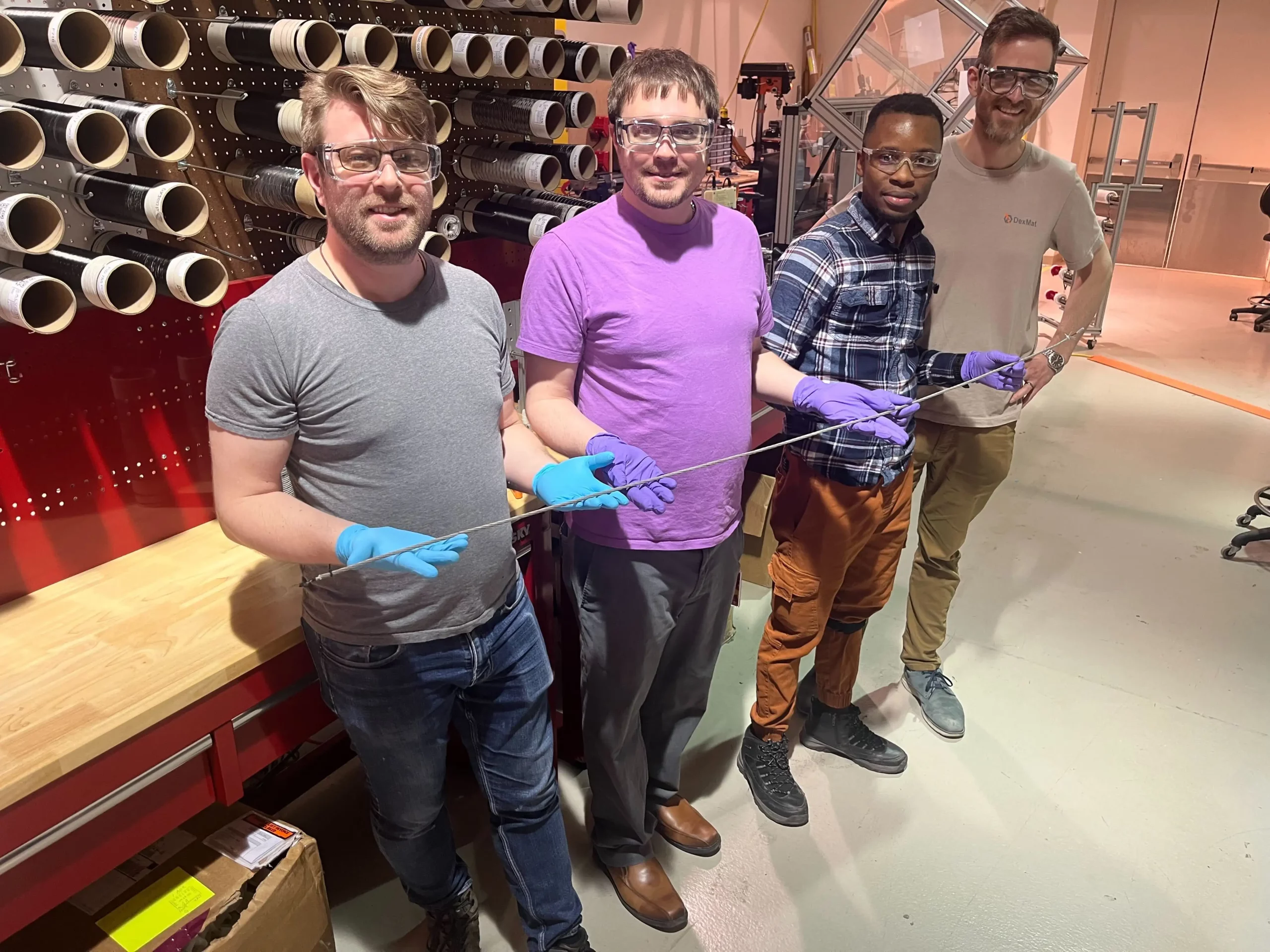
Modern economies require more electricity. Yet, according to the U.S. Department of Energy, “70% of transmission lines in the United States are over 25 years old, and approaching the end of their typical 50–80-year lifecycle. This has major consequences on our communities: power outages, susceptibility to cyber-attacks, or community emergencies caused by faulty grid infrastructure.” One of the key ways we modernize our grid is through re-conductoring: replacing existing power lines with new, higher-capacity advanced conductors, boosting transmission capacity and efficiency without requiring new infrastructure or land acquisition.
