For High-Performance Textiles, E-Textiles, and Composites
At DexMat we have experimented with the patterns discussed below to develop fabrics from our Galvorn conductive yarns and films for both e-textile and composite applications. We share our learnings below for customers that are developing these types of applications with Galvorn.Â
Fabric is traditionally defined as a woven material, typically cloth made from textile fibers, used to create garments. Its flexible, overlapping threads provide both comfort and durability.
Beyond clothing, fabric structures are also crucial for structural composite components, particularly in carbon nanotube composites. Unlike brittle and rigid carbon fiber, Galvorn carbon nanotube (CNT) fibers, yarns, and films are exceptionally flexible. This textile-like behavior gives Galvorn CNT products a significant advantage in forming dynamic composite shapes, as the woven CNT fabric can easily adapt to complex molds.
Whether for clothing or composites (where fabric is combined with an adhesive filler medium), fabrics are created by precisely placing strands of fibers, yarns, and films within a weave to achieve a specific structure.
The combination of electrical conductivity, lightweight nature, and ultra-high tensile strength in Galvorn CNT fibers, yarns, and films is poised to revolutionize the design of high-performance textiles, e-textiles, and composites.
It’s all about the weave
Fabrics derive their unique characteristics and purpose from various weave styles. Each weave style is determined by how two basic categories of strands, warp and weft, are interlaced. Warp strands run lengthwise and continuously throughout the fabric. Weft strands, on the other hand, cross the fabric's width, passing over or under the warp strands in specific patterns to create the desired weave style.
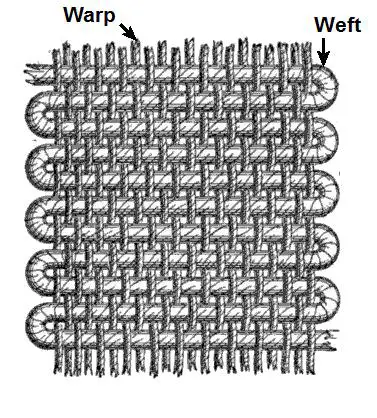
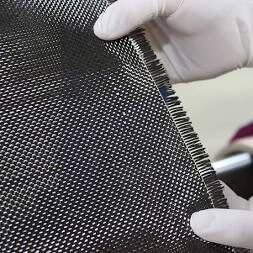
Above: (Left) Warp vs. Weft; (Right) Galvorn CNT fabric weave.
Fabrics are created using a variety of weave styles, each with its own variations. While these styles were initially developed for cloth production, their versatility extends far beyond simple garment construction. In fact, many weave styles used in composite fabrics for structural applications are variations of those found in the clothing and textile industries.
Plain Weave
The plain weave is the most basic weave, consisting of a 1 x 1 pattern produced by a weft strand going over and then under each alternating warp strand. This weave has the highest frequency of over and under passes and is considered to be strong from a cloth standpoint, but not the best option for all composite use.Â
Due to the frequent weft and warp intersections, this dense weave is highly stable and less prone to fraying. It excels on flat surfaces, but it is less pliable and thus challenging for complex 3D composites. For garments, plain weave is a common choice for linens and similar simple fabrics.
Twill Weave
The twill weave, a versatile pattern, is created by two or more weft strands interlacing over and under one or more warp strands. A basic 2x2 twill weave involves two weft strands alternating over one warp strand, a process that can be expanded to a 4x4 twill weave and beyond.
This weave is characterized by a distinct diagonal line on the fabric's face, with a smooth reverse side. The twill weave results in a durable, heavier fabric that is less prone to wrinkling than a plain weave. Its pliability allows for excellent draping, making it suitable for intricate composite molds and comfortable apparel.
Common applications include denim, flannel, and jersey. While twill weave fabric is susceptible to fraying at the edges and requires careful handling, its properties make it a viable option for complex 3D molded composites. Again, the flexibility of Galvorn carbon nanotube fabrics unlocks a lot of design flexibility for composite structures!
