs will revolutionize energy, aerospace, textiles, and medicine. The kilometer long “buckeycables” are available today with more and more customers taking advantage of Galvorn’s exceptional properties. Smalley’s legacy as a visionary scientist continues to inspire us, reminding us that the “strongest damn thing in the universe” is within our reach. Or as we like to say, the lightest, strongest, and most flexible conductive material on the planet.
At Carbon Hub 2025, the DexMat team showcased a swing, replacing its steel chain rope with Galvorn. Galvorn is many times stronger than steel and just 5% the mass of the steel chain it replaced. This is just the beginning.
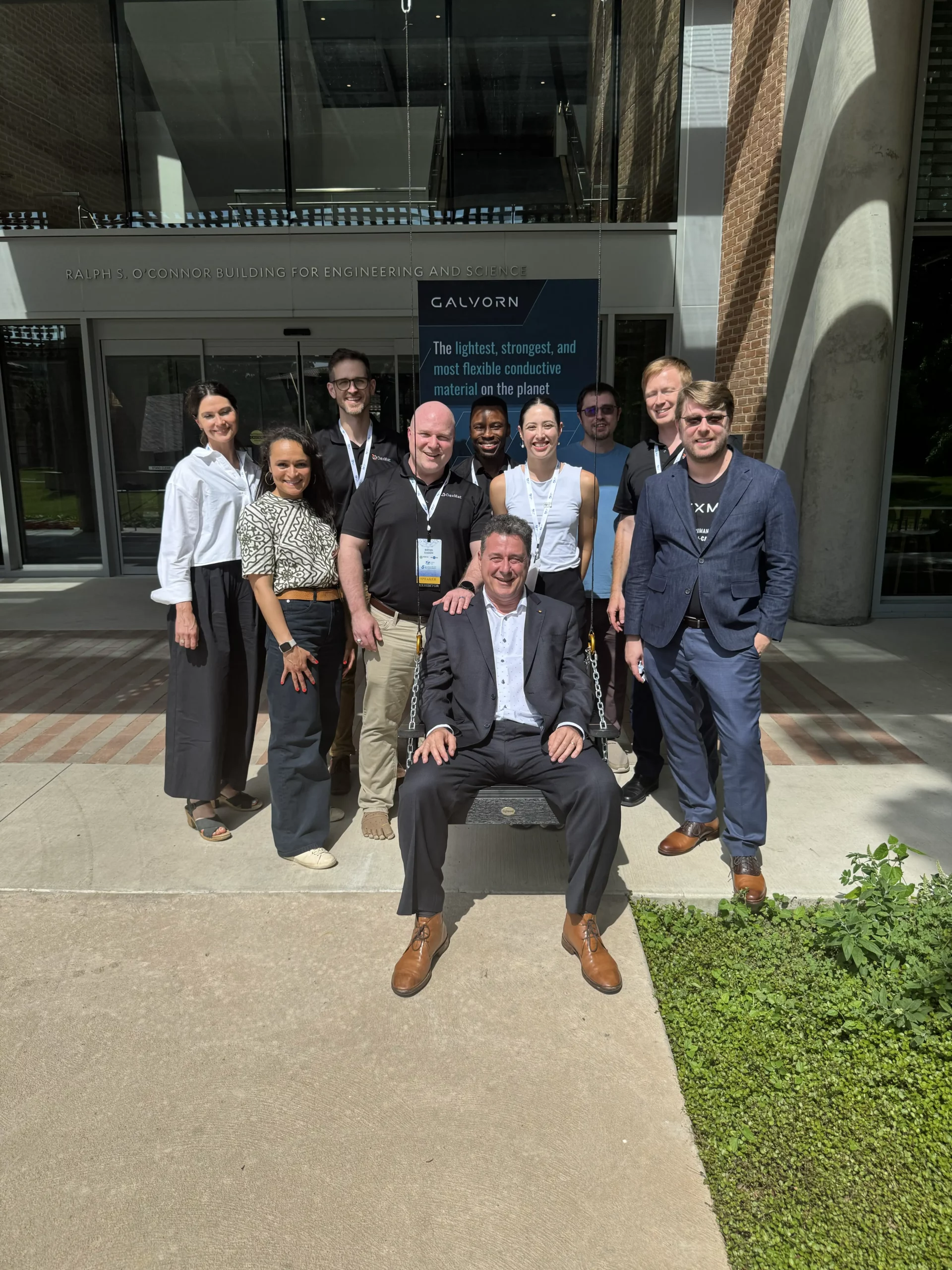
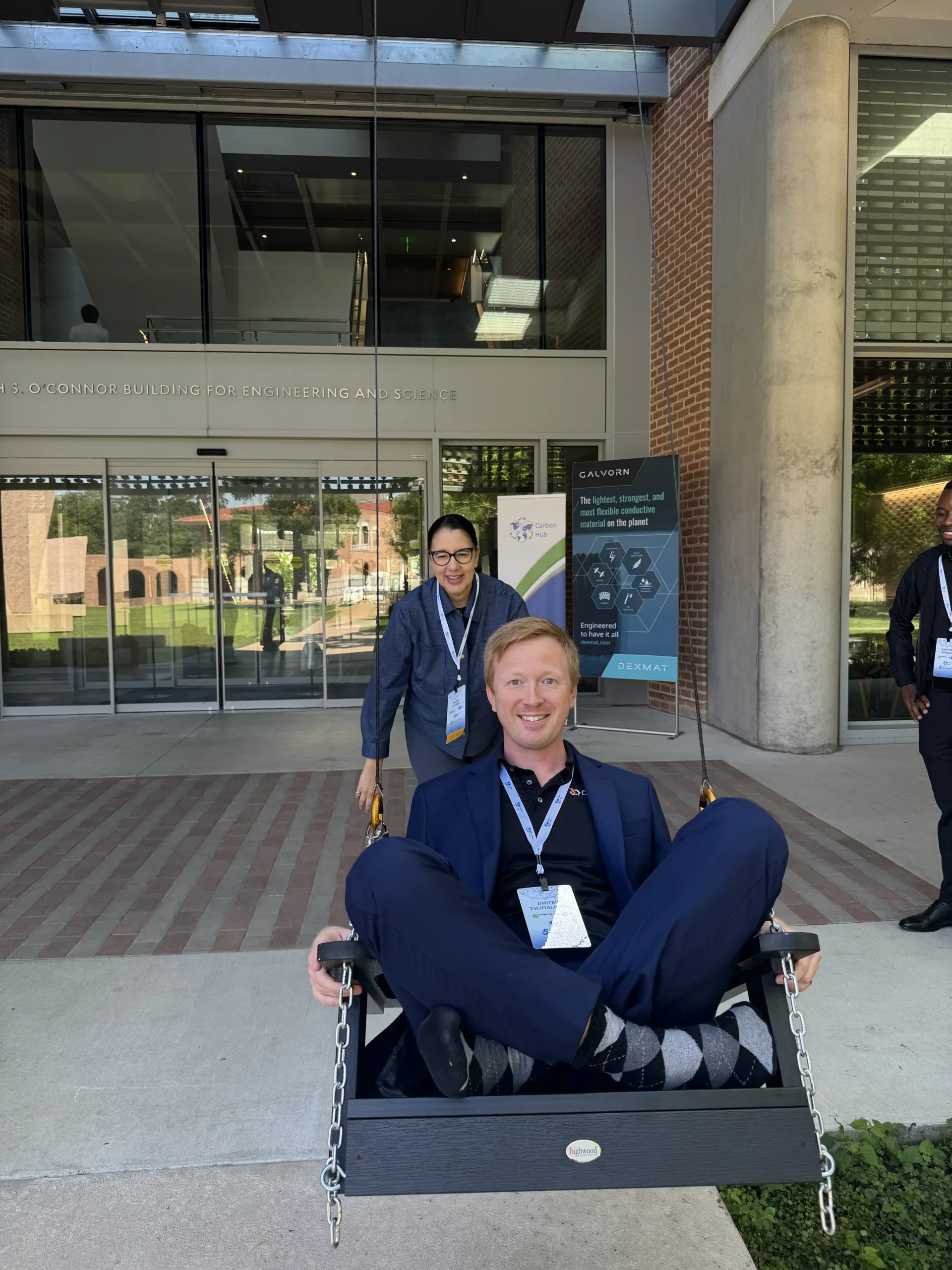