To that end, DexMat has been working with Prysmian as part of a DOE-funded grant to develop the next generation of advanced conductors: an Aluminum Carbon Nanotube (ACNT) fiber conductor.
Galvorn ACNT will be stronger, lighter, and more resilient to extreme weather than traditional conductors, improving the electric grid's reliability for Americans across the country.
In this post we’ll discuss:
- The limitations of existing overhead transmission conductors
- The improvements that Galvorn ACNT conductors promise
- And share the latest updates from our project, including better than expected results!
The Challenges with Traditional Conductors
An Aluminum Conductor Steel Reinforced (ACSR) conductor, is the dominant type of high-capacity electrical conductor used in overhead power lines today. It consists of a core made of steel strands surrounded by layers of aluminum strands. Much of the U.S. electric grid was built in the 1960s and 1970s and these were the readily available materials.
The steel core provides structural strength and support, allowing the conductor to withstand tension, wind, and the weight of long spans between poles or towers. Meanwhile, the aluminum outer layers serve as the primary conductor of electricity, leveraging aluminum’s lightweight nature and excellent conductivity.
This combination makes ACSR conductors durable, cost-effective, and capable of carrying high currents over long distances, which is why they’ve been a standard in electrical grids since the early 20th century. However, ACSR, does have its limitations, namely:
- Limited Current Capacity: Max operating temperature of 75–90°C restricts ampacity, capping how much power it can carry compared to modern needs.
- Thermal Sag: Expands and sags significantly when heated, reducing clearance and risking outages or safety issues.
- Higher Weight: Steel core adds heft, increasing stress on towers and requiring sturdier (costlier) support structures.
- Energy Losses: Greater resistive losses at high loads due to thermal limits, lowering efficiency (e.g., 5–10% more losses than ACCC).
- Corrosion Risk: Steel core can rust in wet or salty environments, shortening lifespan and raising maintenance costs.
- Less Adaptable: Struggles with variable, high-capacity loads from renewables, limiting its role in grid modernization.
An Aluminum Conductor Composite Core (ACCC) conductor, is an advanced type of overhead power transmission conductor designed to replace traditional options like ACSR. It features a hybrid core made of carbon and glass fibers embedded in a high-strength polymer matrix, surrounded by strands of high-purity, annealed aluminum.
The composite core provides greater strength and lighter weight compared to steel, while allowing the conductor to operate at higher temperatures—up to 180–200°C versus the 75–90°C limit of ACSR—without significant sagging. This high-temperature, low-sag (HTLS) capability, combined with the aluminum’s excellent conductivity, enables ACCC to carry roughly twice the current of ACSR of the same diameter, making them ideal for boosting capacity on existing lines without replacing towers. They’re also more resistant to corrosion and fatigue, promising a lifespan of 40–50 years or more. Used in over 1,000 projects globally, including many in the U.S., ACCC conductors help utilities meet rising demand, though one of their key limitations comes down to complexity (and by extension, cost), ACCC requires:
- Specialized Handling: Requires trained crews and specific tools for installation, unlike the familiar ACSR process.
- Repair Complexity: Damage to the composite core can be trickier to fix, potentially raising downtime or costs compared to ACSR’s simpler splices.
Technological advancements continue to be made with carbon fiber core conductors, but the fundamental fact that carbon fiber and glass are materials that must be carefully handled will limit broad adoption. We need solutions that are better performing and less complex to produce and install.
Top 3 Reasons for Galvorn Advanced Conductors
With a new Galvorn Aluminum Carbon Nanotube (ACNT) conductor our goal is to improve performance, and by extension reduce cost. Our work will increase the advanced conductor’s thermal and electrical conductivity, reduce weight, and increase breaking and tensile strengths. These improvements will make overhead transmission line more resilient to extreme weather and heat. It will also reduce the cost of installation by minimizing the number of support towers needed, if extending the grid; or simply putting less strain on existing support towers because the conductors are less dense. Below we highlight the top three reasons Gavorn will be a better solution for grid modernization:
#1 Better, more resilient transmission lines
Galvorn stands out in advanced conductor and transmission line applications due to its exceptional flexibility and resistance to flex fatigue, making it more durable under mechanical stress. Its sag performance is expected to be significantly better than ACSR because of Galvorn's very low coefficient of thermal expansion, reducing the risk of lines drooping under heavy loads or high temperatures while offering a more familiar installation process for grid operators. By enabling higher aluminum content without adding weight, Galvorn reduces losses and enhances efficiency. Additionally, its greater flexibility compared to carbon fiber composite cores makes it more resilient under ice load conditions, addressing key challenges in cold climates. Galvorn’s high thermal conductivity also helps dissipate heat efficiently, ensuring stability under high-capacity loads — a critical advantage for grid reliability in extreme weather.