Dual Twill
The dual twill weave creates hybrid fabrics by using multiple materials, similar to a standard twill weave. It's formed by two weft strands alternately passing over and under the same two warp strands, much like a 2x2 twill. However, both the weft and warp strands incorporate two distinct fabric types. For instance, in an illustrative example, every other warp and weft strand could be made of an alternative material.Â
This weave offers the potential to integrate carbon nanotube (CNT) fibers or yarns with either a conventional textile strand, or a carbon fiber strand. This capability could lead to conductive pathways in wearable garments or electrically enhanced composites.
Satin weave
Satin weave is characterized by weft strands passing over three and then under one warp strand. This creates a fabric with continuous warp strands, resembling the continuous back-and-forth movement of weft strands.
Highly adaptable, the satin weave can achieve increased flexibility by varying the over-count to four or even six warp strands. The low frequency of interruptions between weft and warp strands results in a smooth and flexible structure. However, due to the long runs of fibers without transitions, satin fabric is prone to snagging and requires careful handling.
Commonly, silk and nylon fibers are used with this construction to create an elegant feel in high-end garments and cloth. Carbon fiber composite manufacturers also favor this weave due to its exceptional pliability, which surpasses that of twill, making it ideal for molding into complex curved forms and 3D shapes.
Jacquard weave
The jacquard weave, a complex variation of the basic 1x1 plain weave, is produced on specialized looms. These looms utilize either electronic controllers or mechanical punch cards to precisely lift individual warp strands, enabling the creation of intricate patterns or images within the fabric. The flexibility and durability of the jacquard weave can vary, depending on the intended design and the number of intersections the weft strands form to achieve the desired pattern. This weave is a popular choice for drapery and upholstery.
While less common in the composites industry, it is particularly well-suited for finished products made from materials like carbon fiber that require elaborate designs on the composite's surface.
Additionally, the jacquard weave offers the unique capability to incorporate Galvorn CNT yarns, facilitating the creation of woven circuits or designated sections for high wear resistance or electronic interfacing components.
Fabrics with Galvorn CNT Fibers and Films
The array of available weaves makes it clear that no single weave can serve every purpose. Weaves designed for clothing prioritize flexibility and aesthetic appeal, often featuring varied construction. In contrast, weaves for composites emphasize fundamental mechanical strength alongside the flexibility needed for shaping machine parts.
CNT Weaves for Cloth Fabrics
Galvorn CNT yarn, which can be handled like traditional textile thread, can be woven with conventional yarns to create textiles with electronic functionalities, all without compromising comfort, or adding weight (more likely, reducing weight). This opens up possibilities for wearable devices, from heating elements in clothing to power generation and feedback for mobile devices, and even wearable skin-contact electrodes for health monitoring (ex. monitoring heart rate).
Using a jacquard loom, this material can be woven to directly integrate capacitive touch sensing pads into the fabric, as demonstrated here. This means that any part of a clothing design could also function as a built-in touch-sensitive button.
Beyond electronic applications, the purely mechanical properties of aligned CNT woven fabric offer other uses. For instance, a dual twill weave can create cut-resistant garments and lightweight, flexible bulletproof clothing from CNT fibers or high-strength polymers like Kevlar. The specific weave style or combination of patterns in layers will be crucial in optimizing performance, as each application will have its own unique demands for flexibility and overall strength.
Galvorn CNT Weaves for Composite Fabrics
CNT yarns and films can also be woven into a stand-alone fabric to use for composite construction, such as the prototypes shown here. Below we also show a woven plain weave sample made from 1 cm wide Galvorn CNT film.Â
Fabrics suitable for composite materials can also be made out of CNT fiber (see the image above in the previous section). This 100% CNT fabric could potentially take the place of traditional carbon fiber composites, with the added benefit of increased electronic conductivity. Applications that need high strength and lightweight composites could also turn to composites made from CNT yarns and films to add in EMI shielding, utilizing the conductivity of the CNTs to block and limit electromagnetic signal interference. Learn more about Galvorn EMI shielding here.
Above: A plain weave sample made from 1 cm wide Galvorn CNT film.Â
This serves as a basic introduction to the potential applications of woven materials made from Galvorn CNT fibers and films, which include all the fabric weaves listed here. Galvorn fibers and films are conductive, durable, flexible, and lightweight, making them ideal for the developing field of wearable electronics and highly adaptable for advancing the electronic interfacing of composite materials.