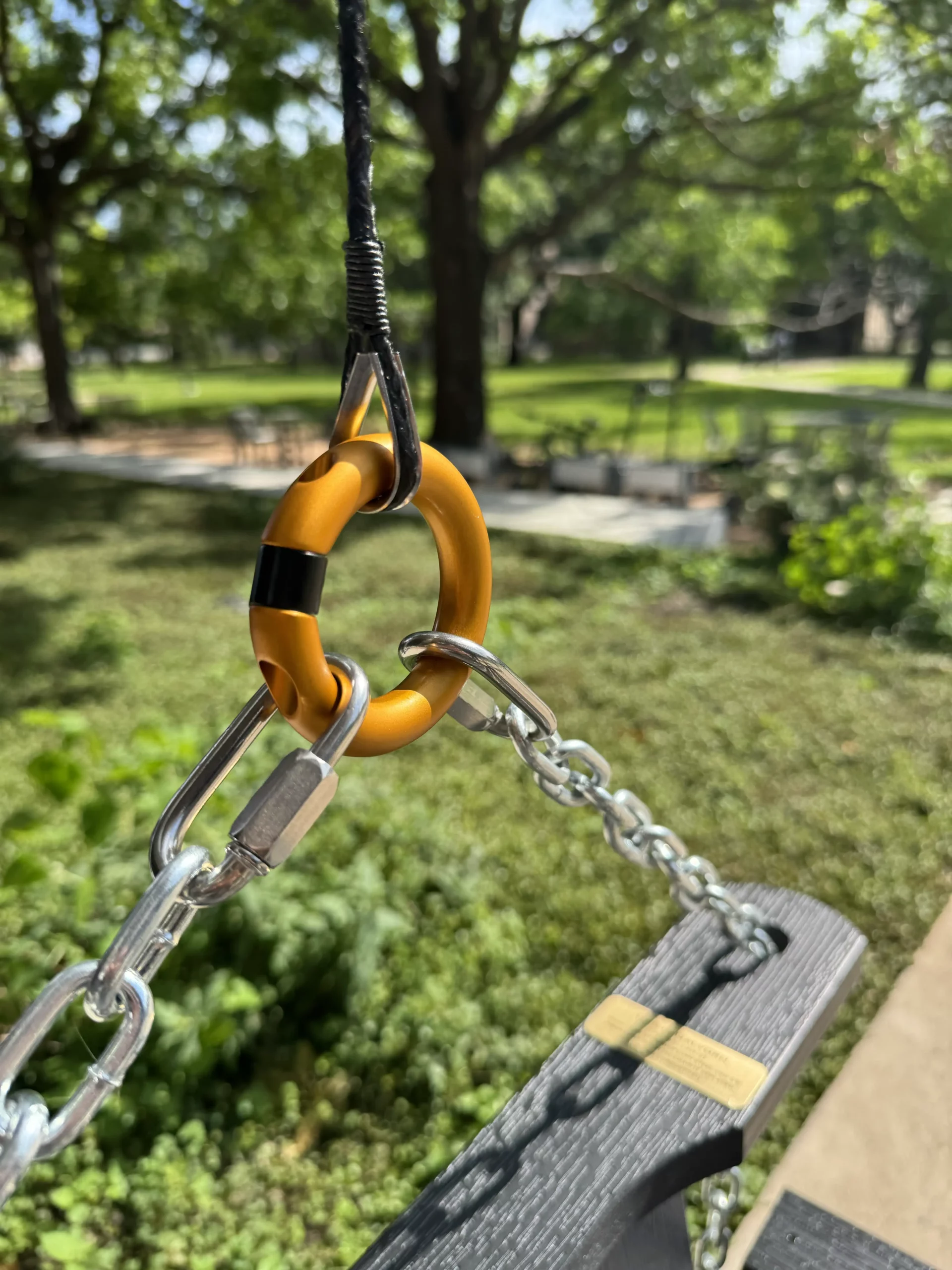
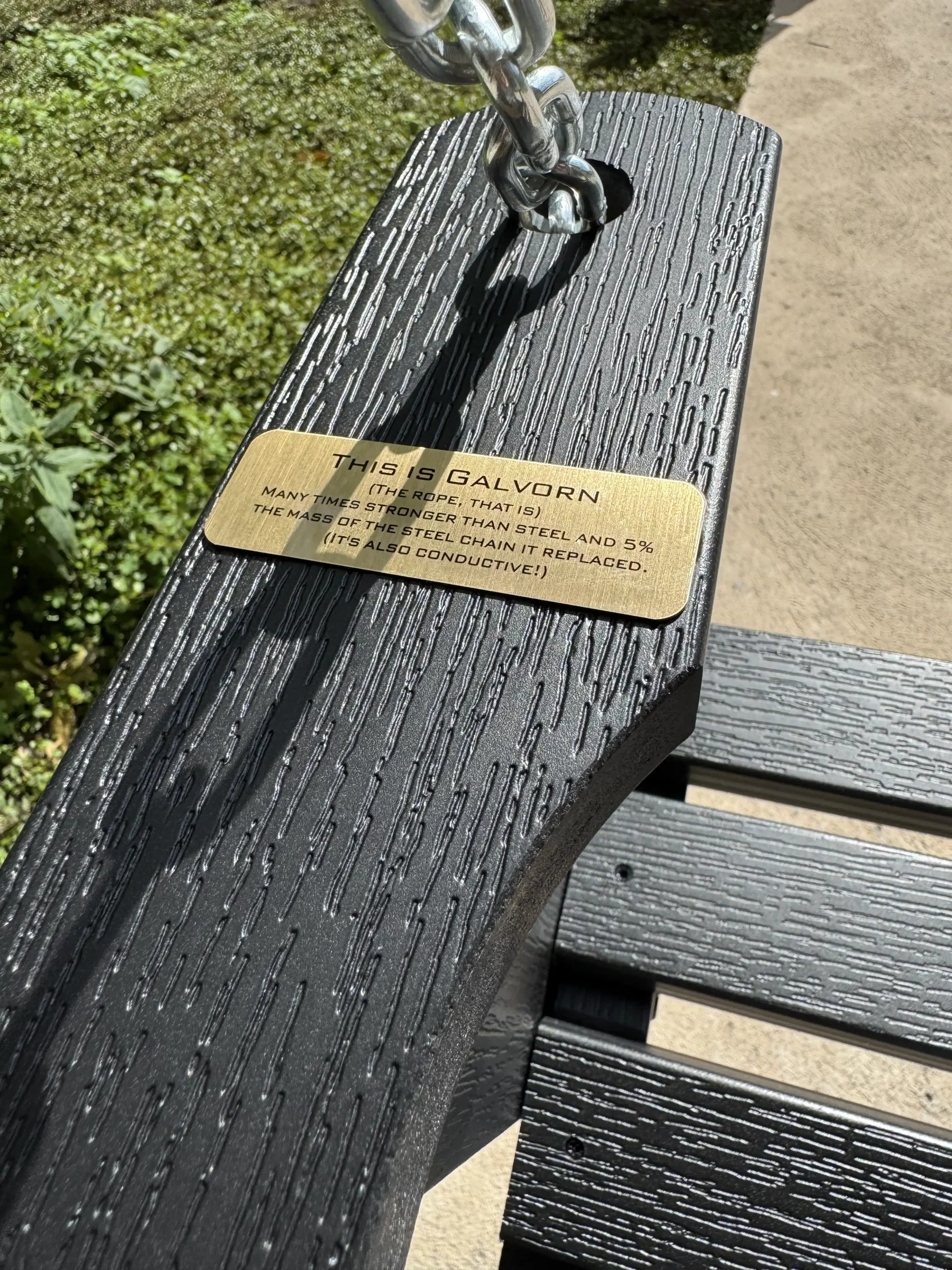
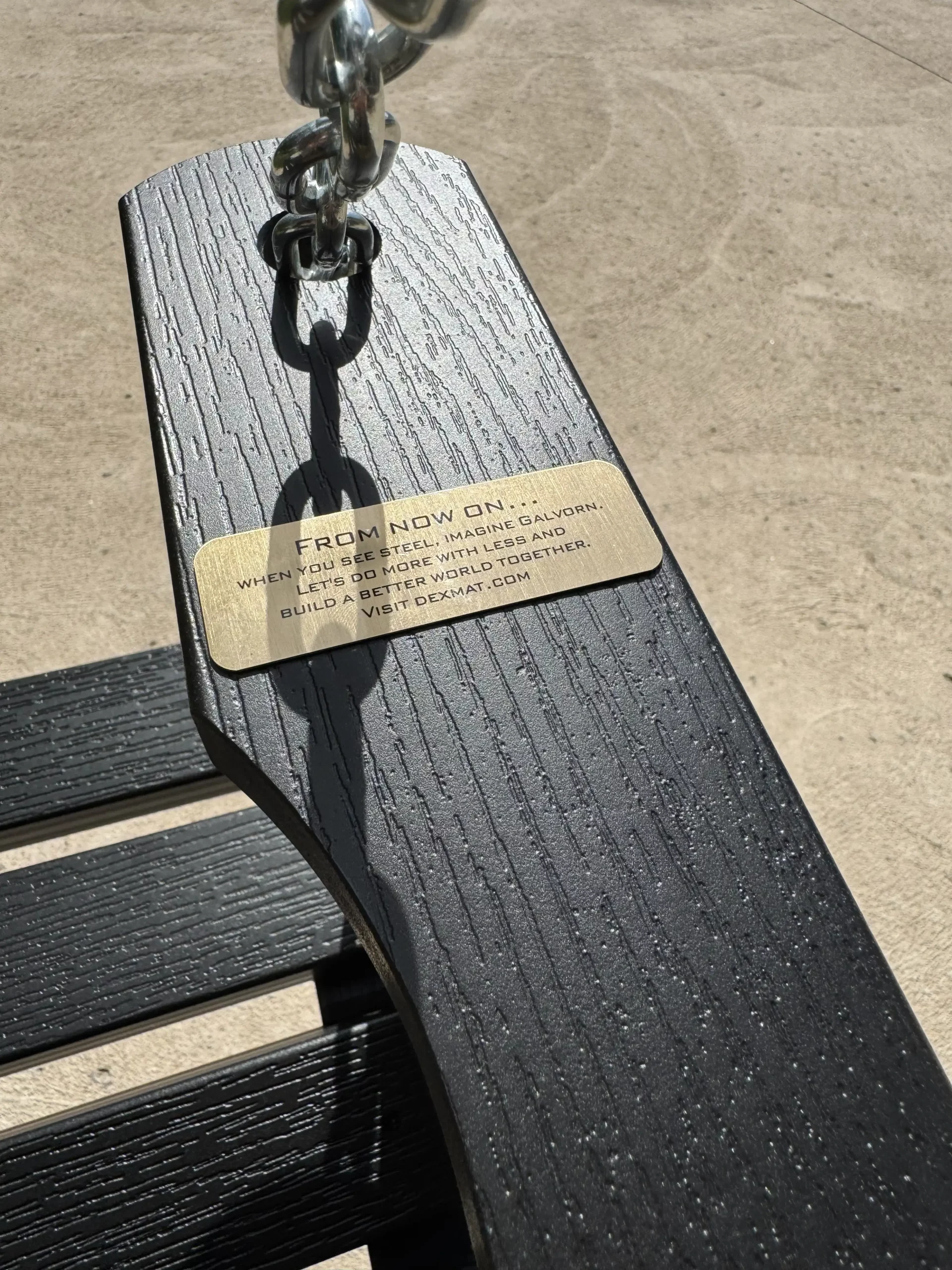
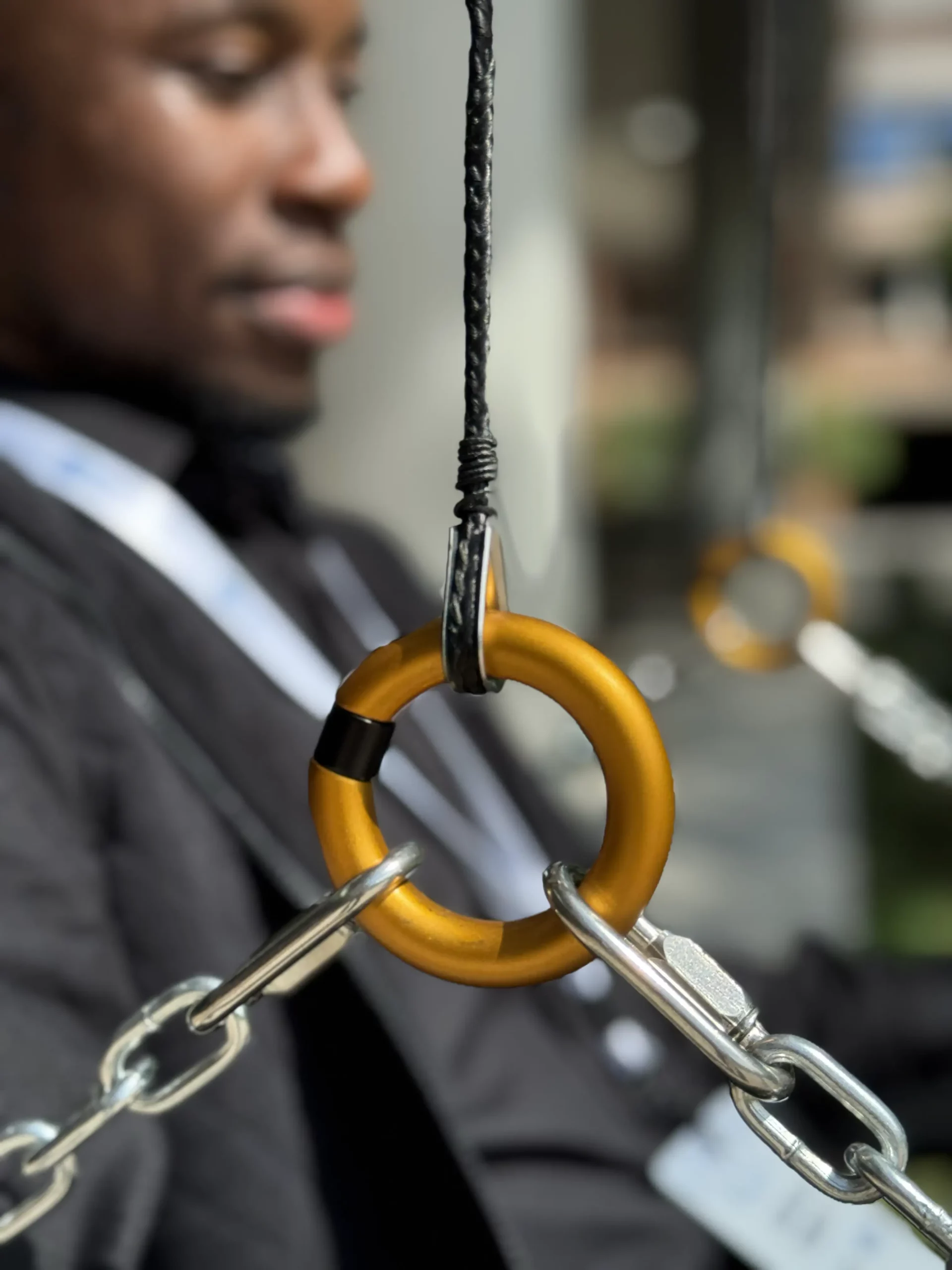