#2 More cost-effective installation
Galvorn conductors will be easier to install, which ultimately means less expensive to install. As noted earlier, one of the challenges with ACCC is its upfront cost of installation. Carbon fiber and glass have exceptional tensile strength, but over-torqueing the carbon fiber composite cores during installation can lead to failure of the entire core. This makes handling and installation more complex, given that overhead power lines are fundamentally always under tension.
Galvorn is flexible, lightweight solid carbon with exceptional tensile strength. In fact, Galvorn does not require epoxy or resin, as its flexibility and inherent strength allow it to be used in its “raw” state. This simplifies manufacturing / installation, retains strength, reduces weight, and eliminates the brittleness issues associated with carbon fiber composite cores. Also, without epoxy, Galvorn can tolerate higher temperatures such that the maximum current rating goes up.
#3 Galvorn can be produced using an abundant feedstock: American natural gas
Galvorn is a solid carbon produced by densely packing and aligning carbon nanotubes into “wet-spun” fibers. The carbon nanotube feedstock can be produced through methane pyrolysis, splitting methane (CH4) into carbon (C), in this case CNTs, and hydrogen (H2). Given that 70-90% of natural gas is methane, we have an incredible opportunity to modernize our grid with materials made from a resource abundantly available in the U.S. The clean hydrogen byproduct would further support our energy dominance by providing an energy-dense fuel without the carbon dioxide emissions.
Gray hydrogen is cheap, but misses an opportunity to unlock a high-value market
Today “gray” hydrogen makes up over 75% of today’s hydrogen market. It is produced through a process called steam reforming. Methane gas is reacted with high-temperature steam in the presence of a nickel catalyst. This reaction produces hydrogen gas and emits carbon dioxide into the atmosphere.
For these reasons, Galvorn has the potential to greatly improve the performance and cost-efficiency of our much needed grid modernization. Consider these benefits:
- Ultra-Long Spans: Higher strength-to-weight ratio for long spans and challenging terrain.
- Extreme Environments: Flexural tolerance and durability outperform brittle carbon fiber under high wind, ice, or temperature cycles.
- Faster/Less Expensive Installation: Flexural tolerance and durability enable faster and less error-prone installation of conductors above and below ground.
- Grid Efficiency: Supports higher aluminum content without added weight, enabling lower losses and reduced sag in high-capacity grids.
- Production Efficiency: No resin requirement and a less energy-intensive production process align with cost- and energy-efficiency targets.
Galvorn ACNT Conductors: Development Update
Our project to develop Galvorn overhead transmission conductors begins with the design, development, and fabrication of a prototype at DexMat’s facilities. To that end, our first test of a 10m braid demonstrated more than 20% higher specific strength than a carbon fiber composite core. This initial braid achieved 1.7 N/tex specific strength, while being able to withstand more than 2x lower bend radius than a composite core.
For our prototype we developed a Galvoron core braid with 1.7 N/tex strength, shown below.
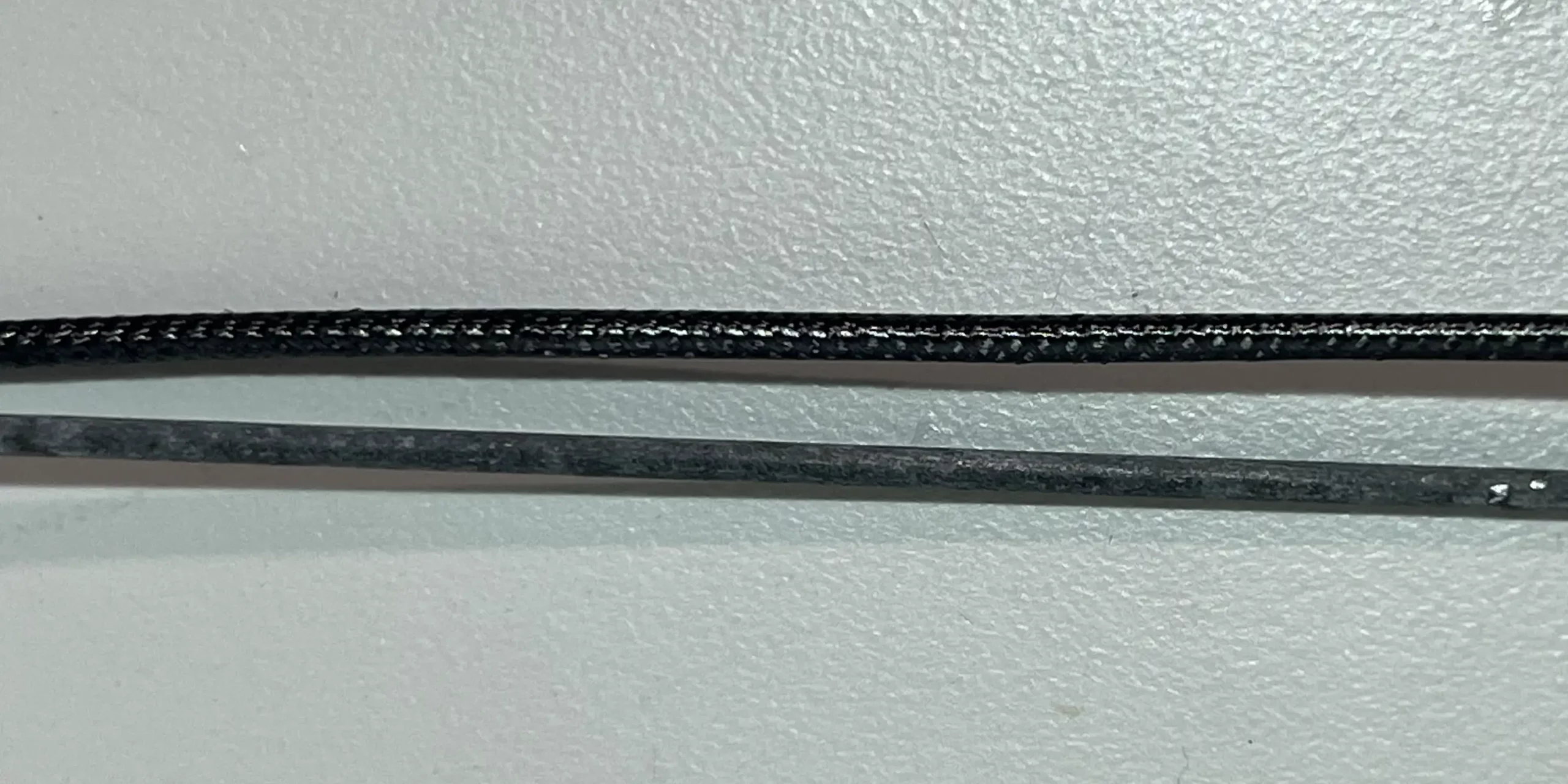
Above: Galvorn braided core with 1.7 N/tex (top) to be used in the new ACNT and a traditional steel core (bottom) used in ACSR.
That braid was then wrapped in aluminum conductor:
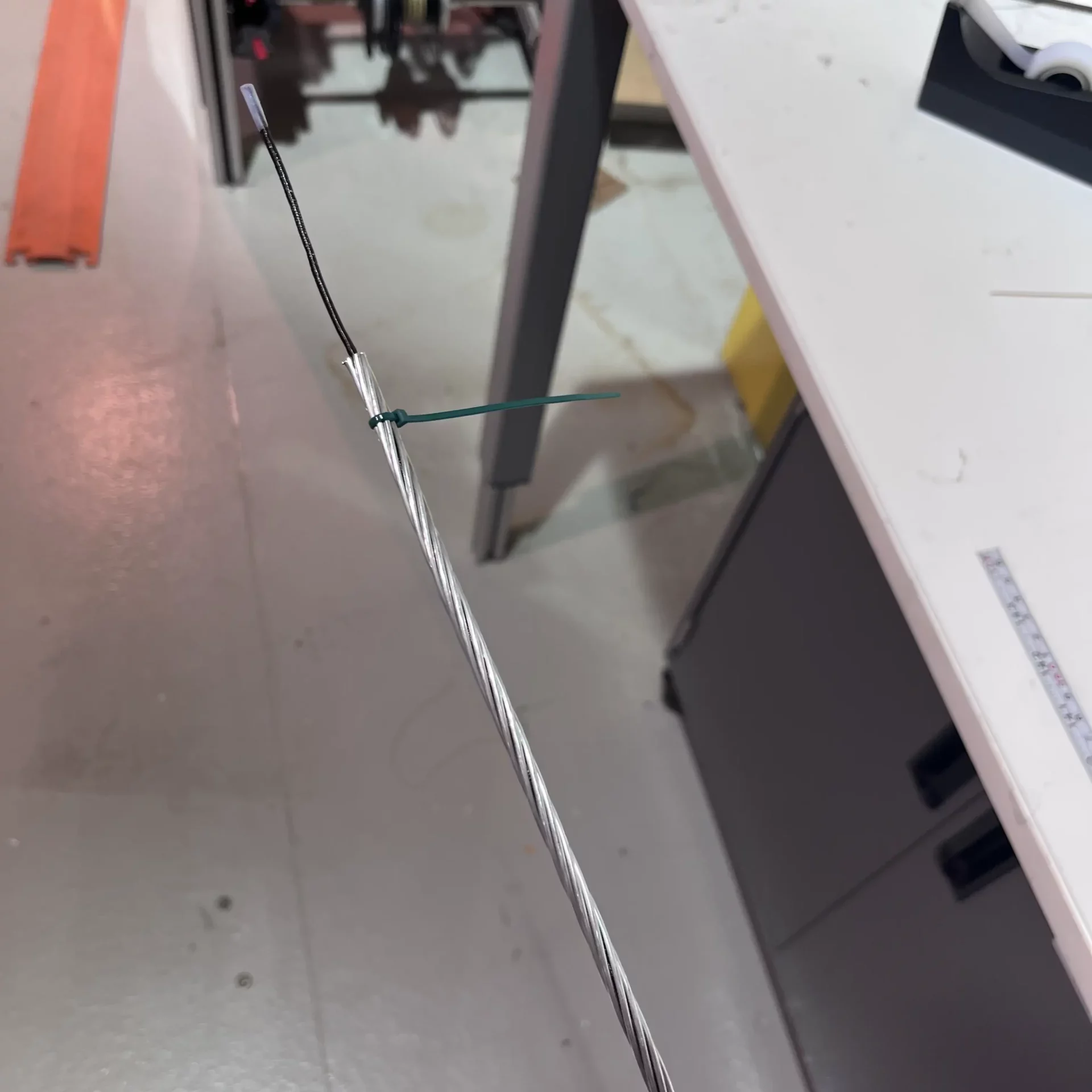
And below is our first ever power transmission line prototype with a Galvorn core! The prototype is equivalent in size to the smallest type of ACSR cable. We made that size as a first step.
In the next phase of our project, we’ll aim for a larger diameter and a much longer sample! For now, this prototype will be tested by our partner, Prysmian, at their facilities.
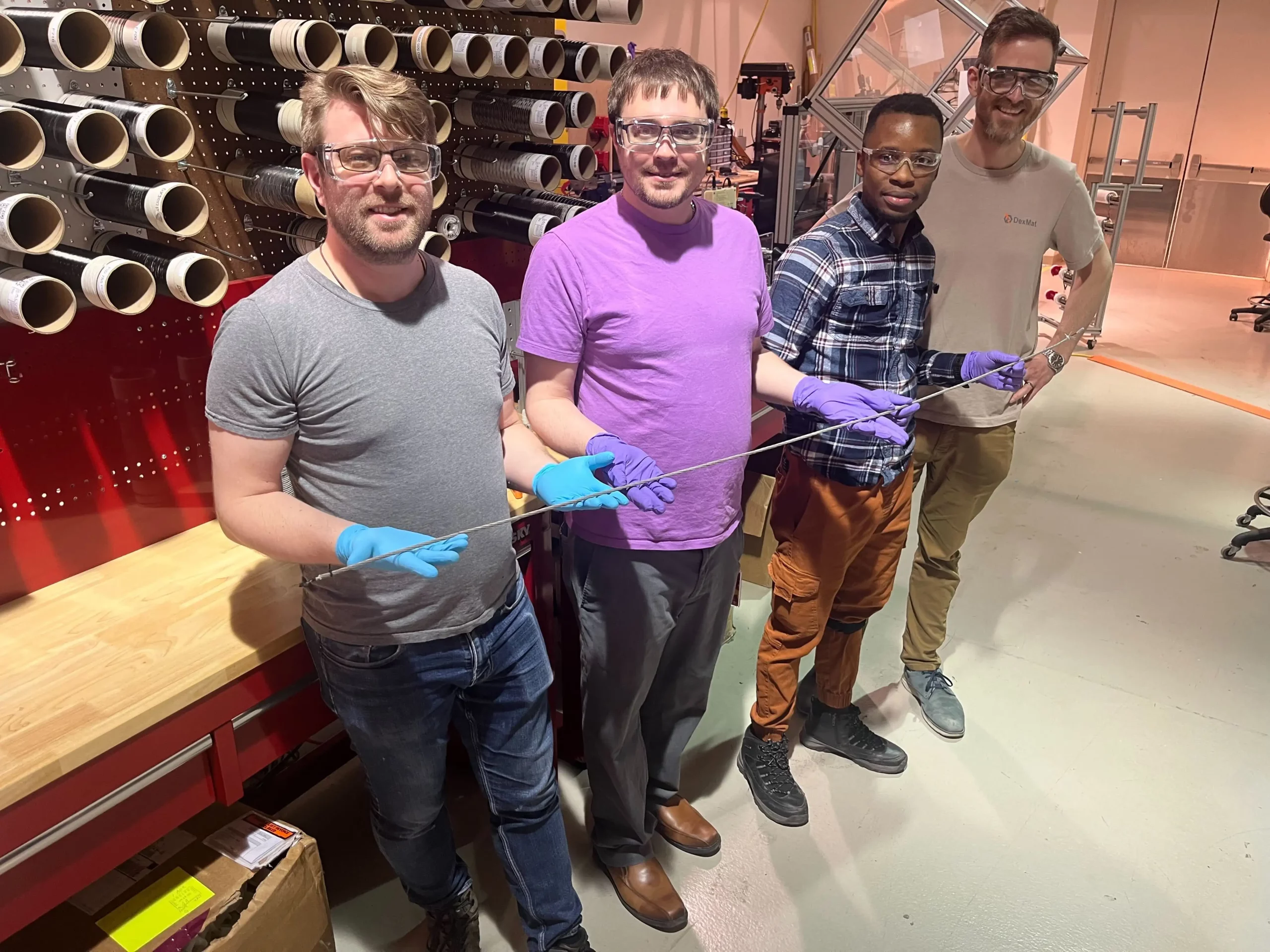
Below is a table comparing the properties of these different conductors. We include the current (initial) testing of our braid, as well as what is technically feasible today, as well as in the near future: the fiber properties will improve with additional processing improvements, which have already been demonstrated and published by Matteo Pasquali, PhD, and his team of researchers at Rice University. Professor Pasquali is a DexMat co-founder and our Chief Science Advisor.
Core properties | Core density (kg/m3) | Core tensile strength (GPa) | Core specific strength (N/tex) |
Steel used in ACSR | 7804 | 1.45 (rated) | 0.19 |
Carbon composite used in ACCC | 1864 | 2.55 (rated) | 1.37 (rated) |
Galvorn CNTF in ACNT Current Braid Testing Results | 1300 | 2.21 | 1.70 |
Galvorn CNTF in ACNT
Our best fiber properties, aka what is technically feasible with our fibers today. |
1600 | 3.0 | 2.00 |
Galvorn CNTF (2-3 years) in ACNT
Our fiber properties in 2-3 years with processing improvements, aka what is theoretically possible within the near future. |
1700 | 6.6 | 3.8 |
Testing Update: March 24, 2025
The results from Prysmian's testing have come in since first publishing this blog. Their testing found that the Galvorn conductor was 43% stronger than a traditional Turkey ACSR conductor, while being only 75% of the weight! This is only the very first protoype so we can expect even more improvements as we continue the work.
A Better Grid, Sooner: Why We Do This Work Now
As is often the case with new materials, the need for better performance is not what limits adoption, rather it’s the cost. Yes, Galvorn on a per mass basis is today more expensive than carbon fiber and steel. But our technoeconomic analysis finds that we can bring Galvorn production costs to significantly below both of these incumbent materials. It will not happen overnight, but by 2030 we anticipate being able to outcompete ACSR and ACCC conductors based on both performance and cost. By doing the development work now, in partnership with Prysmian, one of the world’s leading producers of conductors for the energy sector, and in parallel with our production scaleup, we are in an ever stronger position to bring Galvorn conductors to these critical grid modernization projects sooner.